Introduction
Aluminum sheet metal alloys are prime candidates for use in the automotive industry because of their good strength and stiffness-to-weight ratios. The drawback to their widespread use is their room temperature formability. Aluminum alloys possess only moderate formability at room temperature. Hot forming of these alloys greatly improves their formability and this is the main focus of the research at the University of Waterloo. A large component of this work is on the development of finite element constitutive models that are able to capture the anisotropic behaviour of these metals at elevated temperatures and strain rates.
Description of Process
Hot forming of aluminum alloys consists of four main steps: solutionizing, transfer, quenching + forming, artificial aging. In the solutionizing step, the blank is heated in a furnace to a temperature where the precipitates in the material dissolve. This temperature is usually 470°C for 7000 series alloys and 530°C for 6000 series alloys. The transfer stage occurs when the blank is moved from the furnace into the press, and loses some heat in the process. The forming + quenching stage is the stamping operation in which the blank also cools. The artificial aging process is the post-forming heat treatment applied onto the formed part to obtain the desired strength properties.
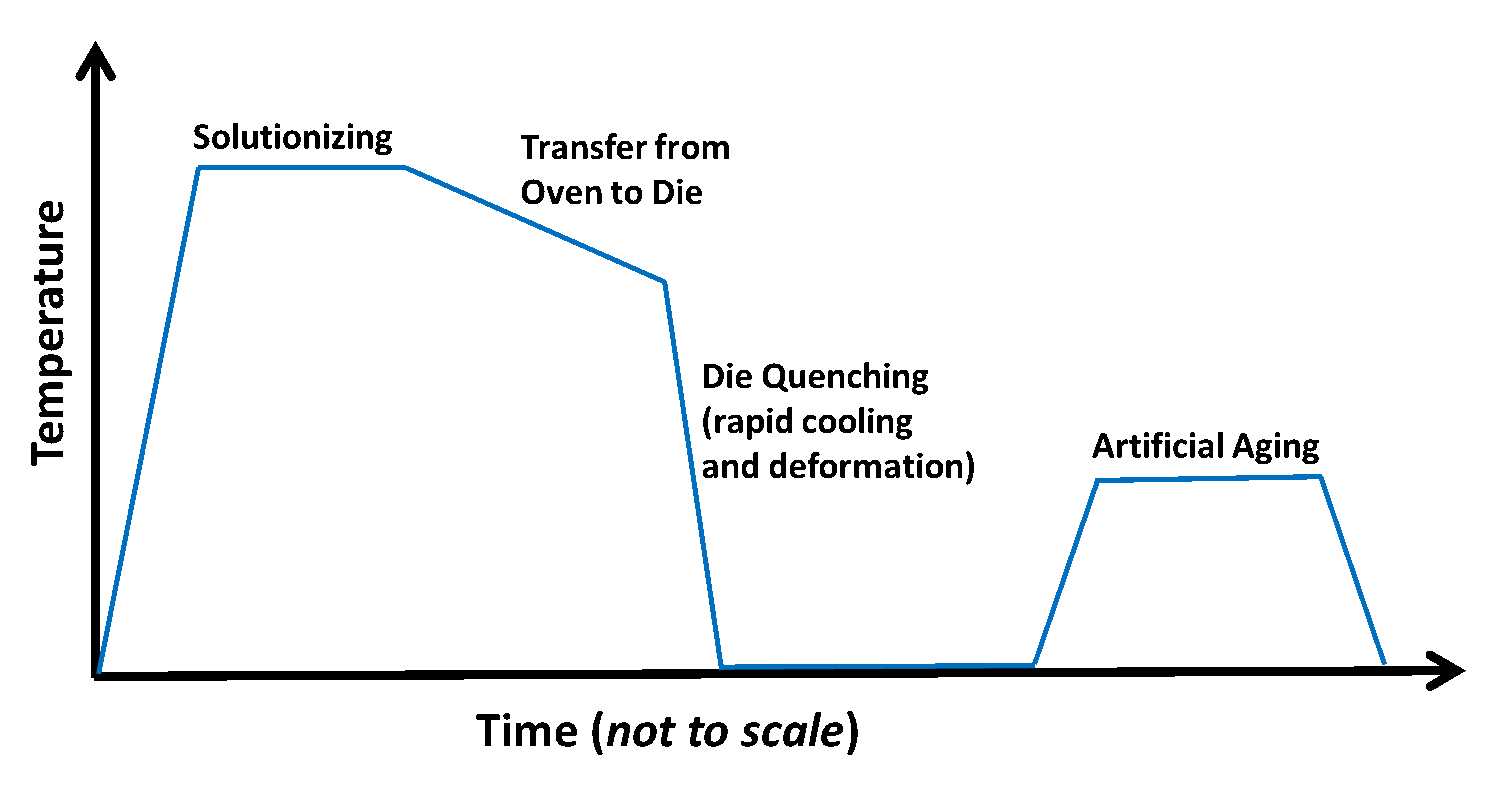
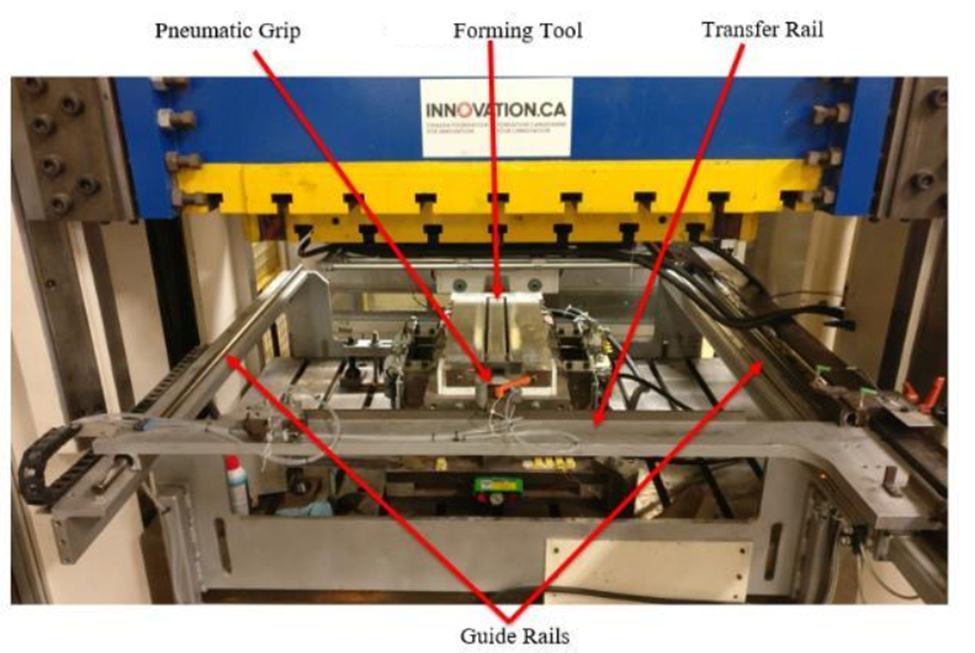
Constitutive Modelling
Experiments were conducted on a servo-hydraulic tensile machine on 2.0 mm thick aluminum sheets were conducted. To imitate the temperature-time cycle in a hot forming operation, a series of quenching nozzles were added inside the heating element to quench the tensile specimen (after solutionizing) to a steady state temperature. A schematic of the testing apparatus at the University of Waterloo is shown below.
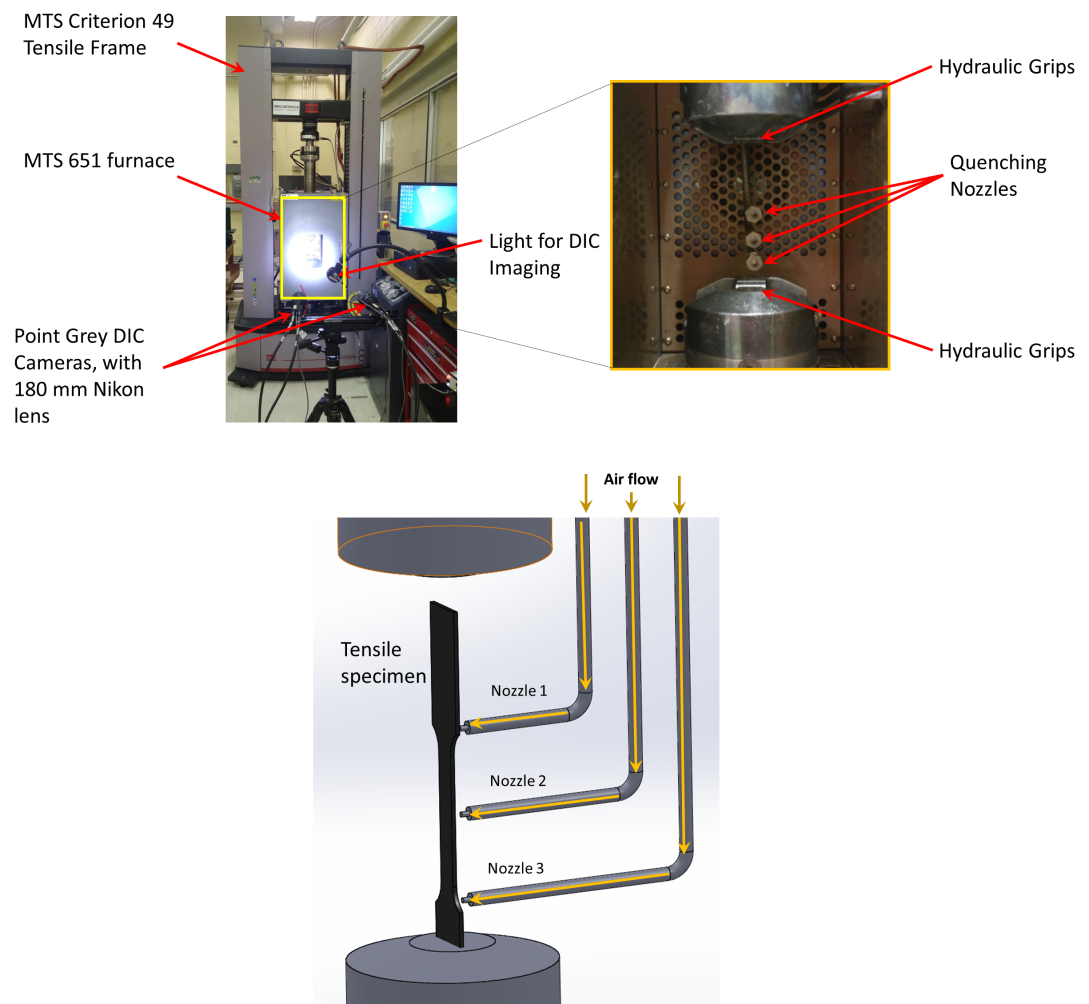
Setup of the tensile tests conducted to characterize the hot forming behaviour of 7000 series alloys (Omer et al., 2017)
Digital image correlation was used on all tensile specimens, from which localized strain and displacement data was extracted. An image of a tensile sample subject to DIC, and its resulting cross-section area in the necking region is shown below. The cross-sectional area was used to calculate the true stress-strain curve for AA7075, which is shown in the second image below. These curves can be used in a constitutive model to simulate the hot forming process of AA7075.
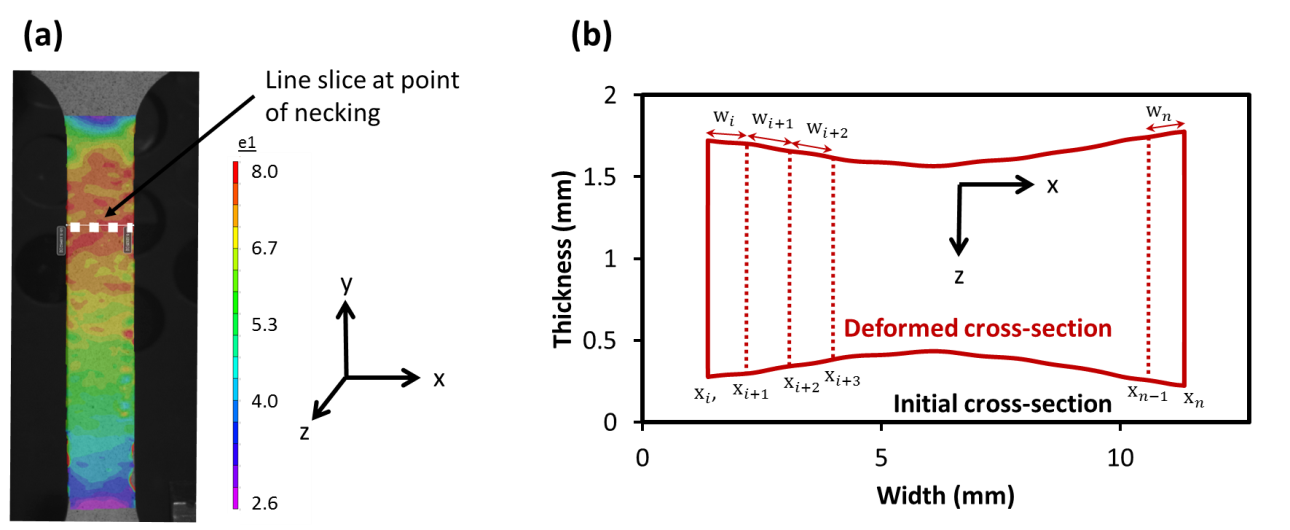
A. A tensile sample tested at 470°C with DIC and B. representation of the necking profile determined through the area reduction method (Omer et al., 2017)
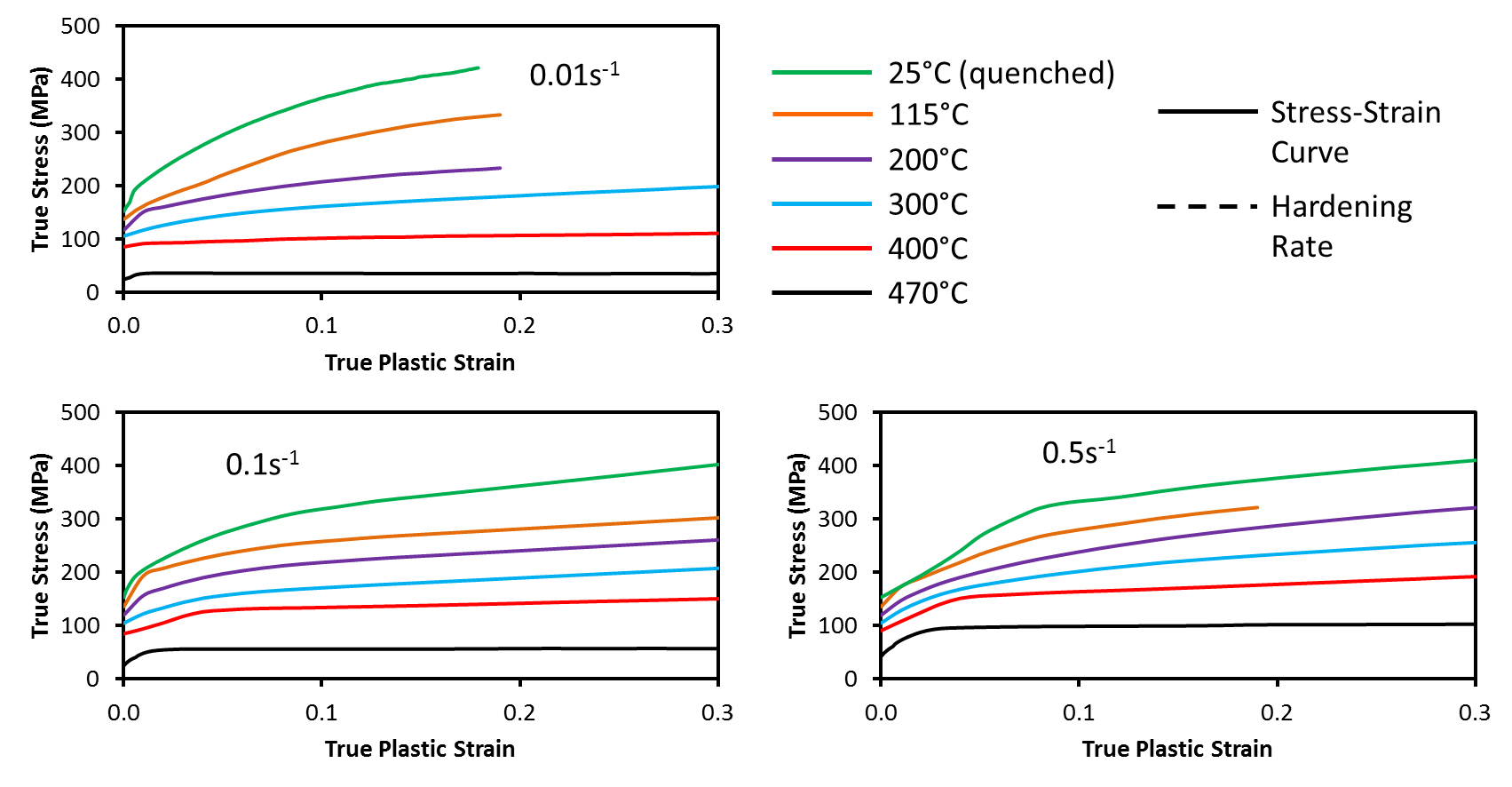
Stress-strain curves as a function of temperature and strain rate for the hot forming of AA7075
Hot Forming of Aluminum
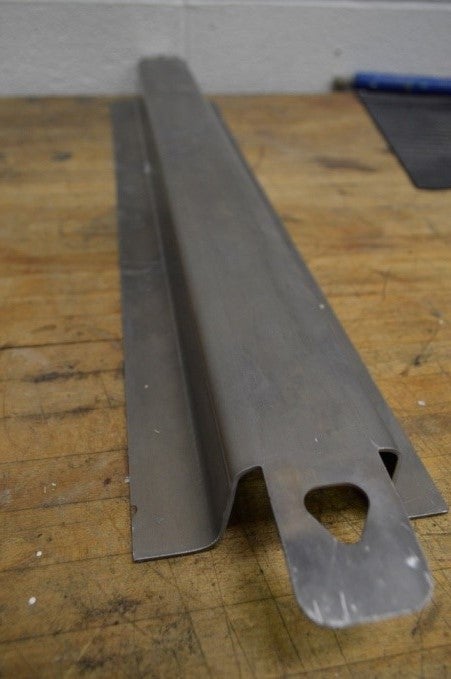
Formed rail lubricated with a PTFE spray (Kim, 2017)
Artificial Aging Treatments
The standard T6 aging treatment was applied onto some formed rails. Others were subject to interrupted T6 treatments, followed by a heat treatment resembling the paint bake cycle that is often applied to automotive assemblies. A total of four aging treatments were applied. The plot below shows the stress-strain properties of the four treatments applied. As shown, the stress-strain properties of material subjected to one particular interrupted aging treatment (8h at 121°C + paint bake cycle) matched the properties of a T6-treated material well.
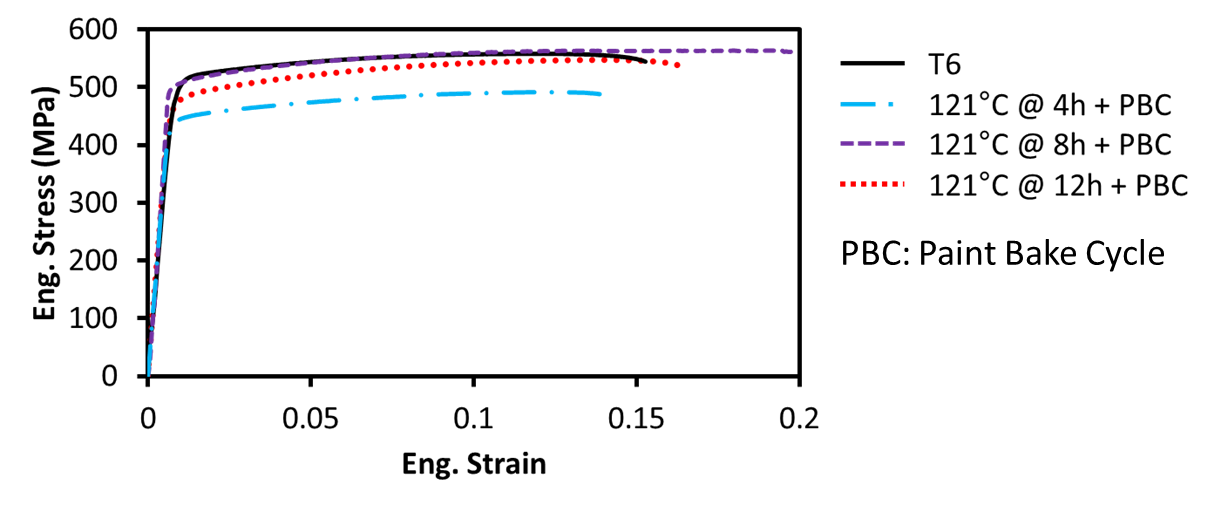
Stress-strain properties of various aging treatment applied to formed 7000 series rails.
References
Kim, S., 2017. Dynamic and Quasi-Static Response of Warm and Hot Formed Aluminum Beams Under Three-Point Bending. University of Waterloo.
Omer, K., Kim, S., Butcher, C., Worswick, M., 2017. Characterizing the Constitutive Properties of AA7075 for Hot Forming. Proc. Int. Deep Draw Res. Gr. Conf.