5.1 General
Any material, be it a chemical, apparatus, an item of furniture, or a fixture can present a hazard, start a fire, or cause injury if not properly handled. You can remove or minimize the hazard with proper handling. Some of the precautions in handling common laboratory equipment are listed below:
- Place equipment as far back from the bench edge as possible.
- All hoses carrying cooling water to an apparatus should be properly clamped.
- Apparatus may tip unless the centre of gravity is within the base area. Use ring stands properly.
- Use round-bottom glass flasks for low-pressure reactions.
- All pressure equipment should be carefully inspected before using.
- Apparatus shielding: where an operation or activity may result in implosion or explosion, laboratory apparatus must be effectively shielded, with appropriate protective equipment or barriers put in place for the protection of the workers involved, and others in the laboratory.
- Know the limitations of the equipment with respect to temperature and pressure; provide for safety pressure relief or vent line.
- Never open a pressure vessel until the internal pressure has been reduced to atmospheric pressure via a relief valve.
- Never examine a pressure gauge without shielding between you and the gauge.
- Turn compressed gas (or vacuum) lines on or off slowly and with caution.
- Always place a capillary relief valve in the system when carrying out a low pressure (vacuum) distillation.
- Use appropriate traps in vacuum systems; avoid corroding the pumps by not using corrosive gases such as halogens, SO2, HCl, etc
- Centrifugal extractors, separators, and dryers should be equipped with an interlocking device that prevents access to the drum or basket while the drum or basket is in motion. All component parts of a centrifuge, particularly the rotor, must be maintained in accordance with the manufacturer’s recommendations and records kept on the number of hours the rotor has been in use.
5.2 Glassware
- Carry tubing vertically rather than horizontally. To break tubing, scratch at the point of the desired break with a single stroke of a triangular file or glass knife; moisten the scratch and place the thumb nails against the tubing directly opposite the scratch and press while pulling hands apart. A towel should be wrapped around the tubing to protect both hands in case the tubing collapses instead of breaking. For tubing with an outside diameter of a 1.5 cm or more, a cutting wheel or hot wire cutter should be used. The tubing end should be fire polished before using.
- When bending glass tubing, place hot glass on a wire gauze. Do not place on a painted ring stand. If handing glass to another person, make sure it is cool first.
- When inserting a glass tube into a stopper, always match stopper holes and tubing size. To avoid cutting the hands, the tubing should be lubricated with glycerol or water and held wrapped in a towel before inserting. Apply necessary force in a lengthwise direction while slowly twisting the tube. It is good practice is to hold the stopper or tubing between the thumb and forefinger and grasp the tubing close to the point of insertion.
- Protect hands with a towel when removing tubing from stopper and do not use pressure. A core borer may also be used to separate rubber and glass.
- Apparatus that can roll such as a thermometer, etc, should be placed on the bench at right angles to the edge keep it from rolling onto the floor.
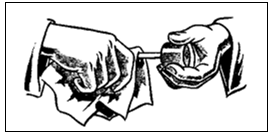
Figure 7: Glass Tube/Rubber Stopper
- Suction flasks will collapse violently under vacuum if cracked or otherwise weakened. Tapping flasks when suction is on full is an unsafe practice. Erlenmeyer and other thin-walled flat bottom flasks are not safe for use under vacuum.
- All containers should be completely emptied and rinsed before cleaning. Organic residues can react with strong oxidizing agents.
- Pipettes with a ragged edge or shortened mouthpieces should be discarded. Plastic pipettors or a propipette should be used for toxic or corrosive materials.
- Release any vacuum from all parts of apparatus before disconnecting.
- Chipped or broken glassware should be discarded into a marked container for disposal.
- Never attempt to connect flexible tubing to glass tubing which has broken, chipped or cracked ends.
- Broken glass should be removed with a brush and dust pan or cardboard and placed in approved containers only. Absorbent cotton may also be used to pick up fine pieces of broken glass. Cotton should be held with tongs. Never use a towel to clean up broken glass.
5.3 Electrical
Electrical equipment, insulating materials and conductors must be suitable for their intended use, approved, where practicable, by the Canadian Standards Association or Electrical Safety Authority (ESA), and handled in an appropriate manner. Warning signs must be posted outside a laboratory where, by the nature of the apparatus of experiment, an electrical hazard may exist (e.g., high voltage).
- All electrical devices must be CSA / UL approved per the UW Safety Office through Electrical Safety Program
-
All new electrical devices (whether purchased or donated) must be inspected by a member of the Safety Committee prior to first use in the lab.
- Avoid makeshift wiring assemblies.
- Don’t use worn connecting or extension cords; replace them immediately when there is any sign of thinning or cracked insulation.
- Don’t use cube taps. Use only multiple-outlet strips.
- Don’t handle any electrical connections with damp hands or when standing in or near water.
- Don’t continue to run a motor after liquid has been spilled on it; turn it off immediately and allow it to dry thoroughly inside and out.
- Use only explosion proof motors and switches on operations in areas exposed to flammable vapours.
- Ground all apparatus, using either 3-prong plugs or pigtail adaptors.
- Check periodically for static accumulation, especially in high voltage situations
5.4 Machine Guarding
Where laboratory equipment or machinery has an exposed moving part or presents an in-running nip hazard which may endanger the safety of a worker, an effective guard or other device which prevents access to the moving part or pinch point shall be installed and maintained.
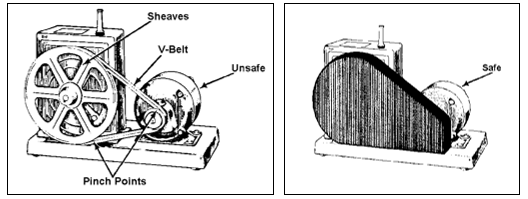
Figure 10: Machine Guarding
5.5 Fume Hoods
Fume hoods are used to reduce levels of hazardous products produced or used during experiments by confining them to an area separate from the laboratory, diluting them with large quantities of air and expelling them long distances from the building.
There are several different types of fume hoods at the University of Waterloo. Among these are:
- Walk-in hood
- Self-contained hood
- Bio-Safety Cabinets
In addition, to these there are special fume hoods for perchloric acid and radioisotopes. Therefore, one must ensure that the appropriate hood is used for each specific reaction or process involving specific chemicals. This information must be provided to students by the laboratory supervisor or laboratory assistants.
A typical modern fume hood consists of the following components:
- The airfoil reduces turbulence in the air entering the hood near the edges and is located at the bottom and sides of the fume hood entrance.
- Air baffle and adjustable slots are used to insure a laminar flow through the hood and to decrease turbulence.
- The sliding sash permits full access to the fume hood when preparing an experiment and partial or full closing while it is taking place to insure proper evacuation of hazardous products.
- The exhaust duct damper is used to set the face velocity of the fume hood. This is normally set between 80 and 120 FPM with the sash set at normal working height. All fume hoods are to be ducted as per Regulation 308 in the Environmental Protection Act.
5.5.1 Construction
Material used in construction should be non-porous and impervious to materials used or produced. For example stainless steel is very good for most radioactive material because it is easily cleaned but will break down when halogenated acids such as Hydrogen Chloride are used.
5.5.2 Fume Hood Safety
- Make sure that the exhaust blower is operating and air is entering the hood, prior to starting an experiment. All fume hoods at UW are fitted with a VentAlert flow monitor or are alarmed in some other way. If the monitor is alarming or not functioning, please call Plant Operations 24 Hr. Service number 33793. If the hood is not working properly please call Plant Operations 24 Hr. Service number 33793 and have the hood repaired prior to using it. The flow monitors must NOT be removed.
- Do not place your face inside the hood. Keep hands out as much as possible. Perform all work involving hazardous or volatile materials in operating fume hoods.
- Connect all electrical devices outside of the hood to avoid sparks which may ignite a flammable or explosive chemical.
- Note that the hood is not a substitute for personal protective equipment.
- Always work at least 6 inches in from the opening of the fume hood.
- Do not modify fume hood.
- Do not use your fume hood as a storage area
- Avoid blocking off baffle exhaust slots in any manner. Elevate large equipment "2" inches off the base of the fume hood.
- Large pieces of equipment or numerous persons standing in front of the fume hood will cause turbulence.
- Be aware of other room ventilation factors that may interfere with your fume hood operation, such as open doors to labs, open windows, blocked exhaust ports or heating and air conditioning vents.
- Avoid cross drafts and disruptive air currents in front of the fume hood.
- Use the sash as a safety shield when boiling materials or conducting an experiment with reactive chemicals.
- Prepare a plan of action in case of an emergency, such as a power failure, especially when using extremely hazardous chemicals or acids.
- Work with the sash at the proper operating level as indicated by the arrows.
- When fume hood is not in use please leave sash closed.
- When fume hood is not in use please insure that all material is in sealed container
5.5.3 Walk-in Fume Hood
Walk in fume hoods are basically a ventilated room with an air baffle at the back and adjustable slots to insure laminar flow. Access is normally gained by sliding or folding doors.
Walk in fume hoods are mainly used to set up large scale experiments or processes, experiments are erected in the walk in fume hood, the doors are closed and the experiment is monitored or controlled remotely.
No protection is provided to persons while inside the walk-in fume hood.\
5.5.4 Self Contained Fume Hoods (Ductless)
Self-contained fume hoods are designed similar to conventional bypass fume hoods but are not ducted to the outside. The air is instead passed through activated charcoal for organic compounds or through a HEPA filter for particulate material and the "clean air" is returned to the laboratory.
The filters must be appropriate to the type of material used or produced and replaced prior to failure.
Lifetimes of HEPA filters are simple to monitor using pressure changes and an external gauge which will indicate when it is time to change the filter. These types of hoods are used to handle dry materials as well as in some bio-hazards.
Life times and absorption efficiencies of activated charcoal filters are extremely variable and should only be used with very low hazard chemicals. All ductless fume hood installations must be approved by the Safety Office.
Ductless fume hoods must not be used for flammable solvents as per Section 4.12.8.3 of the Ontario Fire Code.
5.5.5 Perchloric Acid Fume Hoods
Perchloric acid fume hoods are to be installed and used whenever a process involves the production of perchloric acid fumes. This type of hood is designed to prevent the deposition and build up of perchloric salts on the hood or duct surfaces. Perchloric acid hoods are designed with wash-down devices which periodically (after each use) rinse the fans ducts and fume hoods surfaces with water. The fume hood and duct work is made of stainless steel and the duct work is kept straight, vertical and as seamless as possible to aid in washing away perchloric salts.
- Heating perchloric acid should be undertaken with extreme caution.
- Do not use oil baths or open flames to heat perchloric acid.
- Do not dry filter paper used to collect perchloric acid precipitates.
- Keep perchloric acid away from organic chemicals especially alcohols and glycerol.
- Store perchloric acid in ceramic trays.
5.6 Autoclaves
5.6.1 Hazards
Explosions producing injury and damage are possible. The stored energy in the stream is tremendous and autoclaves differ from other steam receivers in that they have to be opened frequently, and residual pressure may not be detectable by the pressure gauge.
5.6.2 Operations
- Written operating procedures are essential.
- Every operator should be adequately trained in the operation of an autoclave. In particular, they should be made aware of and understand the importance of:
- Ensuring that the autoclave is completely vented before attempting to open the door.
- The function of all operating controls and door interlocking devices.
- The danger of interfering with or bypassing any safety device.
- The correct application of the locking stirrups, swing bolts or door locking mechanism.
- An operator who has not yet acquired sufficient knowledge and experience must be kept under proper supervision by a competent person.
Quality control measures must comply with the manufacturer’s recommendations. All quality control measures must be well documented
- Mechanical: time and temperature graphs, charts or printouts, done during each cycle
- Chemical: time/temperature and/or humidity sensitive tape, strips or pellets, done on each cycle
- Biological: spore-laden strips or vials, done weekly or more frequently if recommended by manufacture.
5.6.3 Controls
- Safe Working Pressure - a suitable reducing valve or other suitable automatic appliance to prevent the safe working pressure being exceeded.
- Safety Valve - a suitable safety valve so adjusted as to permit steam to escape as soon as the safe working pressure is exceeded.
- Accurate Steam Pressure Gauge - to indicate the pressure of the steam in the vessel.
- Isolating Valve - one for each autoclave.
- Interlocks between the door locking mechanism and the steam inlet valve to ensure that steam cannot be turned on unless the door is properly closed and fully locked.
- That the door cannot be unlocked unless the steam inlet valve is closed and the exhaust valve is completely open.
- A test cock or other equivalent device to give an audible and visual indication of internal pressure in the autoclave. This test cock has to be interlocked with the door locking mechanism, so that the test cock will be completely open before the door can start to unlock.
5.6.4 General
- A thorough examination should be done by a Boiler Inspector as prescribed in the regulations.
- A six-weekly check by the Maintenance Engineer(s).
- As per manufactures specification
- Check Safety Valve for intact seal. (replace if damaged or broken)
- Test Safety Valve operation. (test should be conducted at 70% of maximum rated pressure)
- Certificates of inspection must be posted.
- Operating procedure to be written and displayed.
- Autoclaves with automatically opening doors have an electric guard across the doorway which prevents the closing of the door if the operator is in this danger area.
- Check ovens periodically to ensure that the seals to the closures are in good conditions, and safety devices to prevent excessive temperatures and pressures are in working order.
- Train all users in proper techniques and use practices.
- Use non-sealed Pyrex containers which are designed for the temperatures and pressures of the autoclave, as liquids placed in sealed bottles or in ordinary glass bottles may rupture.
- Be aware that if the unit is set to exhaust rapidly, as might be done for instrumental sterilization, boiling may take place in bottles of liquids, with a consequent loss of liquids into the autoclave.
- Do not run flammable liquids or chemicals which could become unstable at the temperatures reached in the autoclave through the sterilizing cycle.
- Post operating instructions and a list of safety practices near the autoclave for easy reference.
5.7 Ovens
- Ovens are used in laboratories for baking or curing materials, out-gassing, removing water from samples, drying glassware, or in some cases providing a controlled, elevated temperature for an experiment.
- Equip every oven with a back-up thermostat or temperature controller which will either control the unit or shut the oven down should the primary one fail.
- Do not use a unit with only a single thermostat for long, unattended processes.
- Do not use an oven to heat any material from which a toxic vapour or gas would be expected to evolve unless provisions are made to exhaust the fumes, as would be done with a fume hood.
- Do not use mercury thermometers in ovens.
5.8 Refrigerators
Laboratory explosions have resulted when ordinary domestic refrigerators have been used for storage of flammable liquids, and leaking vapours have reached one of the many ignition sources within such refrigerators.
5.8.1. Approved Equipment
Refrigerators and any other equipment used to store flammable materials must be certified as such the C.S.A. testing laboratories. No attempt should be made to modify existing refrigerators or other equipment for such use.
Laboratory centrifuges, deep freeze cabinets, environmental chambers, and walk-in refrigerator chests shall be similarly protected.
5.8.2. Precautions
Never store food and beverages in a refrigerator containing laboratory chemicals.
Seal all containers inside the refrigerator tightly and clearly label them (WHMIS label).
5.8.3 Service and Repair
Refrigeration equipment is to be serviced by a person certified under the regulation (Environmental Protection Act).
Refrigeration equipment can be disposed of only after the refrigerant has been removed and the equipment tagged by a person certified under the regulation.
5.9 Maintenance
Any deficiencies in laboratory equipment should be reported to your supervisor. The equipment should be taken out of service until it is repaired.
5.9.1 Installation of Equipment
All equipment shall be installed according to Policy 22-REGULATIONS GOVERNING THE INSTALLATION OF EQUIPMENT IN UNIVERSITY BUILDINGS.
5.9.2 Building Maintenance
Report problems to Plant Operations 24 hr. Service Number Ext. 33793 or 519 888-4813