Introduction
Magnesium sheet metal alloys are prime candidates for use in the automotive industry because of their good strength- and stiffness-to-weight ratios. Limitations to their widespread use include low room temperature formability (and poor corrosion resistance). It is widely known that warm forming of these alloys can greatly improve their formability and this is a focus of the warm forming research at the University of Waterloo. A large component of this work is on the development of finite element constitutive models that are able to capture the complex anisotropy and tension-compression asymmetry behaviour of these metals at elevated temperatures and strain rates.
Strength-to-Weight Comparison
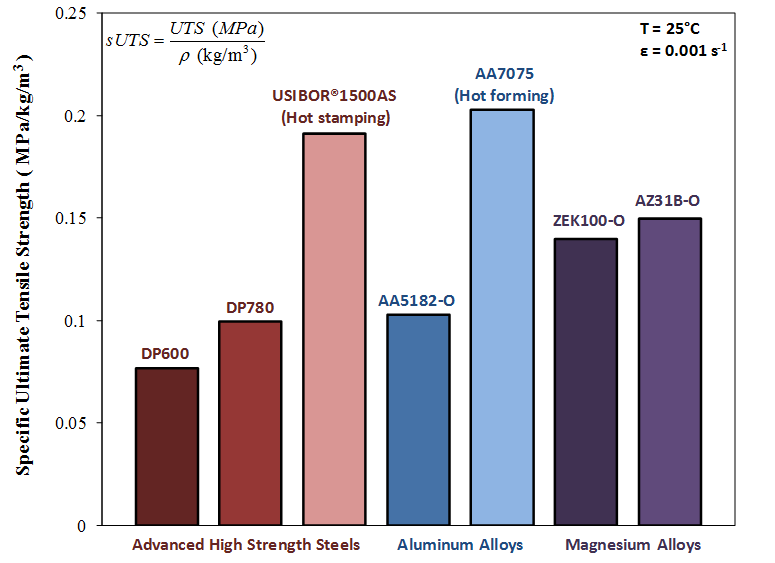
Characterization of Magnesium Alloy Sheet
Constitutive characterization and warm forming experiments were conducted on AZ31B and ZEK100 sheet to study the material formability, drawability, and constitutive response at elevated temperatures and a range of strain rates. Nakazima-type formability specimens were tested with a 100 mm diameter spherical tool with heater cartridges (PID controlled) embedded within the tooling for isothermal and non-isothermal conditions.
Constitutive Characterization: Room Temperature, 0.001 s-1
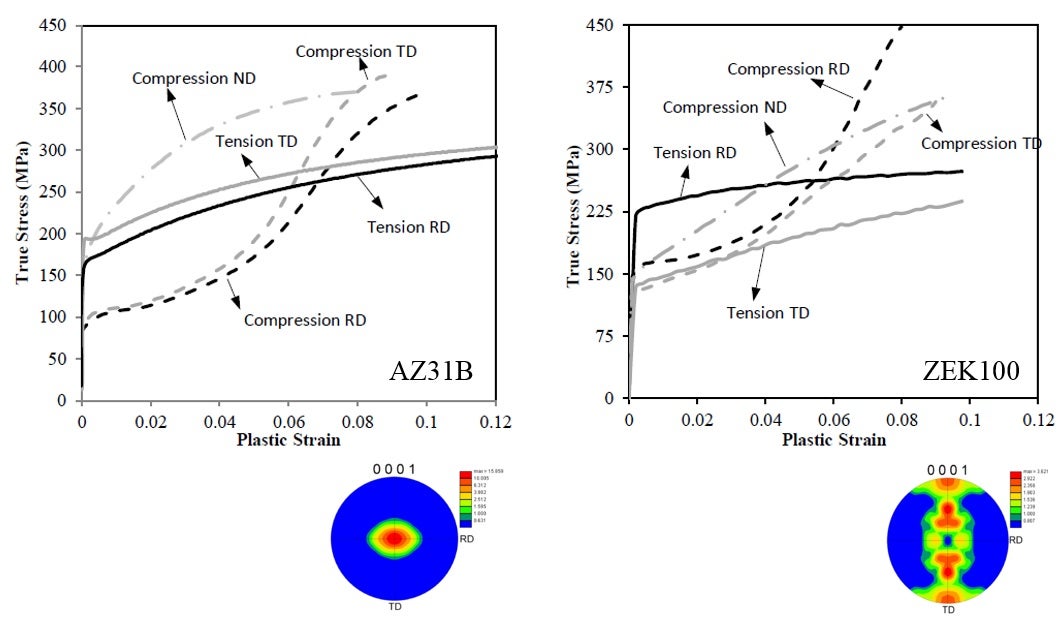
Left: S. Kurukuri, M.J. Worswick, D. Ghaffari Tari, R. Mishra, J. Carter, Proc. Royal Soc., Phil. Trans. A, 2014. Right: S. Kurukuri, M.J. Worswick, A. Bardelcik, R. Mishra, J. Carter, Met. Trans. A, 2014.
Elevated Temperature Constitutive Characterization (Tensile)
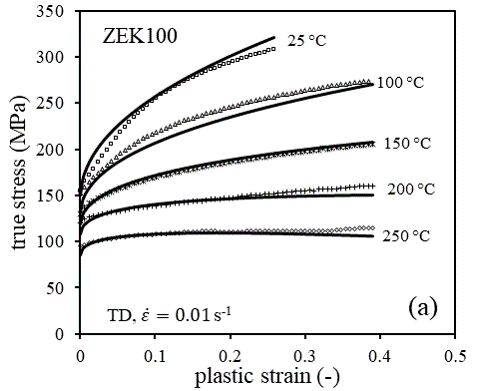
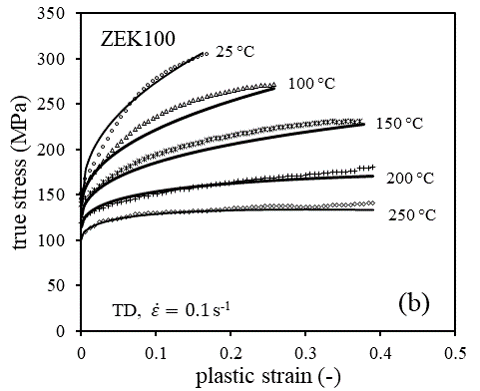
Elevated temperature yield function: ZEK100
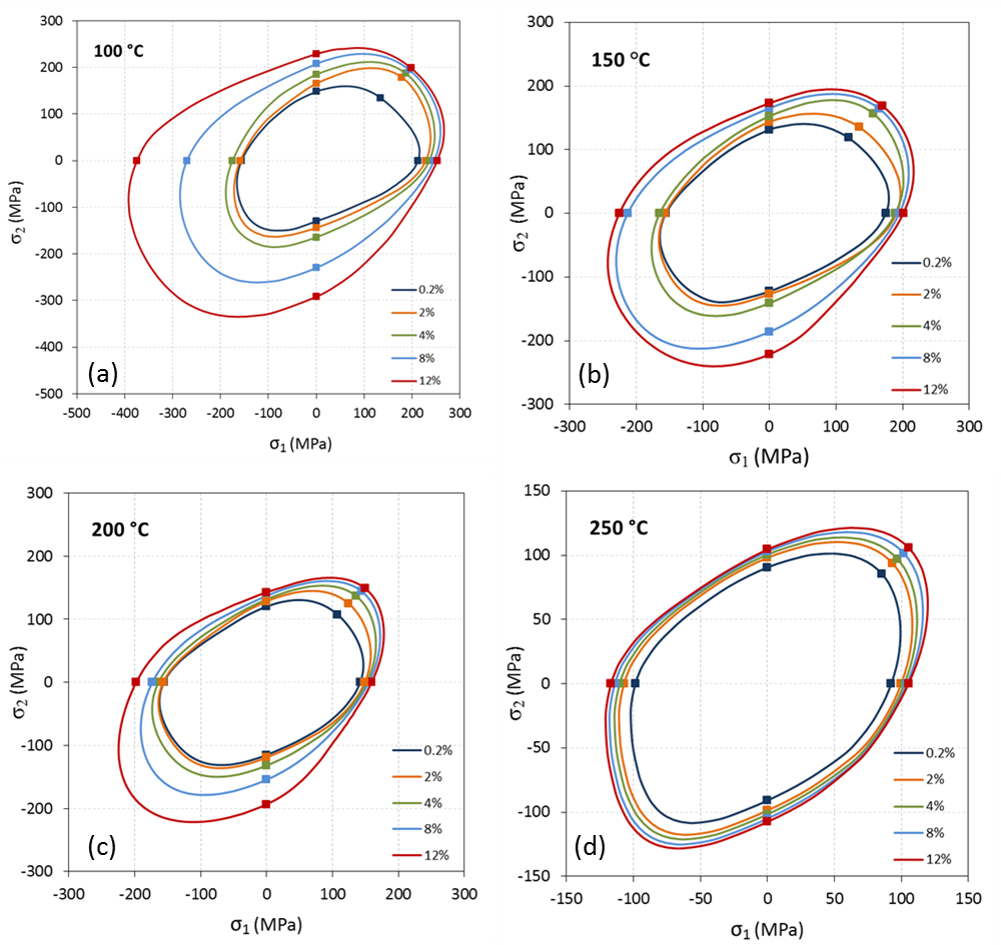
Determination of Warm Forming Limit Curves
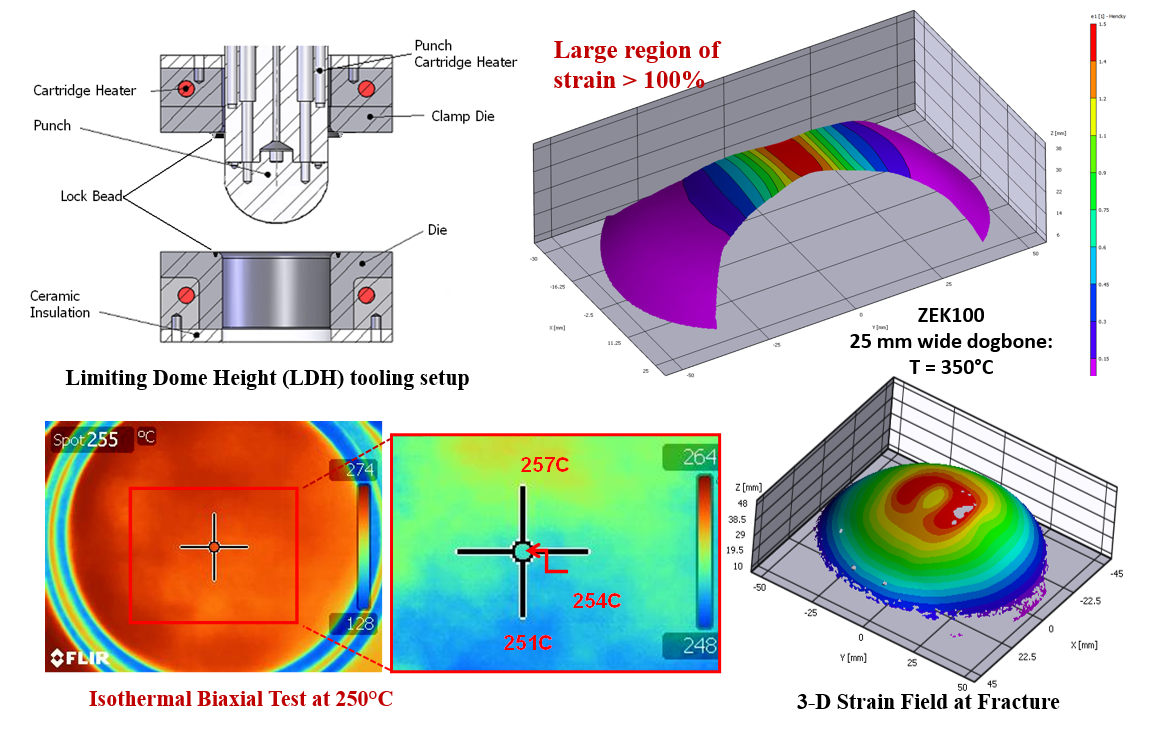
FLC: ZEK100 vs. AZ31B
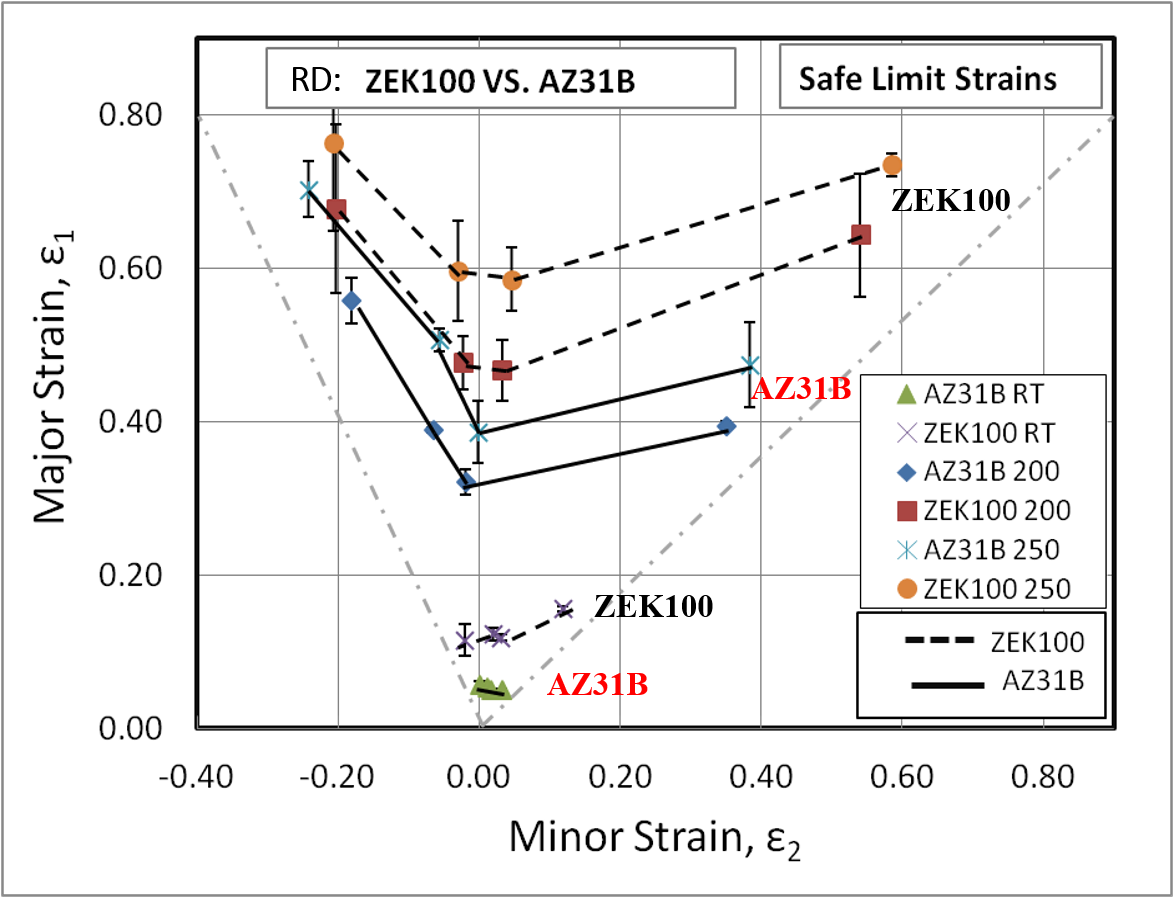
Formability Comparison – Plane Strain Limit
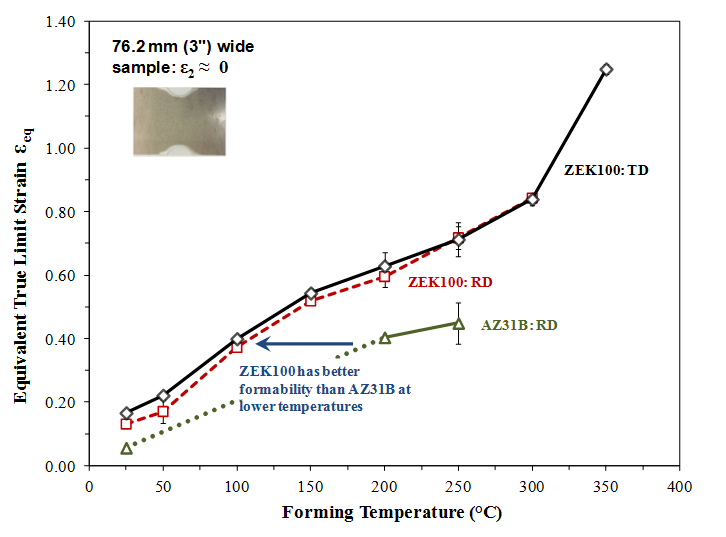
Application: Warm forming of a ZEK100 roof panel
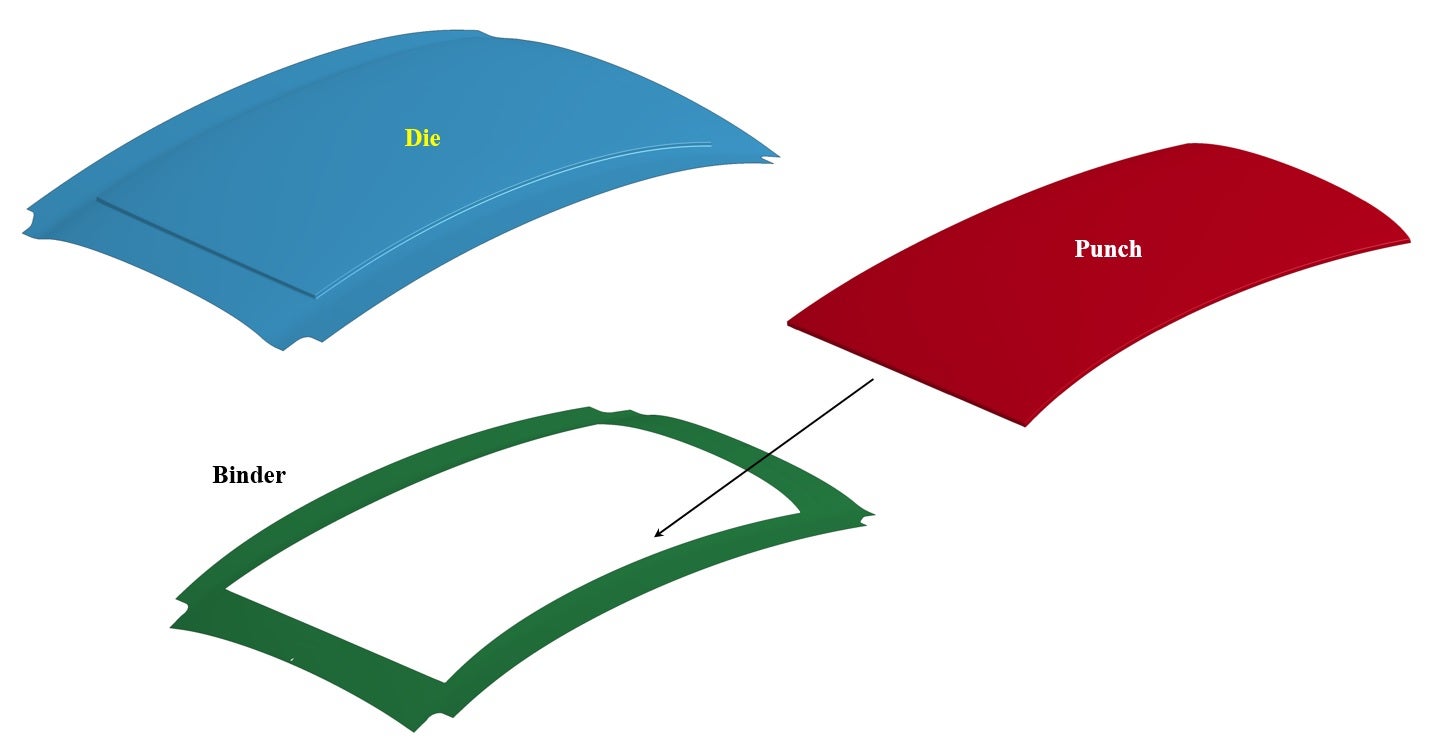
Modelling Procedure
For reference; Blue = Die, Yellow = Blank, Green = Binder, Red = Punch.
1. Blank Transfer & Placement on the Binder (Thermal): T = 270°C

2. Gravity loading: T = 252°C

3. Binder wrap and die close: T = 242°C

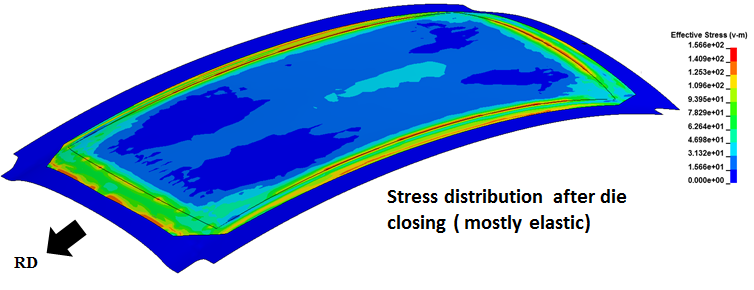
4. Non-isothermal Forming: Die moves downward, stretching blank over the punch: T = 235°C
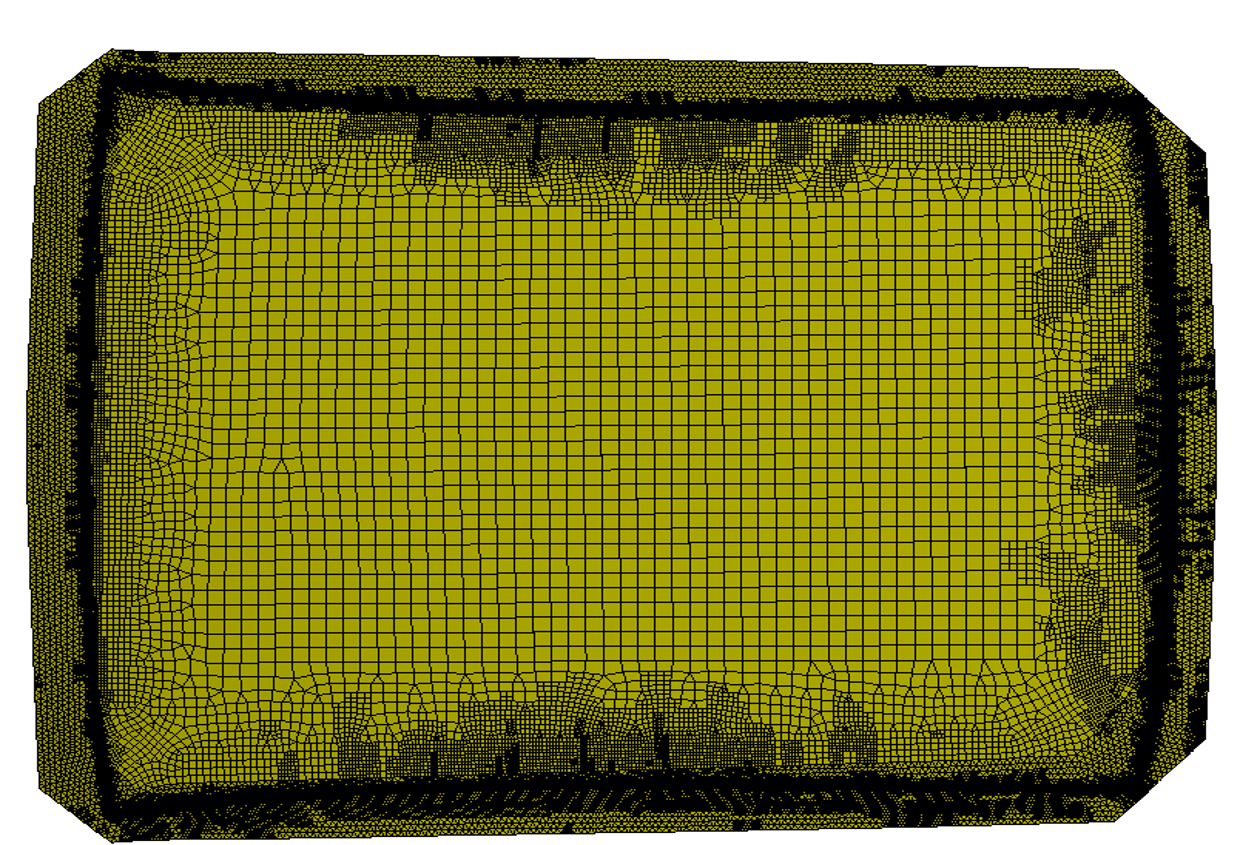
Forming Limit Analysis: Exp. Binder Force: 350 kN
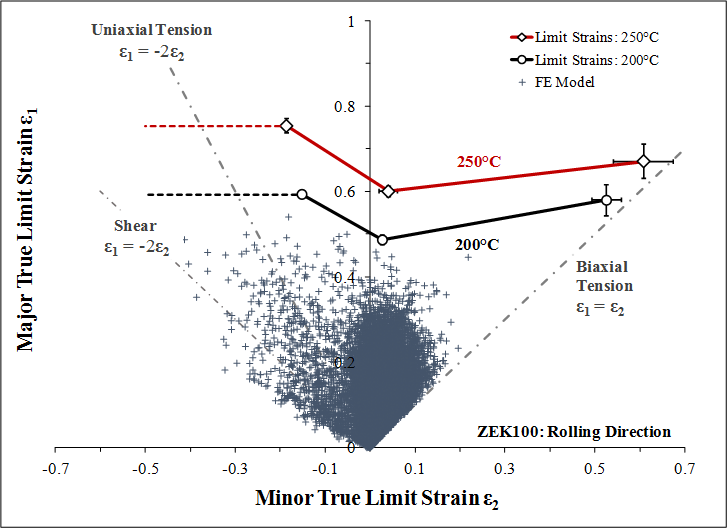
Formed ZEK100 Roof Panel
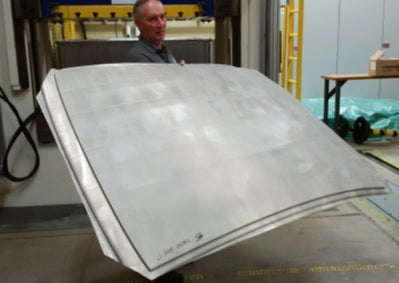
Forming done at Promatek Research Centre.
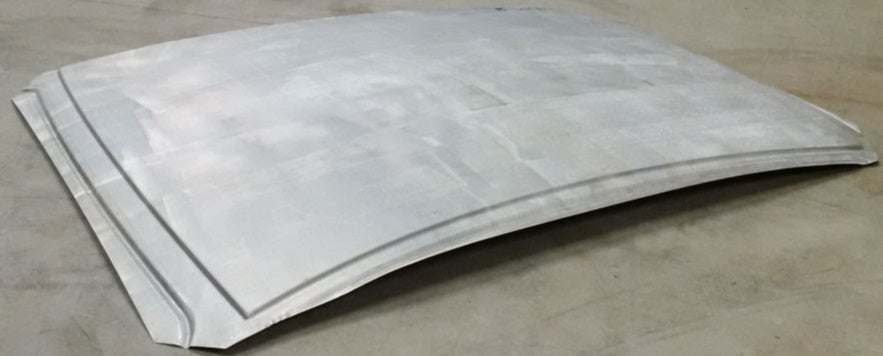