Introduction
Aluminum alloys have been the material of choice for heat exchangers in automotive thermal management systems since the mid-1970s. Today, clad aluminum brazing sheet is favored for its good corrosion resistance and strong braze performance. This clad sheet generally comprises a 3000-series aluminum alloy core, with a clad layer of lower melting-point 4000-series cladding. Unfortunately, such brazing alloys offer relatively poor room temperature formability, worse than aluminum alloys under consideration for automotive structural applications, which imposes limitations on part complexity and ultimately heat exchanger performance. The reduced formability also mandates more expensive progressive die systems to meet formability targets, and reduces confidence in manufacturability assessment.
Another area of research within warm forming of this braze sheet is the potential to reduce springback of the components after forming. For optimal braze performance, it is necessary to have very flat parts such that the braze surfaces make good contact and can produce a strong bond. With higher temper alloys, the elevated yield stress results in an increased level of springback. By warm forming at higher temperatures, the yield stress is reduced and thus the springback improves.
Constitutive Modelling
The material behaviour at various temperatures was measured through elevated temperature uniaxial tension tests. The figure below demonstrates the strong dependence of the stress-strain response on temperature. Phenomenological and physically based constitutive models were fit to the experimental data and it was shown that the modified Voce constitutive model best captured the hardening response at various temperatures, as shown below.
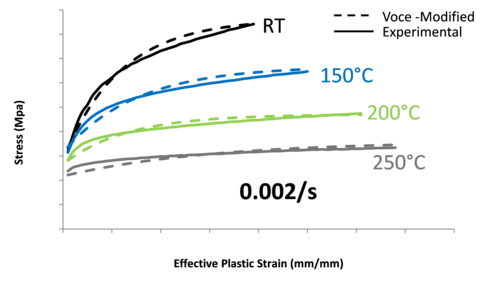
Stress-Strain curves at various temperature for 0.2 mm O-temper sheet. Experiment and Simulation.
Warm Formability
To improve the modelling capabilities, Forming Limit Curves (FLCs) were developed through a series of Limiting Dome height (LDH) experiments at various temperatures. Digital Image Correlation (DIC) was used to measure the Major and Minor strains prior to the onset of necking. These specimens are shown, below.
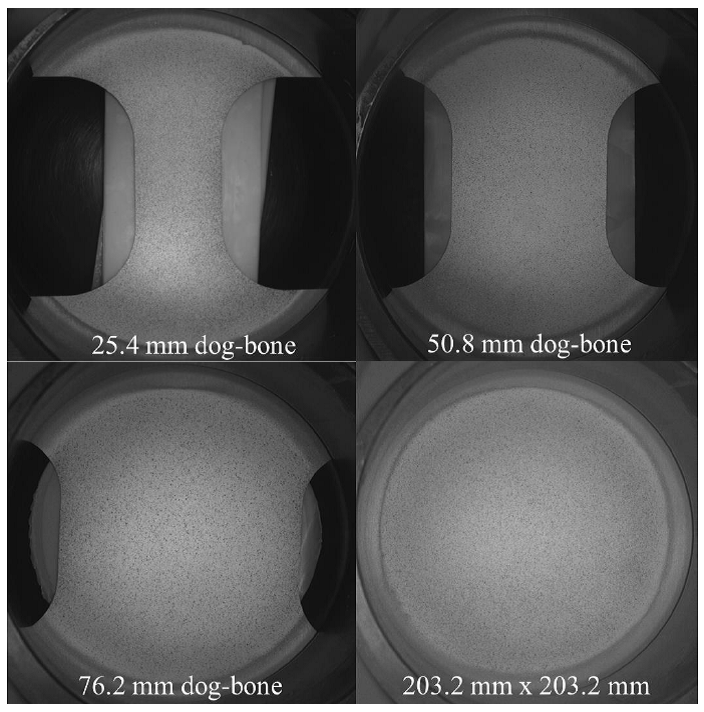
Dogbone Specimens used in the LDH experiments. The speckle pattern is used for the DIC measurements.
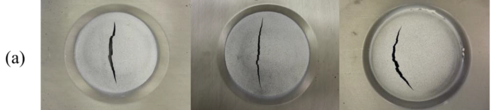
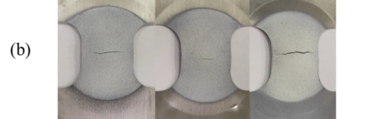
LDH specimens after testing for several Temper conditions at 250°C. (a) Biaxial specimens, and (b) dogbone specimens.
It can be seen from the following FLCs that the limiting strain before failure at 250°C is approximately double from that at room temperature (RT). Additionally, the much stronger H24 temper has similar formability at 250°C compared to O temper at RT.
![]() O temper material |
![]() O temper material |
![]() H22 temper material |
![]() |
Forming Limit Curves in this study
Warm Deep Draw Experiments
Warm forming experiments on a clad aluminum brazing sheet are conducted to characterize the material’s behaviour at elevated temperatures and strain rates, develop material constitutive models, determine the effect of warm forming on the deep drawing process, and validate finite element models. A schematic of the warm forming apparatus at the University of Waterloo is shown below for the deep drawing configuration. Warm stretch-forming tooling is also available.
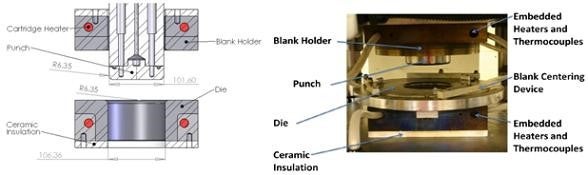
A schematic and photograph of the warm deep drawing apparatus
For this work, non-isothermal warm forming is conducted (where the punch is cooled, while the blank holder and die are heated). Non-isothermal warm forming allows high material strength to be maintained near the punch radius where fracture typically occurs. The heated binder and die allow the flange area to flow more easily at elevated temperatures, which reduces the magnitude of stress in the cup sidewall and reduces tooling loads. Deep drawing experiments showed that a 9" diameter blank could not be formed at room temperature, but at a die/binder temperature of 250°C, the blank was fully drawn as shown, below.
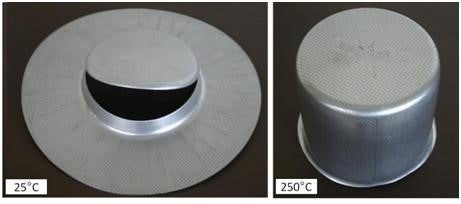
A deep drawn cup at room temperature and 250°C
Using the Bergstrom constitutive model, coupled thermo-mechanical finite element simulations of the deep drawing experiments accurately predicted the strain and thickness distributions, as shown in the major strain comparison below. The punch loads were also predicted accurately for the Teflon lubricant used in the study.
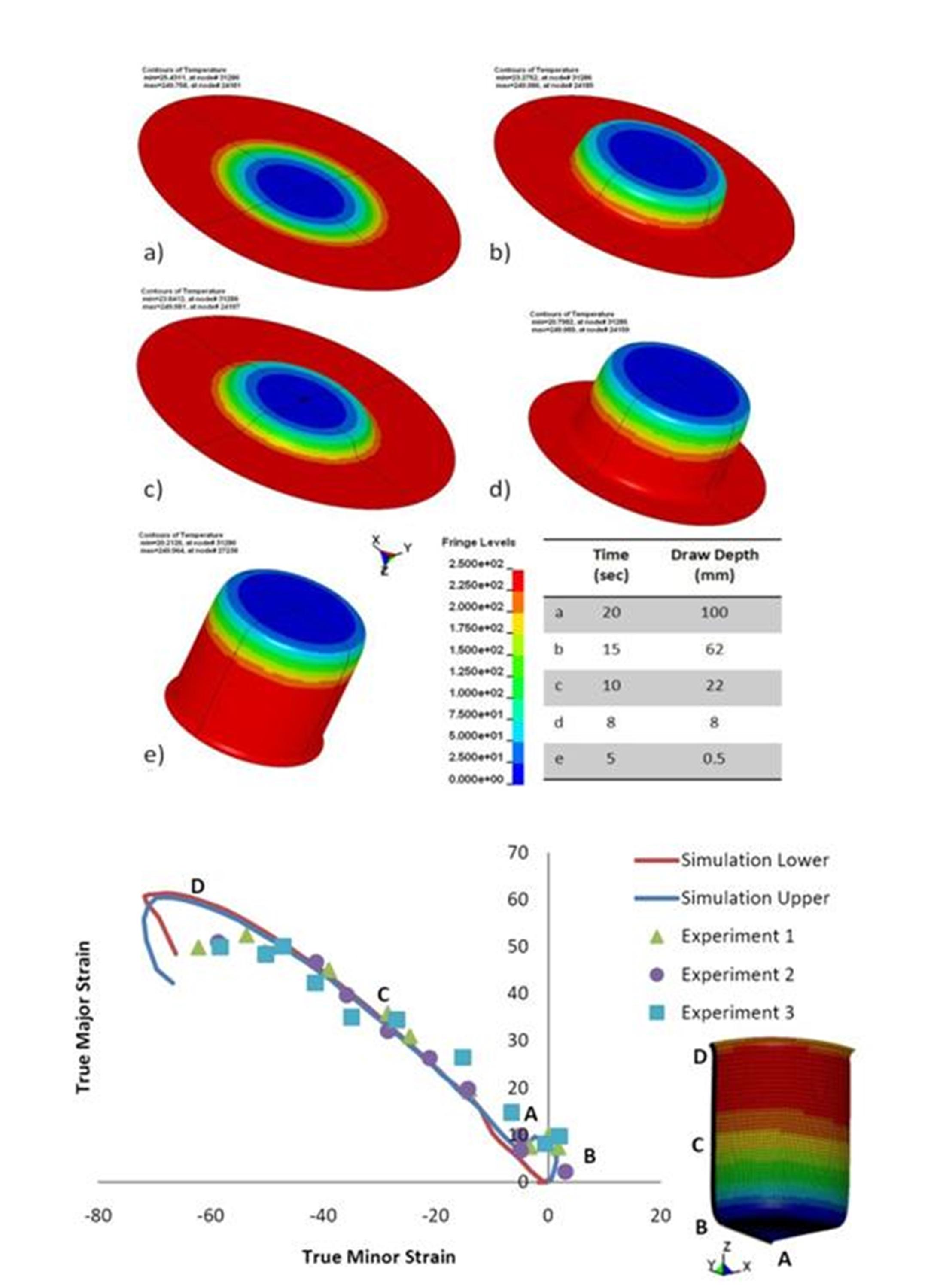
Non-isothermal deep drawing, showing contours of temperature with a chilled punch and heated die/binder
Springback
Another major difficulty in forming complicated geometries, especially for higher strength/temper alloys, is the effect of springback on the final part geometry. There is a desire to use higher temper alloys for these heat exchanger components due to the benefits of overall component strength increase, as well as improved corrosion response. This does, however, come at the cost of reduced formability and increased springback at room temperature. By applying a warm-forming strategy, it is possible to drastically reduce the springback of these materials compared to a conventional cold-form operation (see below).
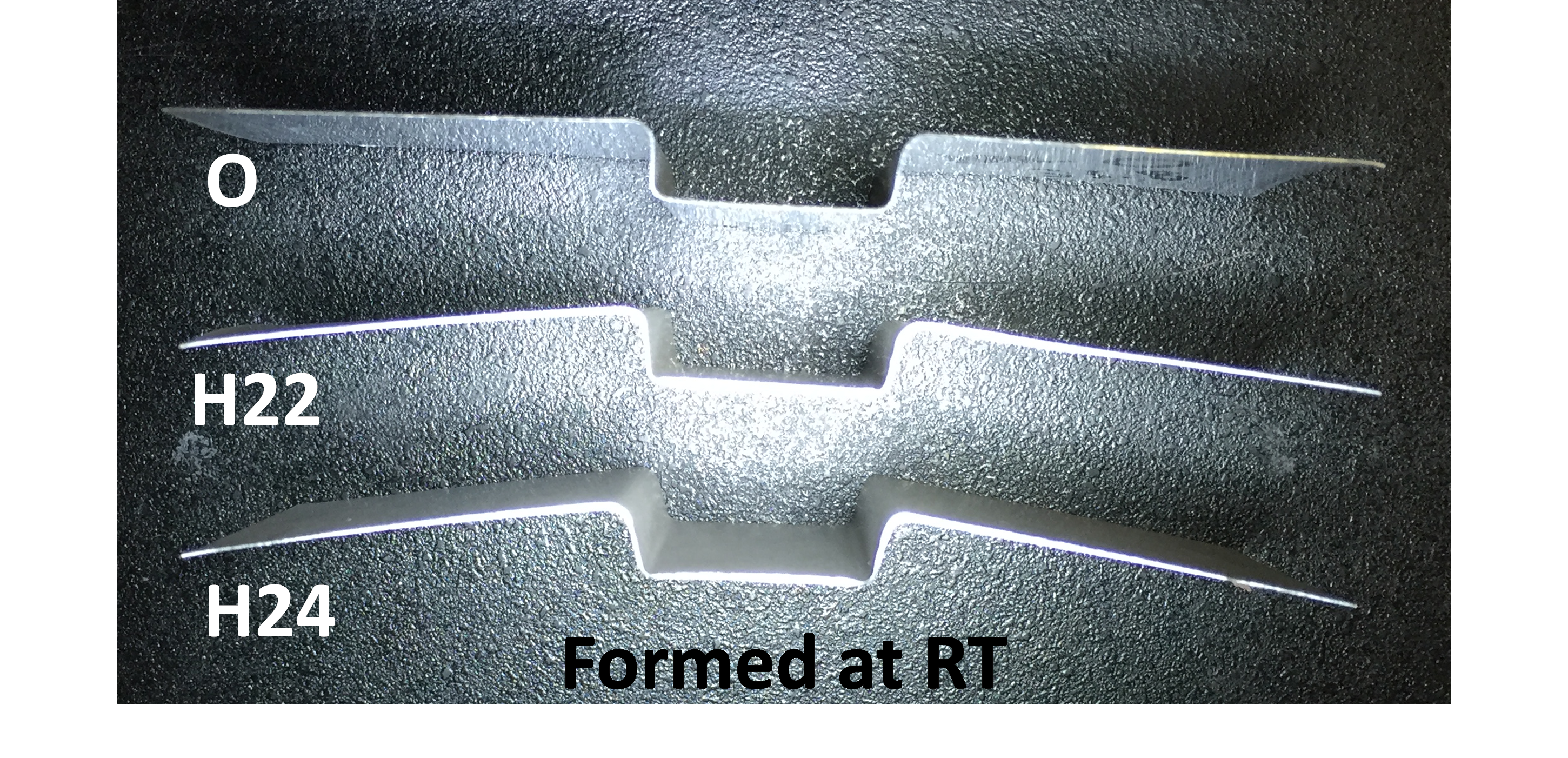

Springback of braze sheet for three temper conditions at various temperatures
Surrogate Heat Exchanger Plate – Warm Forming and Simulation
The experiments and modelling improvements up to this point can all be applied to the development of a representative heat exchanger component.
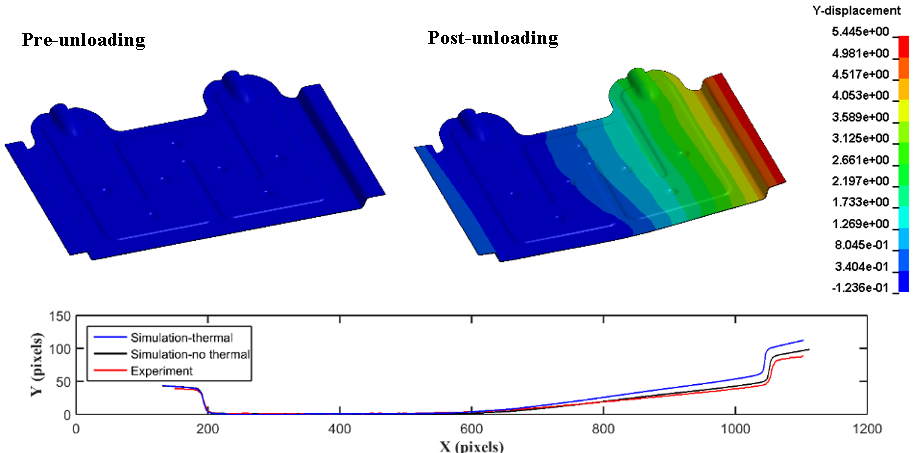
Springback of the surrogate heat exchanger plate, comparing the simulation and experiment.