Introduction
Electromagnetic (EM) forming is a high speed forming process developed in the 1950-60’s to obtain shapes from sheet metal that could not be obtained using standard forming techniques. Interest in EM forming of sheet metal for automotive applications has been growing in recent years, due to its potential as a means of forming aluminum and other low formability materials. Forming of aluminum has been the main focus, due to its inferior forming characteristics relative to mild steel and its potential to reduce automobile weight. Several studies have indicated that the formability of aluminum increases when it is formed using high-speed processes like EM forming.
The electromagnetic forming process takes advantage of the repelling force that is produced between two opposing transient magnetic fields. A typical EM forming operation begins by charging a capacitor bank to the voltage required for the specific operation and then discharging it through a coil that is in close proximity to the workpiece, be it a tube, or flat or pre-formed sheet metal. A current pulse flows through the coil, generating a transient magnetic field. This magnetic field in turn generates a time-varying current in the conductive workpiece, which generates a magnetic field that opposes the field of the coil. The magnetic fields repel one and other, generating a body force, called the Lorentz force, on the workpiece that propels it away from the coil.
Increased Formability
Research at the University of Waterloo has shown that the formability of certain aluminum alloys (AA 5754 and AA 6111) increases under specific conditions when formed using EM forming. It has been determined that the interaction with of the fast moving sheet with the die is an important factor in the increased formability. This is illustrated by the modest increases in formability observed in AA 5754 that has been free-formed (i.e. formed into the air with no die) and the significant formability increase observed when the sheet is formed into a conical cavity die. This behaviour is attributed to an "inertial ironing" effect produced by the impact of the sheet and the die , which results in highs through thickness normal and shear stresses. Also, the strain rates in excess of 104 s-¹ produced by the process are believed to have an effect on formability.

Formability results of AA 5754 free-formed 1 mm sheet
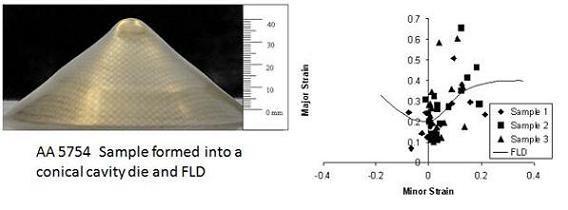
Formability results of AA 5754 1 mm sheet formed into a conical cavity die
Numerical Modeling Capabilities
Numerical modeling is needed to properly understand EM forming; especially, to analyze the complex stress and strain histories that are generated on the sheet metal during EM forming. The process is modeled using a commercially available LS-Dyna with EM capabilities. The EM solver uses Finite Element Method (FEM) for the solids and Boundary Element Method (BEM) for air. The work carried out has shown that there is good agreement between the predicted and experimental results.
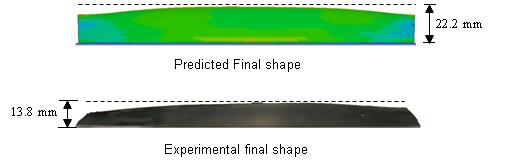
Predicted shape compared to the experimental sample

Experimental sample and numerically predicted final sample
Hybrid Electromagnetic Forming
Hybrid EM forming combines conventional and EM forming operations with the goal of obtaining features that cannot be obtained using conventional forming alone. A schematic representation is shown below. In the operation researched at the University of Waterloo the workpiece is pre-formed using conventional stamping techniques to an outer radius of 20 mm and then EM forming is used to reduce the radius to 5 mm. Using the hybrid process, the formability of the material was increased, as can be seen in the Forming Limit Diagram (FLC) presented, which shows data for experiments with sheets that were pre-strained to 15% strain prior to the hybrid forming operations. The process proved successful and could potentially be used in industrial applications.
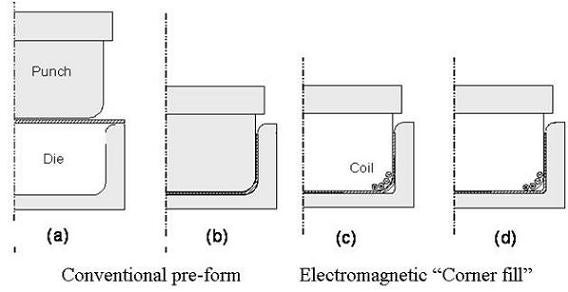
Schematic of a hybrid electromagnetic forming process
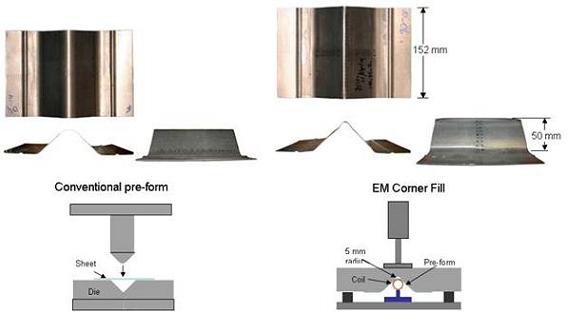
Experimental samples after conventional pre-form (left) and after EM corner fill (right)
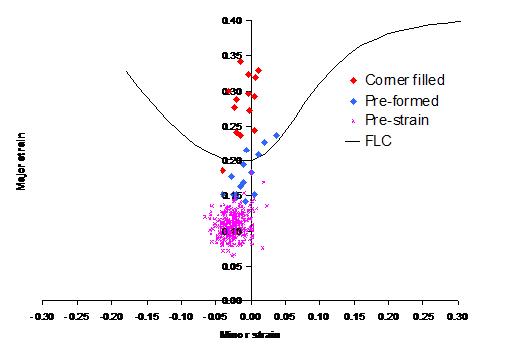
Forming limit diagram showing the results of hybrid EM forming of 1 mm AA 5754 sheet pre-strained by 15%. The forming limit curve (FLC) is for conventionally formed AA 5754.