The triple acting servo-hydraulic press at the University of Waterloo can be used to conduct forming experiments; such as warm forming, non-isothermal forming, deep-drawing and stretch-flanging. A die is held stationary while the punch and blank holder (BH) are moved by the two hydraulic actuators. An optional backup punch can be added when required. The punch, backup punch and BH movements are displacement-controlled or force-controlled, respectively. Load cells located between the actuators and their respective tooling measure the actuator force. The tool displacements are measured with linear variable differential transformers (LVDT). Each actuator is controlled by a MTS 407 controller which is interfaced to a Labview program. The apparatus is equipped with a custom-built temperature control system that enables independent temperature control of the tooling. Experimental data is recorded via a data acquisition card attached to a PC.
Specifications:
- Main punch cylinder capacity = 200 kip
- Main punch calibrated load = 110,000 lbs
- Main punch force = 125,000 lbs
- Main punch stroke = 7.32"(186.0mm)
- Back up punch load cell capacity = 100 kip
- Back up punch stroke = 8"
- Warm forming up to 300ºC
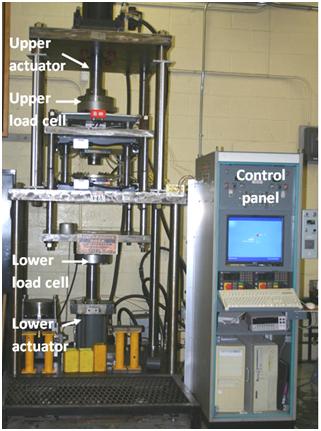