Introduction
Currently, the need to improve automobile efficiency through weight reduction is apparent and one method to achieve this is by manufacturing conventional automobile structural components with new and lightweight sheet metals. However, in order to accurately model a vehicle crash event using finite element methods, the mechanical properties at elevated strain rates are required. This research consists of determining the constitutive behaviour of these new and lightweight metals at high rates of deformation. For each material, the compiled data consists of flow stress as a function of strain, strain rate, and temperature. Of equal importance is the fracture behaviour and damage development under high rates of deformation.
In order to evaluate the response of a materials over the range of strain rates operative during crash, tension (or compression) tests are conducted at strain rates that range from:
- Quasi-Static Strain Rate: 0.001-1.0s-¹ tested using an MTS Criterion Model 45 Tensile Frame
- Intermediate Strain Rate: 1.0-100s-¹ using the Hydraulic Intermediate Strain Rate (HISR) apparatus
- High Strain Rate: 500-1500s-¹ tested using a Tensile Split Hopkinson Bar Apparatus (Compressive Split Hopkinson Bar Apparatus is also available)
The range of alloys that have been tested at the University of Waterloo include:
- Dual Phase Steel (DP600, DP800, DP980, DP1180 flat and tube stock)
- Transformation Induced Plasticity Steels (TRIP780, flat and tube stock)
- High Strength Low Alloy Steel (HSLA350, flat and tube stock)
- Drawing Quality Steel (DDQ, DQAK, flat and tube stock)
- Hot Stamped Boron Steel (various microstructures of USIBOR®1500 and DUCTIBOR®500)
- Magnesium (AZ31B sheet and cast AM60, at various tempers)
- Aluminum (AA5182-0, AA5754, AA6063-T6 extrusions, AA6013, AA6111, AA7075, flat and tube stock)
- Various other AHSS and aluminum alloys
- Polymeric (various types including fibre reinforced polymer matrix)
Quasi-Static Strain Rate – MTS Criterion Model 45 Tensile Frame
The quasi-static experiments conducted at the University of Waterloo are carried out using the MTS Criterion Model 45 Tensile Frame. There are currently two load cells which can be used interchangeably with the system having capacities of 30kN and 100kN. Specimen displacement may be measured with extensometers manufactured by MTS. However, the digital image correlation method is typically used for measurements of displacement and strain. The specimens were mounted in a pair of custom grips as shown below with the extensometer. The grips are positioned as to align the specimen concentrically with respect to the loading axis of the machine, which reduces the likelihood that bending loads will be applied to the specimen. An environmental chamber allows elevated temperature testing up to 500 °C with in situ digital image correlation (DIC) based strain measurement.
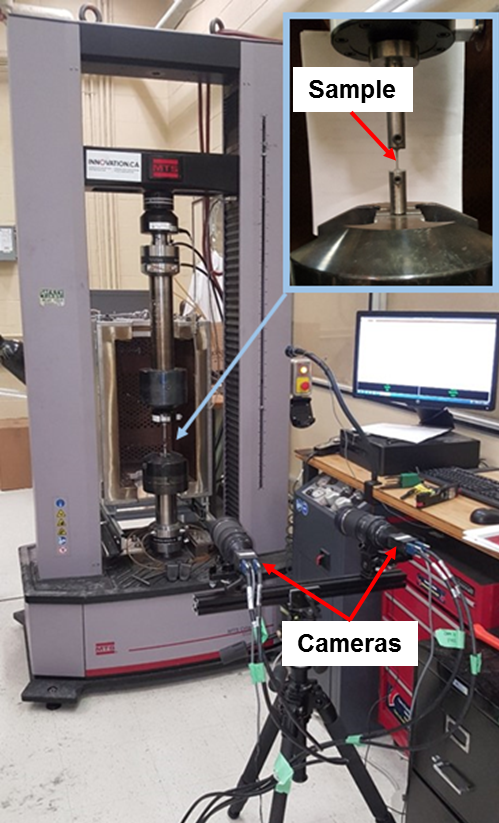
MTS Criterion Model 45 Tensile Frame Setup for miniature dogbone tensile specimens
Intermediate Strain Rate - Hydraulic Intermediate Strain Rate (HISR) Apparatus
The hydraulic intermediate strain rate (HISR) apparatus was developed at the University of Waterloo. The apparatus has a 13.3kN (3,000lbf) hydraulic actuator with 101.6mm (4”) stroke. The apparatus functions by accelerating the engagement sleeve to a constant velocity which then contacts the engagement piston at the bottom of the stroke as shown in the schematic below. A MOOG high performance servo-valve with a 15GPM capacity is used to achieve a maximum stroke rate of 1500mm/s. A KISTLER 9500A4 ±30kN piezoelectric load cell, which is located directly above the upper grip assembly, measures the load during the test while the enhanced laser displacement system (ELDS) may be used to measure the displacement. However, the digital image correlation method is generally used for measurements of displacement and strain. Load and displacement are acquired within the HISR system using a National Instruments 6212 USB data acquisition module at a maximum sampling rate of 250,000 samples per second.
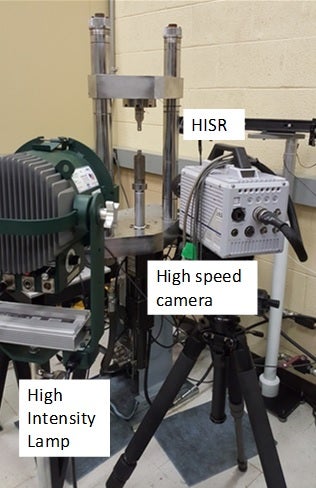
HISR apparatus at the University of Waterloo with a schematic showing the ELDS system
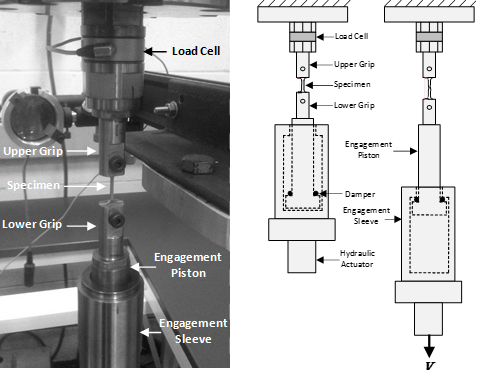
High Strain Rate - Tensile Split Hopkinson Bar Apparatus
The tensile split Hopkinson bar (TSHB) apparatus is used to conduct high strain rate tensile tests on sheet metal specimens (can be used to pull cylindrical specimens as well) and the TSHB apparatus at the University of Waterloo is shown in the figure below along with a schematic representation. In this test, a gas gun propels a hollow striker towards the end cap. The impact creates a tensile load on the incident bar which sends a tensile wave along the incident bar towards the specimen. When the tensile wave reaches the specimen, part of the wave is transmitted through the specimen and the remainder is reflected as a compressive wave as shown in the wave data below. Using the Kolsky equations, the stress, strain and strain rate can be calculated using the data. The TSHB at the University of Waterloo has momentum trapping capability, which traps propagating stress waves, thereby allowing interrupted tests to be conducted. Also, a radiative furnace is available to conduct elevated temperature tests that are used to characterize thermal softening.
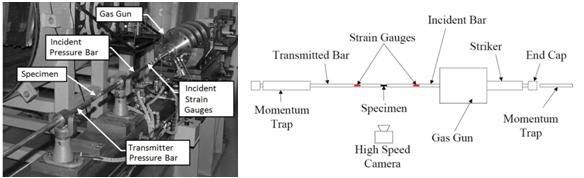
TSHB apparatus (and schematic) at the University of Waterloo
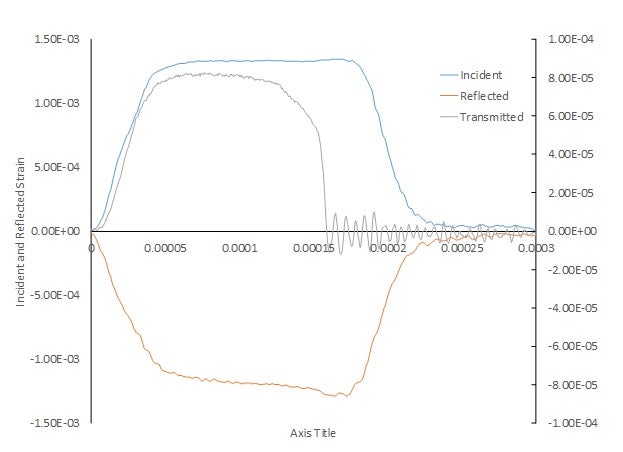
Typical waveform strain data
The THSB is capable of performing interrupted tests. These tests are used to stop the deformation of samples prior to final fracture, thus enabling the measurements of damage in the necked region.
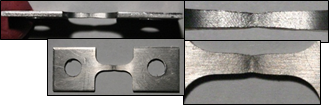
Sample from an interrupted TSHB test. Note the neck region, which would not have been able to be obtained using a standard TSHB test.
Digital Image Correlation (DIC) System for High Strain Rate Testing
In situ digital image correlation (DIC) technique are employed to measure the full-field strain distribution within the samples during the experiments ranging from low (10-3 s-1) to high (103 s-1) rates of strainr. Photron SA5 high speed cameras are used to capture the images with a maximum of 200, 000 fps for the experiments at strain rate of 1000 s-1. Funding has been recently secured to purchase ultra-high speed cameras (stereo) with framing rates of 10,000,000 fps. A new Telops high speed thermal camera is also available enabling thermal measurements at up to 90,000 fps. The preparation of the specimen surface and speckle pattern has significant effect on the quality of the image and DIC resulting data. A high quality speckle pattern allows the post-processing software to identify and calculate the displacements accurately. Therefore, it is important to get an adequate speckle pattern, as well as an initially flat and smooth specimen surface. A considerable quantity of black speckles arranged randomly with different shapes and sizes are required to achieve an adequate speckle pattern.
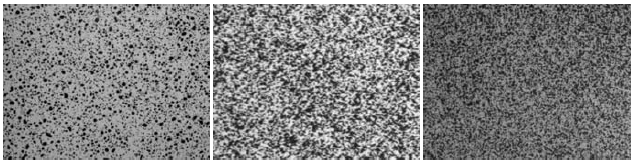
Typical speckle patterns
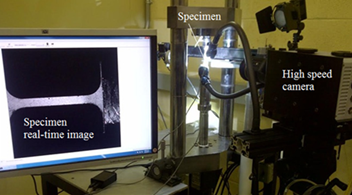
DIC testing setup on the HISR
Material Characterization
The typical material characterization procedure involves testing a sheet metal at various strain rates (with the equipment described above) as shown by the flow stress curves below. The experimental data is then used to calibrate a constitutive model (Zerilli-Armstrong, Johnson-Cook, modified Voce, etc.) using non-linear regression, as shown for room temperature tests and a modified Hockett-Sherby constitutive model. The constitutive model is then used as input for finite element models of vehicle crash.

Experimental and model predictions of the strain rate sensitivity associated with the AA6063-T6 extrusion (a) True stress vs. strain rate for various levels of plastic strain and (b) True stress vs. plastic strain for different strain rates.
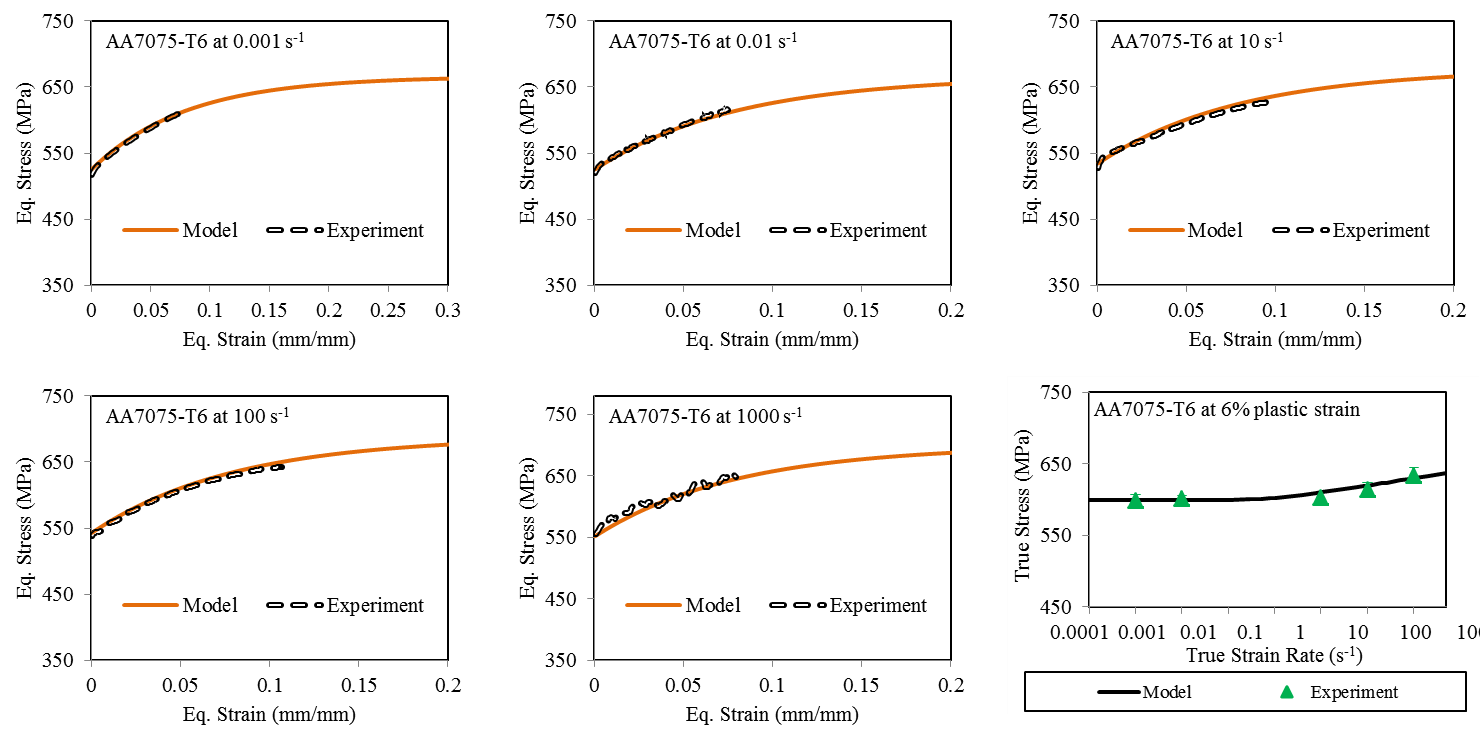
Experimental and model predictions of the strain rate sensitivity associated with the AA7075-T6 sheet metal alloy.
Unlike most of the steel alloys, some aluminum alloys, such as, AA5182-O exhibits a mild negative rate sensitivity over the strain rate range from 0.001–1 s-1, while at higher rates a mild positive strain rate sensitivity is observed. The Portevin–Le Châtelier (PLC) effect can be attributed for such negative rate sensitive response. Following video of high speed DIC full-field strain measurements shows the PLC band propagation during tensile testing.
The material hardening response at large strains and strain rates should be well characterized along with the material high rate fracture behaviour under stress states ranging from shear to equal biaxial tension. Traditionally, material characterization at elevated strain rates has been performed using uniaxial tensile tests to determine the hardening response along with the fracture behaviour. Such material hardening data is only valid until the onset of diffuse necking as defined by the Considere criterion when the hardening rate becomes equal to the true stress; beyond this point, diffuse necking ensues and the triaxiality increases such that the response is no longer uniaxial. A complementary test for material and fracture characterization at large strains and elevated strain rates is a simple shear test that unlike the tensile tests, does not develop a through-thickness necking instability at low strains and for which deformation remains planar as simple shear does not promote thickness strain (plane strain in nature). A micro-shear specimen geometry (shown below) can be used to perform shear tests at strain rates ranging from low (10-3 s-1) to high (103 s-1).
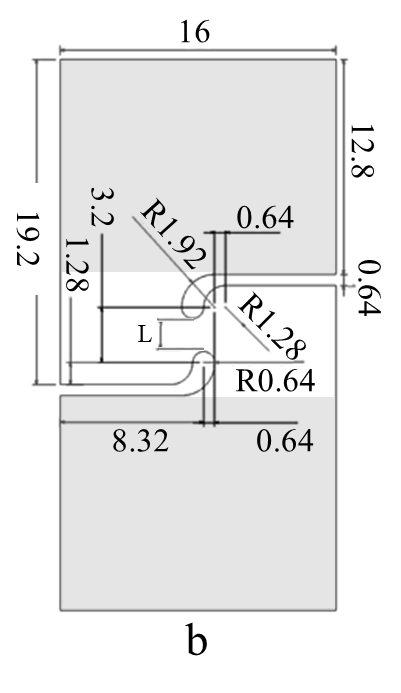
Micro-shear specimen geometry. Dimensions are in mm. Shaded regions correspond to the grip area.
The effect of strain rate on the shear stress-strain response for the DP600 and AA5182-O sheet materials is shown below. The drop in rate sensitivity with strain as strain rate is increased can be largely attributed to the increased temperature rise with strain rate as the deformation becomes more adiabatic.
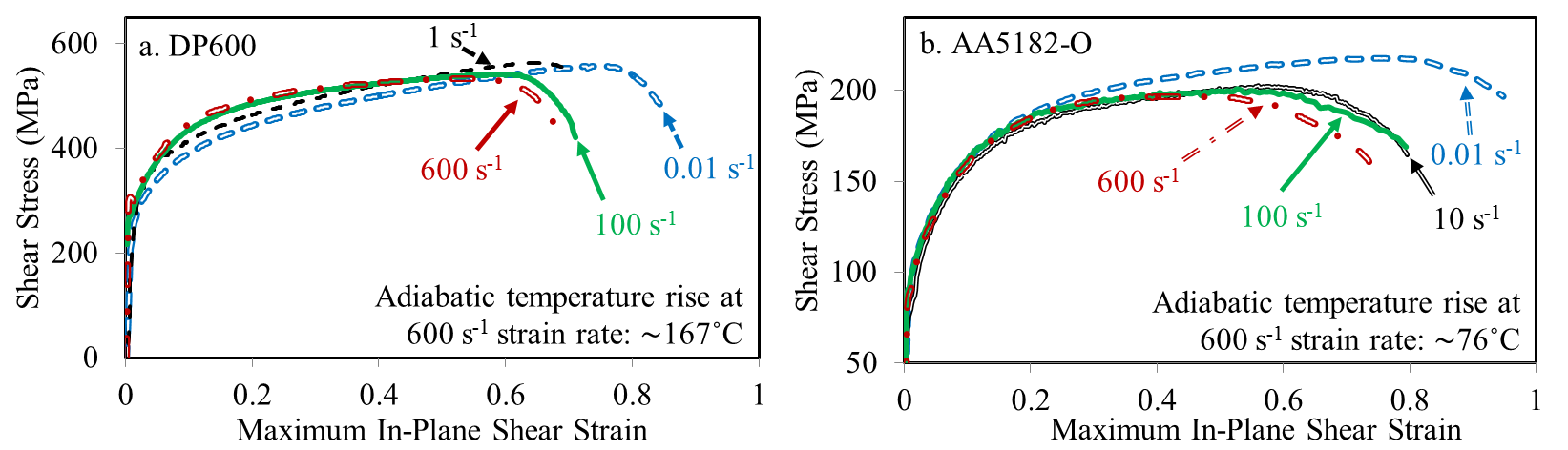
Strain rate effect on the stress-strain curves from shear experiments for (a) DP600 and (b) AA5182-O sheet specimens at strain rates ranging from 0.01 to 600s-1.
The effective stress-effective plastic strain can be converted from the shear experiments to uniaxial tensile data with very good agreement between the hardening response from the uniaxial tension and shear experiments (as shown below for DP600). The effective stress-effective plastic strain data derived from the shear experiments are attractive since they are direct measures of constitutive response at large strain and offer an alternative to inverse analysis approaches to extrapolate constitutive behaviour beyond necking in tensile tests.
![Effective stress-effective plastic strain response for DP600 derived from tensile [4] and shear experiments (using Eq. (24) and (25)) at (a) quasi-static (b) 1, (c) 100, and (d) 600 s-1 strain rates.](/waterloo-forming-crash-lab/sites/default/files/uploads/images/tabs3.png)
Effective stress-effective plastic strain response for DP600 derived from tensile [4] and shear experiments (using Eq. (24) and (25)) at (a) quasi-static (b) 1, (c) 100, and (d) 600 s-1 strain rates.
Finite Element Modeling
LS-DYNA is used to conduct finite element modeling of the high strain rate tensile tests. The various constitutive models determined from the experimental results will be applied within a user-defined material model or umat. Comparisons between experimental results and those predicted by the finite element model will be made to assess the constitutive models as shown below. Damage development will be predicted using a Gurson-based constitutive model.
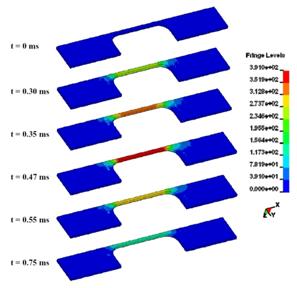
Finite Element Model of 1000s-¹ test showing contours of true stress