Damage-Based Modelling of Stretch-Flange Forming
Aluminum alloy sheet is a primary candidate for use in automotive body panels due to its good strength and stiffness-to-weight ratios, recyclability and moderate formability. Stretch flange features are of particular interest since they are used in structural inner door cut-outs where optimum formability is required. The materials used in this work are AA5182 and AA5754 aluminum alloy sheet of 1 and 1.6mm thickness. The inner cutout radius varies from 88mm to 98mm. The formability of a stretch flange from a blank is greatly dependent upon the cutout radius and the blank thickness.
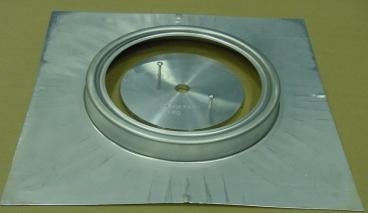
Formed AA5184 Z-Flange (insert shows initial cut-out size)
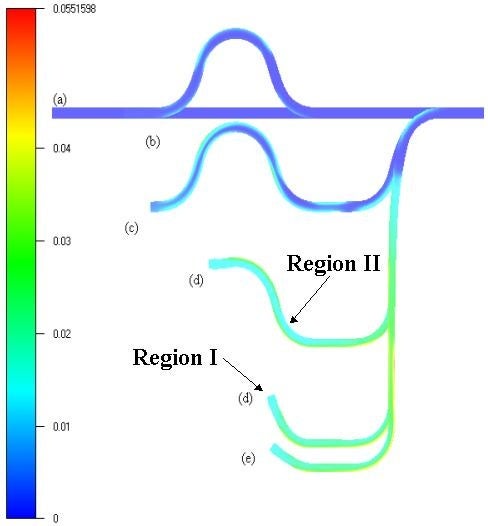
Gurson-based damage model porosity predictions for AA5182, 1.6mm, 92mm cutout. Failure is suppressed through the use of high material coalescence threshold
Quantitative Stereology of Ductile Damage
Metallurgical aspects of formability in AA5182 and AA5754 and their effect on the damage mechanisms are studied. Quantitative metallography characterization reveals extensive damage induced by the second phase particles. This damage occurs at the region immediately beneath the drawbead profile due to bending/unbending effects as predicted by the FE calculation. AA5182 presents higher damage (porosity) than AA5754 due to its higher initial second phase particle areal fraction.
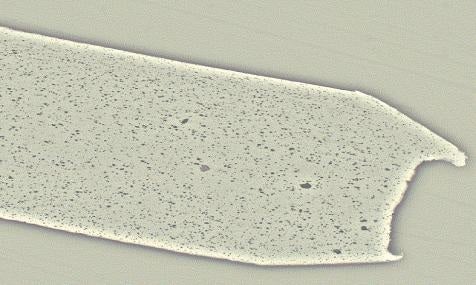
Damage distribution around inner edge of flange (Region I) at 90% limit strain: AA 5182, 1.6 mm. Average porosity value is 3%. Specimen was sectioned through thickness
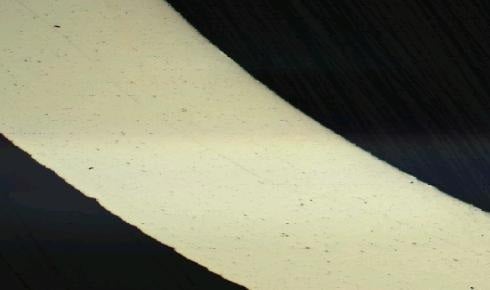
Damage distribution in a bending area (Region II) at 75% limit strain: AA5754, 1.6 mm. Average porosity value is approximately 0.6%.
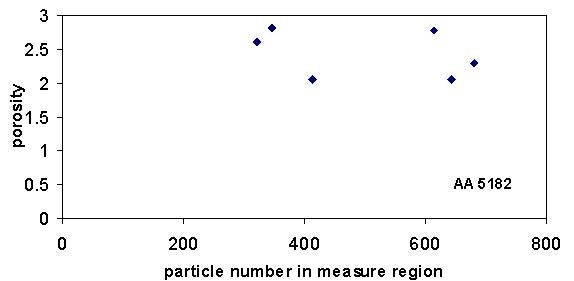
Measured porosity values for various particle fields in the deformed region (II) of the flange cross-section
Damage Percolation/FE Coupled Model
A damage percolation model has been implemented to predict the influence of particle field/void damage heterogeneity on onset of fracture through void coalescence. Second phase particle fields are acquired using digital image acquisition and then mapped onto a finite element mesh used to simulate metal forming or impact. Continuum-level strains and stresses are predicted by the finite element code (LS-DYNA) while damage evolution through void nucleation, growth and coalescence is calculated by the damage percolation code.
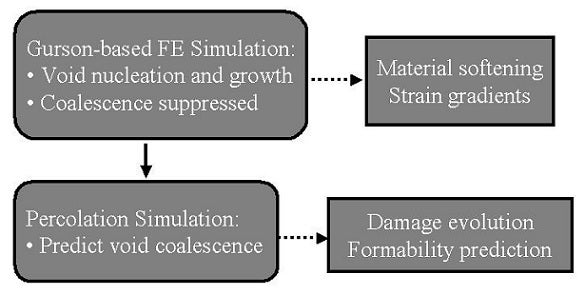
Predicted Void Evolution In Particle Fields
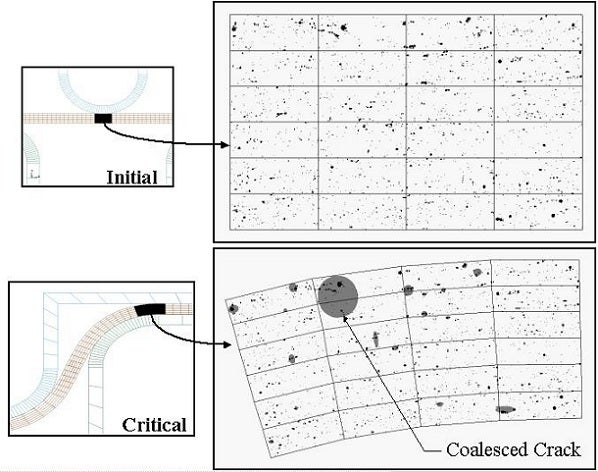
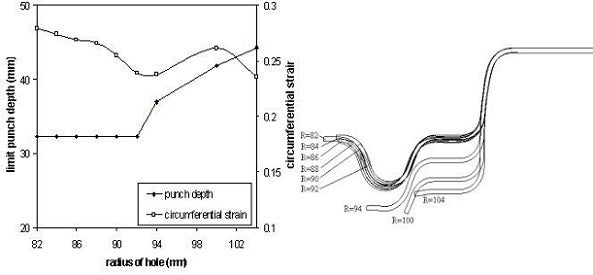
Formability Predictions from Coupled Model
Extension to Three-Dimensions
The coupled damage percolation model has been extended to utilize 3D images acquired using Synchrotron X-Ray tomography.
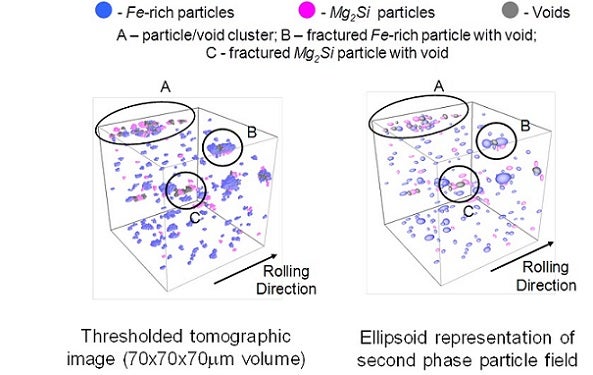
Particle clusters and as-rolled void damage extracted from 3D X-Ray tomographic image
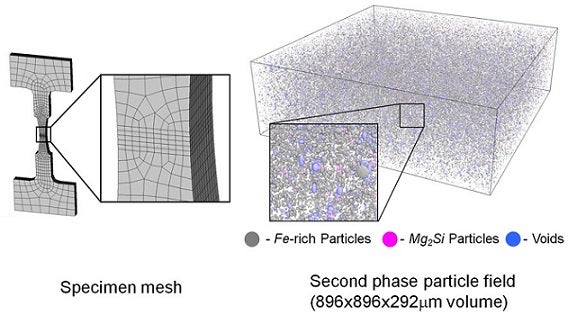