Introduction
Tailored blanking is a relatively new method of producing automotive structural components. It involves seam welding together two or more separate sheet metal pieces to form a composite blank. This approach allows the designer to combine different gauges, and even different alloys in the same blank. The formed sheet metal part can than be optimized for weight and function, while reducing waste material, assembly time and even design effort. Current applications of tailored blanks allow designers to amalgamate stamped and welded assemblies of numerous separate pieces into one part. Applications include any part or assembly that require different properties in different locations.
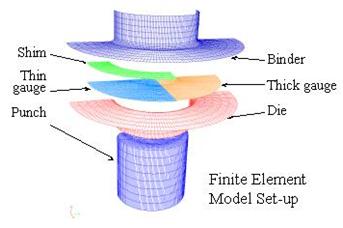
Deep drawing finite element model meshes
TWB Formability
Formability data is collected from limiting dome height tests and deep drawing tests. Various combinations of sample geometry and weldline placement produce different strain paths. Strains measured at sample failure then define the forming limits for that particular strain path. This formability data is then assembled to construct a forming limit diagram (FLD).
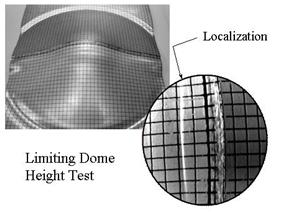
Localization (necking) in a stretch formed TWB
Finite Element Modeling
Finite element modeling of the TWB forming process makes it possible to predict the formability of a part without first building a prototype as shown below. Modeling the strain distribution in the part, especially in the material adjacent to the weld line is critical. Finite element modeling of a part can speed up the development of TWB in industrial applications.
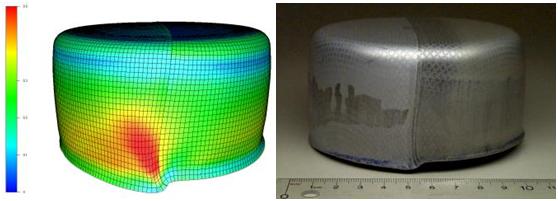
FE model (showing major strain contours) and experimentally drawn cup
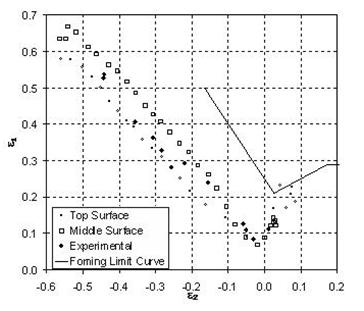
Forming Limit Diagram: Strain Comparison
Application
With formability knowledge of TWB’s and accurate finite element models, more aggressive weld line placements can be pursued. This leads to more flexibility for designers and better optimization of parts.
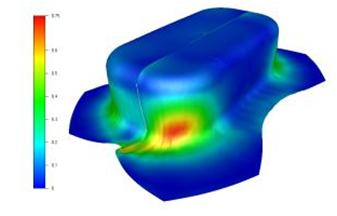
Medium Scale TWB Formability
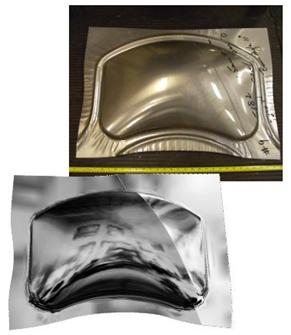
Large Scale TWB Formability