Introduction
The development of lightweight structural materials for automotive applications continuously attracts significant research interest due to governmental regulations and the demand for enhanced fuel economy. However, as alloy design strategies become more complex, so do the material models used to evaluate material performance. Fracture characterization is essential for the design of lightweight structural materials. Ductile fracture commonly occurs by the nucleation, growth, and coalescence of microscopic voids.
Common approaches adopted today to predict ductile fracture include micromechanical models (e.g. Gurson-type models) or phenomenological continuum damage models. Phenomenological models are often employed in industry due to their lower computational cost. One of the more commonly adopted models is the Generalized Incremental Stress-State dependent Model (GISSMO) which was recently developed by Daimler to predict ductile fracture within the finite element code LS-DYNA. Its primary motivation is to improve numerical simulations which involve strain path dependent processes. Damage is accumulated in an incremental manner using a generalization of the Johnson-Cook model. Once the damage parameter reaches a critical value, damage is introduced and element deletion occurs. The main input into the GISSMO model is tabulated data of the failure strain as a function of stress triaxiality which is obtained experimentally.
Experimental Approach
In order to develop fracture loci an extensive experimental program is required. The equipment used for quasi-static fracture characterization in the metal forming lab at the University of Waterloo are as follows: MTS Criterion Model 45 servo-electric tensile frame for tensile based geometries, MTS dome testing system for hole expansion and Nakazima dome tests, Tinius Olsen deep draw apparatus for mini dome experiments and an in-house developed v-bend system for plane strain fracture characterization. Strain measurements are obtained from the digital image correlation (DIC) method and this system is compatible with all of the instruments described above. Comprehensive experimental programs have been developed to determine the fracture loci of different advanced sheet materials including aluminum, steel, and magnesium alloys. Different sample geometries were investigated which cover a wide range of stress states as shown below.
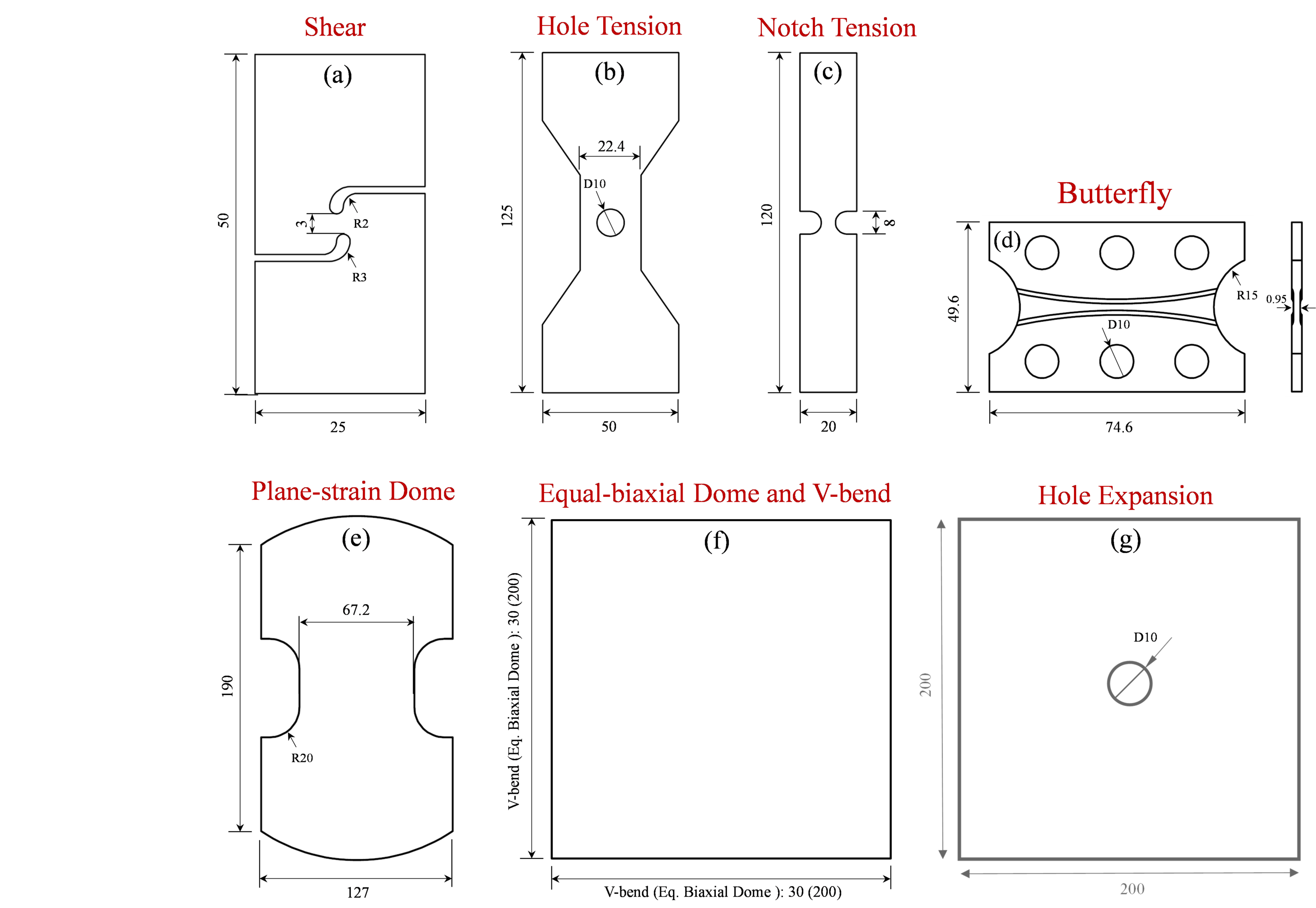
Sample geometries used for fracture characterization
For instance, for a 6000 series aluminum extrusion, the samples shown below were all pulled at a nominal strain rate of 0.001s-1 on the MTS frame. The von Mises equivalent strain at failure was extracted from the image before the first crack was observed on the sample surface. Furthermore, the stress triaxiality was determined from finite element simulations.
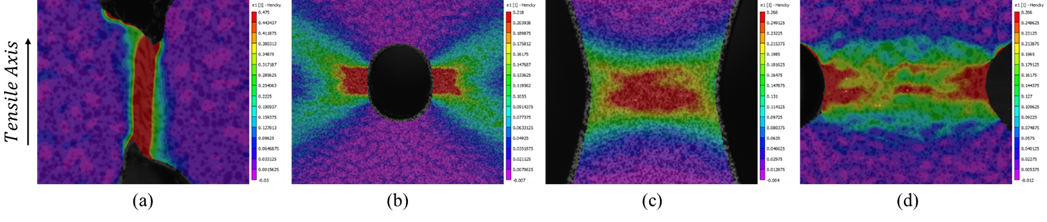
Strain contours of the maximum principle strain one image before a crack was observed (a) mini-shear, (b) hole tension, (c) smooth notch and (d) plane strain notch.
Fracture Loci Calibration
The phenomenological fracture loci such as the Modified Mohr-Coulomb (MMC) model can be used to investigate the fracture surface of materials. Combination of the failure strains obtained experimentally and the numerical stress triaxiality values yields several critical points which can be used to calibrate the fracture model as shown below. The model can be calibrated using a hybrid experimental-numerical approach. If the material exhibits anisotropic behaviour, failure curves can be generated for different orientation with respect to the rolling or extrusion directions of materials.
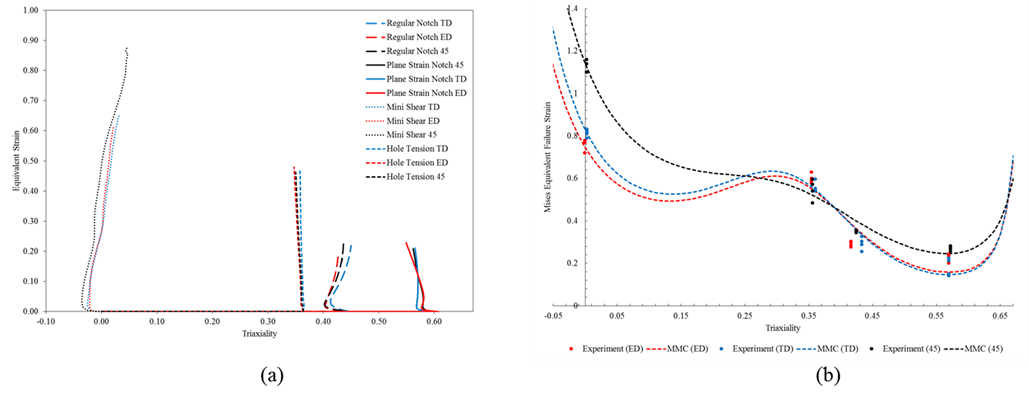
Equivalent strain vs. stress triaxiality for each loading case and (b) the MMC model fit to the hybrid experiment-simulation data.
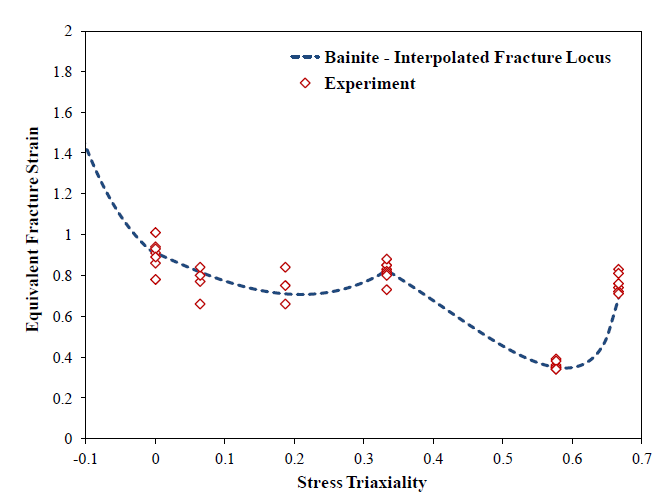
Fracture locus of a bainitic steel.
Fracture under Non-proportional Conditions
It is essential to characterize the response of materials under non-proportional loading conditions since in metal forming operations and in crash events materials undergo severe stress state changes. The constitutive and fracture behaviour of materials under non-proportional conditions are different than proportional cases which leads to specific features such as kinematic hardening and non-unique forming limit diagrams (FLD). The figures below show specimens extracted from pre-strained uniaxial and biaxial specimens to impose significant changes in the strain paths for the second stage of deformation to investigate the role of non-proportional loadings on fracture.
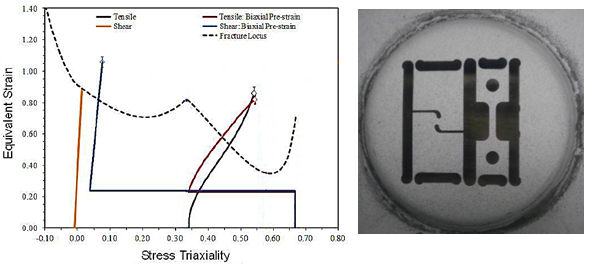
Non-proportional response of materials can be studied under severe changes of strain paths. Such as shown above for a Usibor steel sheet.
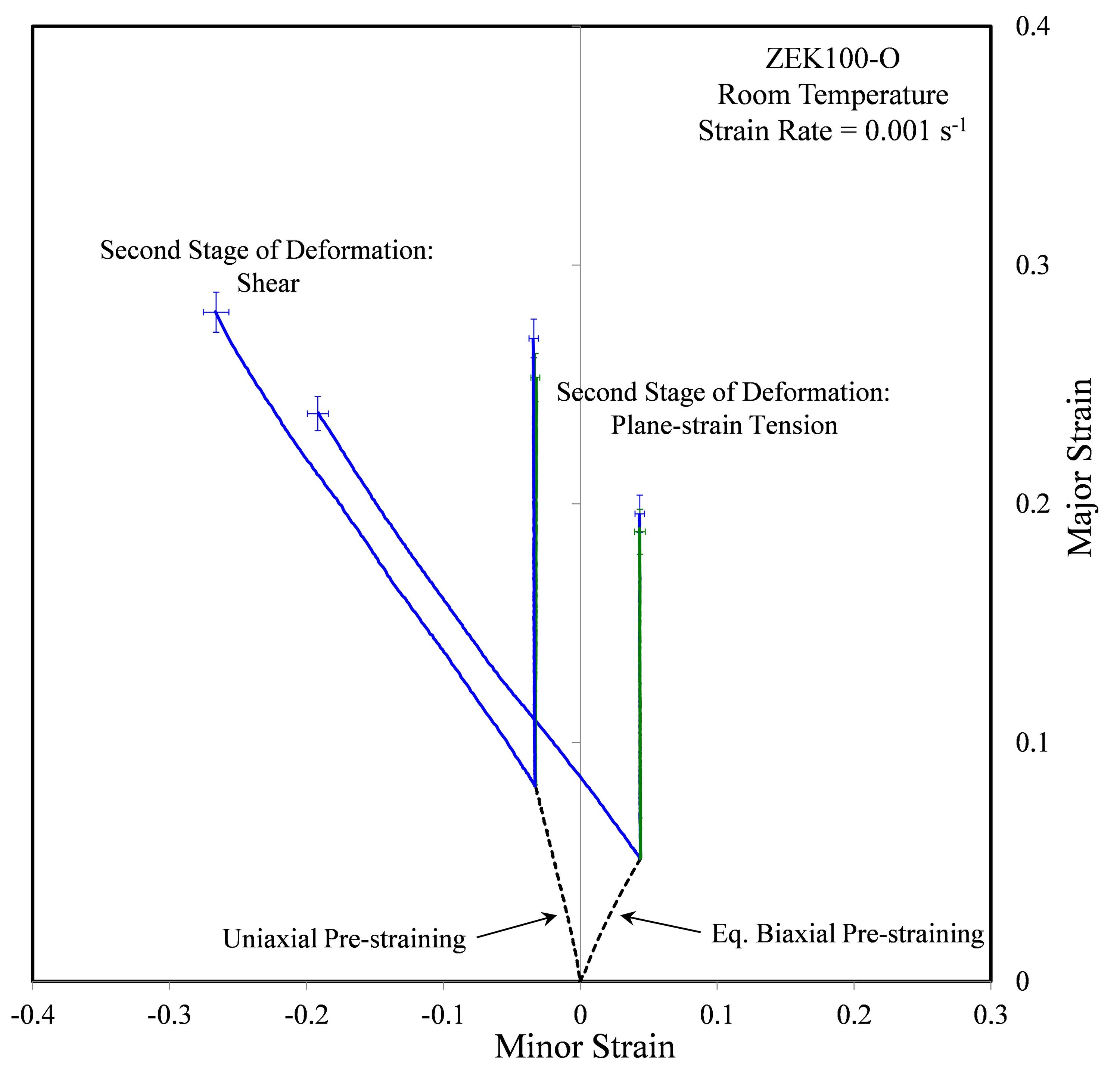
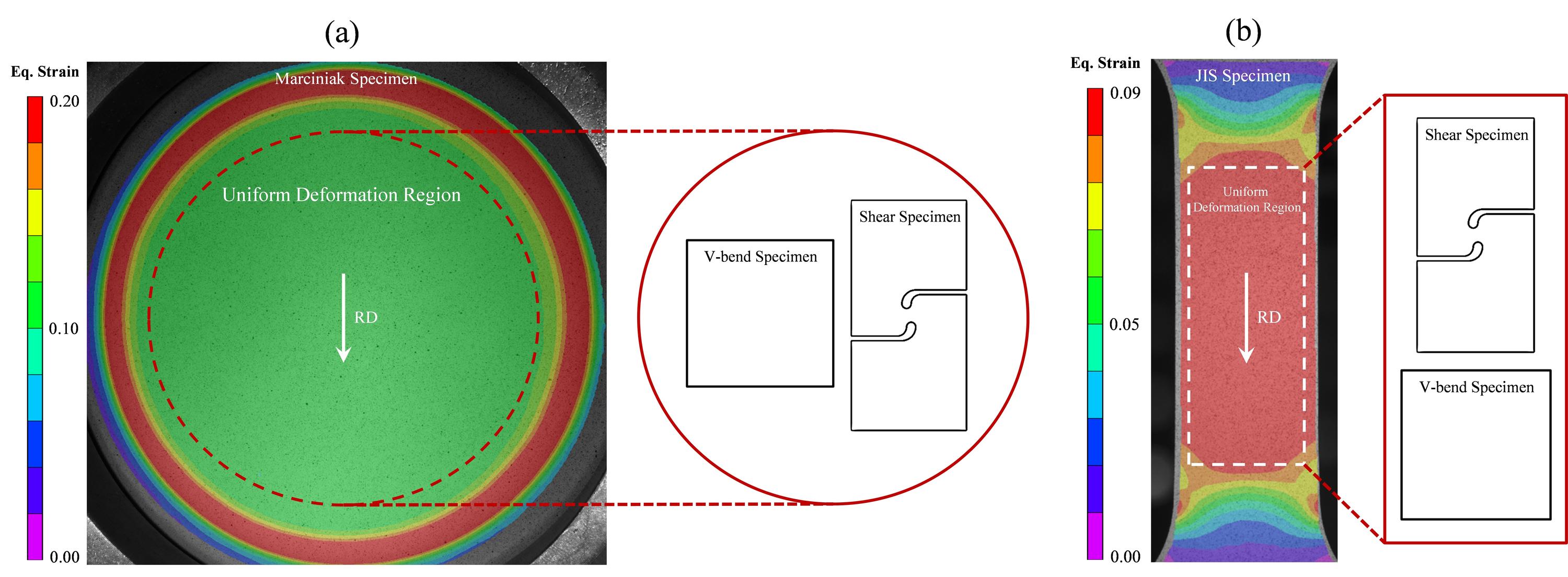
Non-proportional response of materials can be studied under severe changes of strain paths. Such as shown above for a magnesium alloy sheet.