In automotive industries, sheet metal assemblies are usually fabricated by using several joining methods. At the University of Waterloo work is done to characterize resistance spot welding and adhesive bonding for crash safety applications. Resistance spot welding is used by industry due to its flexibility, low cost and very short cycle time. Despite the extensive application of resistance spot welding in automotive industries, there are many processing and material parameters that influence the final mechanical properties of the welds. In resistance spot welding, a passing current (~6-10 kA) heats up the contact point between two sheets in a fraction of second (~200 – 500 ms) through resistance under a clamping force (~2-6 kN). This joining process results in the temperature distribution shown in the contour plot below with the corresponding microstructure shown to the left. In addition to these important parameters, the spot weld quality depends on the material parameters such as thickness, hardness, coating, and chemical composition and also the electrode geometry and material.
At the Waterloo Forming and Crash Lab, we focus on characterizing the mechanical response of these joining methods using several experiments that show the deformation and fracture response of the joints to various loading conditions. Ultimately, the goal is to use the data to construct/calibrate spot weld models that can be used in automotive crash models. The current weld material model used by our group is an elastic-linear plastic with a three-parameter failure function that softens after damage initiation. This function requires experimental normal stress, bending stress, and shear stress, at weld failure to be properly defined. Each of these stress states are shown below with calibrated models for tailored hot stampings shown below. The normal stress at failure is determined using the cross tensile test, the bending stress at failure is determined by the coach peel test, and the shear stress at failure is determined by the lap shear test. Each of these tests are designed to isolate the weld load state as best as possible. The design of the weld coupons to be used in these tests are from the American Welding Society (AWS) standards.
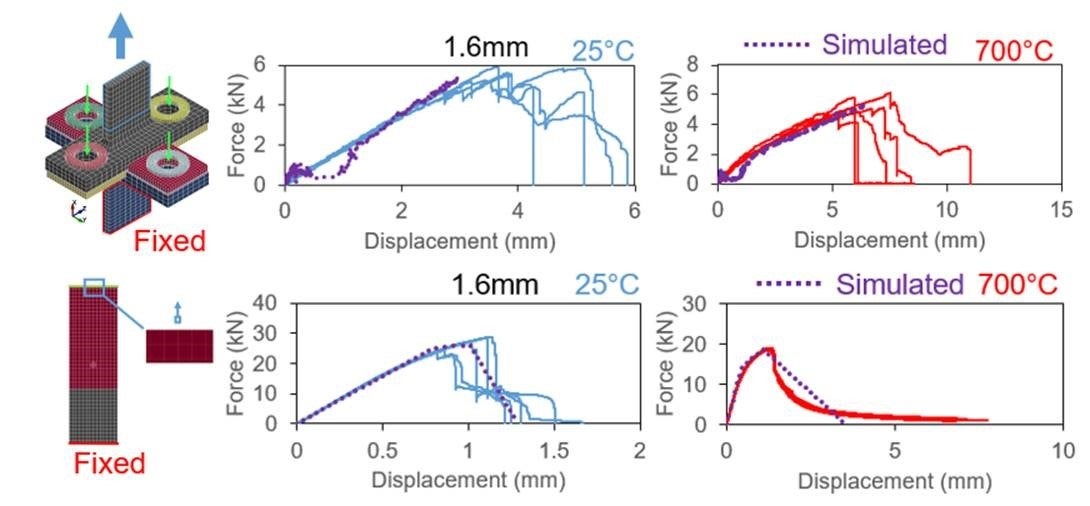
Figure 1: Cross tension (top) and lap shear (bottom) experimental and calibrated CAE force displacement data
The Forming and Crash Lab also has the capacity to investigate the mechanical behaviour of these joining methods in structural settings. Currently work investigating performance of spot weld groups is being done on a structural Mode I (Caiman) test where a part is deformed producing a tensile loading condition on a joined region so that failure propagation along the glue/weld line can be examined as shown below. The Caiman may be executed at both quasi-static and dynamic rates to investigate any potential rate sensitivity of the desired joining method. Using high speed Infrared Thermography available at the University of Waterloo the exact time and location of each joint failure can be characterized through the distribution of plastic work and used to validate the joining material models in crash simulations.