- Smoking is not permitted in any laboratory. (OHSA, UW Policy #29)
- Food or beverages are not to be stored, prepared or consumed in laboratories. (OHSA)
- All injuries are to be reported.
- People who are under 14 years of age are not permitted in laboratories unless accompanied at all times by a knowledgeable person who is 19 years of age or older. (OHSA)
3.1 Research Project Health and Safety Assessment
3.1.1 Requirements
The requirements noted below are official policies in the Department of Chemical Engineering. The abbreviation OHSA stands for the Occupational Health and Safety Act (Ontario).
Based on the desirability for self-awareness, supervisors, workers, or others using chemicals and other hazardous or potentially-hazardous materials or equipment are to use the following procedures as a minimum standard:
(a) At the time they first are engaged to work on a particular research project, all persons (being paid a salary, or stipend or not) must become informed of the physicochemical properties, hazard ratings (e.g., acute or chronic toxicity), necessary safety precautions, etc. for all chemicals and other potentially hazardous materials or equipment expected to be used for any purpose. Relevant information may be provided by the supervisor (preferably in written form) [see OHSA] or may be obtained directly by the person who will perform the research [see (b) below]. The supervisor and researchers also should review all other required safety practices at that time. (The requirement of supervisors to inform workers is stipulated in the OHSA)
(b) Before starting hands-on laboratory research, the person who will perform the research must prepare in sufficient scope and detail a written Health and Safety Assessment Report applicable to her or his project (see section 3.1.2) and submit it to the project supervisor for approval.
(c) Before a researcher (paid or unpaid) starts to use a new chemical or other potentially hazardous substance or equipment as a result of:
(i) Her or his own determination, or
(ii) Upon instructions of the supervisor,
the researcher should not proceed with its use in any manner until becoming thoroughly familiar with its physicochemical properties, hazard ratings, safe handling procedures, etc. (i.e., until the appropriate source documents have been obtained). For case (i) above, the researcher shall not proceed until the supervisor is advised of the intended use of the chemical, etc.
(d) Supervisors and all others engaged in research are to regularly (annually, as a minimum) review experimental conditions and practices (methods, equipment, etc.) as they relate to health and safety. The recommended form of review is a written addendum to the initial Health and Safety Assessment Report that was prepared by the researcher [see (b), above].
3.1.2 Guidelines for Report Preparation
The health and safety assessment and the written Report should include, but not necessarily be restricted to, the following aspects and types of hazards:
- A description of what the research goals are and what research procedure that is planned to achieve the goal (ie: use of compressed gases, reactor vessel, mixing certain chemicals, instruments, etc) .
- Hazards identification:
- Potential fire or explosion hazards
- Chemical or biological toxicity, carcinogenicity, etc
- Use of designated substances (see section 4.1) or regulated agents (OHSA)
- High pressures, temperatures
- Electrical (e.g., high voltage)
- Radioactivity
- Potential of falling objects
- Rotating equipment – entanglement or body contact
- Potential for leaks or spills and containment requirements
- Personal Protective Equipment (PPE – ie: gloves, safety glasses, lab coats)
- Safe start-up and shutdown procedures, including emergencies
Your Safety Report must include a Laboratory Project Hazard and Risk Assessment. If you are going to be working with nanomaterials, your Safety Report must also include a Nanomaterials Risk Assessment Form.
When conducting the above assessment and writing the Report, consider all chemicals (process and analytical), equipment (process and analytical) and procedures used in the course of the research, either continually or periodically.
The written Report should include:
1. A list of all chemicals, organisms and other biological agents, etc. used for process and analytical purposes. For those which are hazardous beyond the normal level, copies of literature describing their particular hazards, toxicity rating, etc. are to be appended to the written report [for chemicals, you may obtain this information from appropriate references or by consulting the Director of Safety (see p. vi)].
2. A list of all equipment used, including analytical equipment, and specific identification of any potentially hazardous features (e.g., high pressure, high voltage, or rotating parts).
3. Point-form notes of all special operating procedures which are now followed or should be followed to ensure safe operation of the experimental apparatus, analytical equipment, etc.
4. A schedule of recommended routine maintenance work or inspections necessary for continued safe operation of equipment.
5. Identification of any operations that are or may be potentially hazardous to others working in the same area or in nearby areas.
6. Potential for release of noxious or hazardous substances into the environment (e.g., into the air; or into the water system through drains).
7. Special procedures for handling accidental spills, power failures, or other emergencies.
The Report should be of a format useful for quick consultation (e.g., include a Table of Contents and use appropriate headings and subheadings). Excluding the Table of Contents and Appendices, the Report should be about 5 to 15 pages in length, depending on the scope and complexity of the particular project. Co-investigators should submit a jointly-prepared assessment report.
After review by the supervisor(s), the Report should be discussed with the person(s) who prepared it. A copy of the approved Research Project Health and Safety Assessment Report or any later additions or revisions should be submitted promptly to the Department Health and Safety Co-ordinator.
3.2 General Safety Awareness and Practices
- Know all the safety rules and procedures that apply to your work. IF YOU DO NOT UNDERSTAND - ASK!
- Determine the potential hazards, appropriate safety precautions and proper waste disposal techniques before beginning any new operation.
- Know the location and proper use of emergency equipment (safety showers, eye baths, fire extinguisher, and first aid kits)
- Be familiar with emergency procedures (exits, alarm stations, and evacuation routes)
- Do not eat, drink, smoke or apply cosmetics in any laboratory.
- Do not pipette or start siphons by mouth.
- Wash hands with soap and water before leaving the work area. This applies even if one has been wearing gloves
- Know what protective equipment is available and use the proper type for each experiment
- Ensure that all chemicals are correctly and clearly labeled.
- Use laboratory equipment only for its designated purpose.
- Combine reagents in appropriate order. (i.e., pour water first and then acid; and avoid adding solids to hot liquids)
- Wipe up spills immediately.
- Keep sinks clean. Practice good housekeeping and clean up at the end lab work.
- Keep aisles free of obstructions (chairs, stools, boxes, etc.). Apparatus set up should be as far back on bench as conveniently possible so it will not tip onto floor.
- Do not set up apparatus so that it is necessary to reach through the assembly to turn water, gas, or electricity on or off. Assemble apparatus so that control valves and switches will remain accessible if a fire should occur.
- Confine long hair and loose clothing or jewelry when in the laboratory
- Avoid exposures to gases, vapors, and aerosols (USE FUME HOODS)
- Do not leave experiments in process unattended. (If you must leave equipment running over night please post contact information near experiment)
- Identify shut off switches and ensure they are easily accessible.
- Children should not be allowed in the laboratory.
- Avoid working alone at night.
- Keep laboratories locked when unoccupied. (Leave doors unlocked while working in laboratory in case assistance is needed)
- Do NOT wear protective gloves outside the lab area, to avoid contamination on door handles, water fountains, etc.
If you are not already fully knowledgeable of the following, please learn about the following:
- emergency telephone numbers (see p. iv)
- proper use of fire extinguishers
- proper means of disposing of broken glassware
- proper disposal of “sharps”
- proper use of safety showers and eye-wash fountains
- correct storage and handling or dispensing of flammable liquids
- proper procedures for radiation monitoring and control, if applicable
- proper procedures for chemical or biological spill clean-up and disposal
- correct operation of fume hoods or biological safety cabinets, if applicable
A departmental safety representative or the Director of Safety (see p. iv) can advise you on all health and safety practices, including those mentioned above.
In the laboratory areas where you work, find and remember the location of:
- telephones
- exits, especially emergency exit routes should be planned in advance (see p. v)
- fire extinguishers
- fire alarm stations
- safety showers
- eye-wash stations
- first-aid kit
- designated building door for ambulance arrival (see p. v)
3.3 Rules for Working Alone
You should never work alone in a laboratory if the research involves operations that may be hazardous or potentially hazardous to a significant degree. Some examples are: the use of large quantities of flammable liquids (i.e., more than about 2 L) or smaller amounts of flammable liquids contained in an apparatus at elevated temperature and pressure; toxic gases, liquids, or solids; high-pressure systems; moving equipment and machinery (excluding pumps and compressors with the required shaft guards in place); cold rooms. If you are working inside any confined space, vessel or other chamber from which escape would be difficult or delayed, the OHSA Act requires that there be at least one person in attendance outside of the work area at all times.
3.3.1 Faculty, Postdoctoral Fellows, Graduate Students, and Research Employees
Subject to the general guidelines noted above, normally it is appropriate for Postdoctoral Fellows, graduate students, Co-op Work Term Student employees and other researchers with equivalent experience and competence, and who have prepared an approved health and safety assessment report (see section 3.1), to work alone in areas other than offices, as may faculty. However, precautionary measures are required. Use the risk assessment tool to determine whether you can work alone or not.
When working alone and while you are inside the laboratory room, whenever possible or appropriate leave the doors unlocked, or open, so that you may be reached quickly if an accident happens. When doubt exists as to whether an operation or job function meets the suggested guidelines for working alone, the researcher, supervisor and the Director of Safety should jointly assess the situation and reach a mutually-agreeable decision.
3.3.2 Undergraduate Research Students
The term undergraduate research students means all undergraduate students involved in research pertaining to degree requirements, all those who receive Faculty of Engineering Undergraduate Research Assistantships or Scholarships, and all those who are enrolled in the Combined B.A.Sc.-M.A.Sc. program, and who are conducting their research in the Department of Chemical Engineering, or using other facilities provided for their research.
To perform experimental research work in a laboratory, an undergraduate student must have prior authorization from her or his instructor. The granting of such authorization should be contingent upon the prior submission by the undergraduate researcher of an acceptable work plan (for a 4A/4B coursework project) and of an acceptable Health and Safety Assessment Report (see section 3.1).
3.4 Fire Prevention
Fire may be caused by flammable liquids, electrical hazards, smoking, hot surfaces, sparks, poor housekeeping, and arson. Precautions must be taken to aid in the prevention of fire to reduce the risk of loss of life and property.
Flammable Liquids
- Store flammable liquids only in approved safety cans or storage cabinets. Label the containers and keep them in areas that are well ventilated, away from any heat sources.
- Clean up spills immediately.
- Store oily rags in a covered metal container with a self-closing cover and the containers must be emptied daily.
- Never smoke or light a match near flammable liquids.
Electrical Fire Hazards
- Check tools, equipment, extension cords and plugs for worn spots and exposed wires.
- Keep switch boxes clean and closed.
- Don't try to use broken power tools or equipment, report them to the supervisor.
- Repairs on broken power tools should only be performed by competent personnel.
- Inspect equipment at regular intervals.
Hot Surfaces
- Keep floor clean to prevent falling sparks and hot metal from causing a fire. Cover wood floors with metal or other non-combustible material.
- Use fire retardant curtains.
- Turn off and unplug appliances such as soldering irons and coffee pots when workday is over.
Sparks
- Use brass or plastic tools when working with flammable liquids.
- Oil motor bearings frequently.
- Take precautions with metal to metal or metal to concrete contacts.
- Ensure containers for flammable liquids are grounded and bonded to prevent static electricity from causing a spark.
3.5 Fire Fighting: Types of Fires and Fire Extinguishers
If you discover a fire:
- Attempt to extinguish fire only if you can do it safely.
- Immediately warn others: activate the fire alarm and start evacuation of the building.
- See emergency procedures on p. i of this manual for further information.
3.5.1 Types of Fires
Table 2 shows the four major fire classifications: Class A, Class B, Class C, and Class D fires. The classification system is based in part on the type of combustible material involved.
Table 2: Classification of Fires and Required Types of Extinguishers
Class |
Type of Material |
Extinguishers |
||
Water |
CO2 [1] |
Dry Chemical |
||
A |
wood, cloth, paper (common combustible materials) |
Good |
Good |
Good |
B |
flammable liquids or gases (solvents, petroleum products) |
Prohibited |
Good |
Good |
C |
energized electrical equipment involved in Class A or B fires |
Prohibited |
Good |
Satisfactory but not desirable |
D |
Active metals |
Prohibited (see Note 1) |
Prohibited (see Note 1) |
Permitted |
Fire Extinguisher Use In Case of Fire
- Laboratories typically only have one type of extinguisher, if that is true and the extinguisher is incompatible with the type of fire then leave the room close the door and pull the fire alarm.
- Quickly size up the situation, and stay calm. Most fire extinguishers only last for 30-40 seconds.
- Fire extinguishers are located near room exits or in hose cabinets located in the hall ways.
- Get everyone out, pull fire alarm. If fire is still small, fight it using appropriate extinguisher.
- Keep near the door - so you have an escape.
- Stay low - out of heat and smoke.
- Select the proper fire extinguisher for the job.
- Use the PASS technique with the appropriate fire extinguisher:
- Pull the pin or locking device.
- Aim low, at the base of the fire.
- Squeeze the handle.
- Sweep the agent slowly and evenly at the base of the fire.
- Stay outside small rooms - shoot stream in.
- Ventilate only after fire is out.
- Have the Waterloo Fire Department Check to make sure the fire is out.
Figure 1: Fire Extinguishers, Applications, and Methods of Use
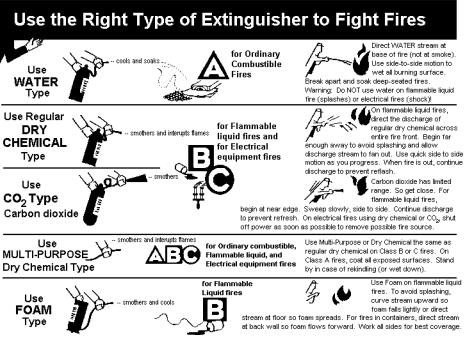
You should frequently check all fire extinguishers located in your work area(s) to verify that maintenance personnel have serviced them at the required intervals and that they are in good working condition (i.e., fully loaded and pressurized).
If you think you might not know how to use a fire extinguisher, call the Director of Safety (x35814) and arrange for a demonstration (at which time you also may operate an extinguisher yourself).
3.5.3 Clothing Fires
If your clothing or any part of your body (e.g., your hair) catches fire, immediately drop to the floor and roll. Do not run. In case of ignition of another person’s clothing or body, immediately knock that person to the floor and roll that person to smother the flames. Rolling on the floor not only smothers the fire, but also serves to keep flames away from the victim’s face and reduces inhalation of smoke.
The use of safety showers or fire blankets is of secondary importance. They should be used only when immediately available.
3.6 Personal Protection
3.6.1 Eye and Face (OHSA)
Instructors, supervisors and all other persons in authority shall explain the reasons why safety glasses or other types of eye protection equipment should be worn and it will be their responsibility to ensure that students, faculty, staff and visitors are provided with eye protectors in all areas were required.
All persons assigned to, or entering areas which have any of the following hazards must wear eye protectors:
- Sparks, open flame and spatters.
- Molten metals.
- Research activities involving high energy, the possibility of flying particles, explosion or implosion of vessels.
- Hazardous chemicals.
- Shops: wood or metal processing, particularly grinding, welding, chipping, sawing and sanding.
- Injurious radiant energy, for example, welding, ultra-violet light, lasers and brasing.
Table 3: Eye Safety Selection Guide
Type |
Recommended for |
---|---|
Standard Safety Glasses |
Protection from: flying particles such as metal, wood, glass or plastic coming from in front. |
Safety Glasses with Semi-side Shields |
Protection from: flying particles coming from in front of you or from your side. |
Safety Glasses with Eye-cup Side Shields |
Protection from: flying particles from the front, side, top or bottom. |
Goggles with Regular Ventilation |
Protection from: dusts, sparks and flying particles coming from many angles. |
Goggles with Hooded Ventilation |
Protection from: chemical splashes, dusts, sparks and flying particles coming from many angles. |
Face Shields (Used with other eye protection) |
Protection from: splashes, heat, glare and flying particles, if worn over safety glasses or goggles. Face shields alone do not provide adequate eye protection. |
Figure 2: Eye Protection Devices
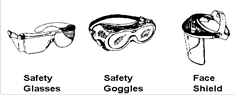
If a chemical or other substance enters the eye, flowing fresh water (eye fountain or eye-wash station at sink) should be used immediately to flush out the eye for a minimum of 10 minutes. After flushing, report immediately to the UW Health Services. When Health Services is closed, have someone immediately take you to the Grand River Hospital Emergency Ward. If you are working alone, call UW Police (x22222) for help.
Contact lenses are not to be worn if water-soluble gases of a corrosive or irritating nature, vapours, dusts or other hazardous substances could be released into the work environment. Contact lenses can trap and hold damaging materials or chemicals against the eyeball, or the lenses may melt onto the eyeball in the presence of some dissolved chemical vapours.
3.6.2 Feet (OHSA)
Classification of Safety Footwear
- All protective footwear must conform to CS Standard Z195-M92 “Protective Footwear”
- Select CSA-certified footwear. Ensure that it has the proper rating for the hazard and the proper sole for the working conditions
- Employees requiring foot protection shall be aided by subsidy paid by the university, prior approval must be obtained from your supervisor
- Use metatarsal protection (top of the foot between the toes and ankle) where there is a potential for injury
Table 4: Selection Guide for Safety Footwear
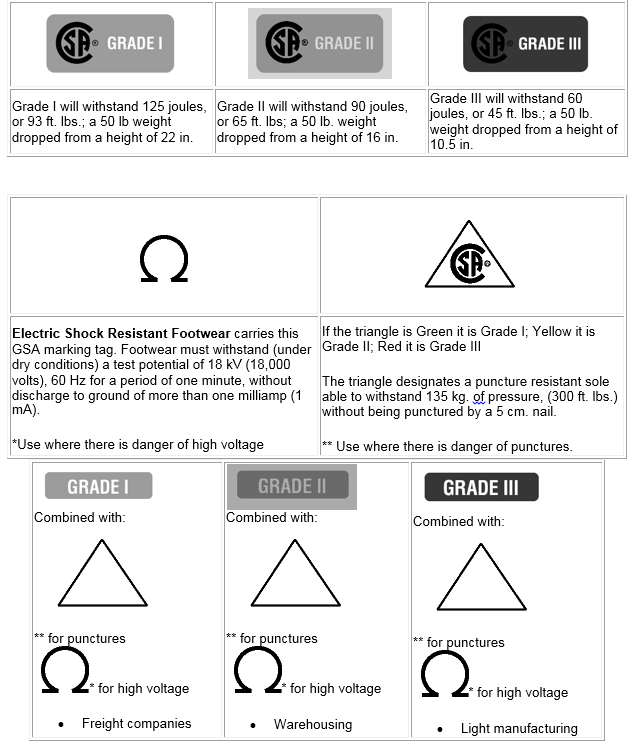
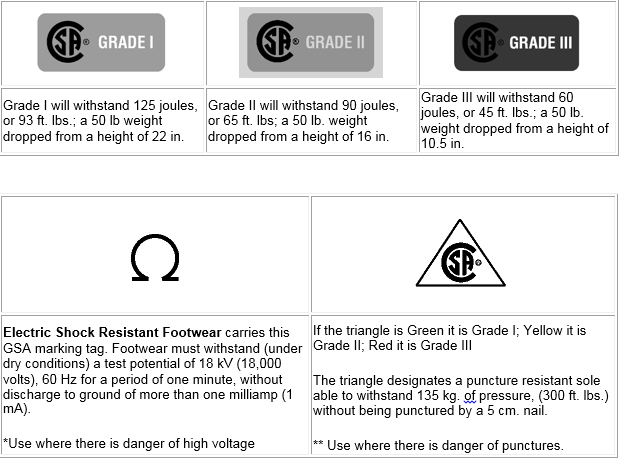
3.6.3 Hands
3.6.3.1 Handling Chemicals or Biological Agents
Gloves reduce the exposure of our hands to hazardous materials. No single material will protect against all chemicals, so glove selection must be made for each type of chemical. Latex gloves may provide adequate protection against dilute aqueous solutions; they however provide no protection against exposure to most solvents. Table 5 below is intended as a guideline for selection of the appropriate protective glove. Manufacturers can supply specific information on the choice of glove.
Note: Nano-materials are also a challenge with regard to penetration through gloves; sometimes double gloving is recommended. See also section 4.2.5.10 which details PPE for handling different types of nano-materials.
Glove selection should be based on the following criteria:
Degradation
Degradation due to contact with chemicals causes the glove material to soften, swell, shrink, stretch, dissolve, or to become hard and brittle.
Permeation
Permeation is the result of molecular diffusion of a chemical through a glove material. There may be permeation without obvious signs of degradation. Permeation is quantified by breakthrough time and permeation rate.
Breakthrough Time
Breakthrough Time is the time it takes for a particular chemical to pass through a protective material.
Permeation Rate
The speed at which the chemical moves through the protective material once it has broken through.
Exposure
Glove performance is decreased significantly as chemical exposure is increased by the following:
- Chemical concentration
- Direct immersion
- Pervious exposures
Temperature
Permeation test data are obtained at room temperature (20 to 25 degrees Celsius). If chemicals are being used at temperatures higher than this glove performance may be significantly affected.
Glove Thickness
Any chemical will permeate a protective material given enough time. The breakthrough time for a thicker material will be longer than that of a thinner material, providing superior chemical resistance. When choosing a chemically resistant glove manual dexterity must also be taken into account.
Manufacturer
Differences in production of materials results in variations of permeation and degradation between manufactures. Test data for a particular manufacture should be consulted prior to selecting a chemically resistant glove.
Chemical Purity
Permeation testing is conducted using pure chemicals. Mixtures of chemicals will significantly alter the permeation rate and degradation of a material.
Physical Resistance
Chemical penetration through a tear or hole in a glove will cause a much greater chemical exposure potential than caused by molecular permeation.
Selection Guide
This guide is for general reference only, for specific recommendations contact the glove manufacturer, SDS or the Safety Office.
Table 5: Chemical Resistance of Glove Materials
Gloves |
|
Chemical Resistance |
|||||
RECOMMENDED |
NOT RECOMMENDED |
||||||
Latex |
Natural Rubber |
Weak Acids, Weak bases, alcohols, aqueous solutions |
Oils, greases and organics |
||||
Butyl |
Synthetic Rubber |
Aldehydes, ketones, esters, glycol ethers, polar organic solvents |
Aliphatic, aromatic and chlorinated solvents |
||||
Neoprene |
Synthetic Rubber |
Oxidizing acids, bases, alcohols, oils, fats, aniline, phenol, glycol ethers |
Chlorinated solvents |
||||
Nitrile |
Synthetic Rubber |
Oils, greases, acids, caustics, aliphatic solvents |
Aromatic solvents, many ketones, esters, many chlorinated solvents |
||||
PVA |
Poly-Vinyl Alcohol |
A wide range of aliphatic, aromatic and chlorinated solvents, ketones (except acetone), esters, ethers |
Acids, alcohols, bases, water |
||||
PVC |
Poly-Vinyl Chloride |
Strong acids and bases, salts, other aqueous solutions, alcohols, glycol ethers |
Aliphatic, aromatic and chlorinated solvents, aldehydes, ketones, nitrocompounds |
||||
Viton |
Fluoroelastomer |
Aromatic, aliphatic and chlorinated solvents, and alcohols |
Some ketones, esters, amines |
||||
Silver Shield |
Laminate |
Wide range of solvents, acids and bases |
3.6.3.2 Hot Objects
When the use of appropriate tongs is not possible or feasible, heat-resistant gloves or mitts should be used when handling hot objects (i.e., metal containers or glassware). Do not use old-style gloves or mitts containing asbestos. Several types of asbestos-free gloves or mitts currently are available. Caution also should be exercised when handling very cold material or objects. See 4.2.5.9 Cryogenic Gases
3.6.4 Hearing (Permitted Exposure to Noise) (OHSA)
No one is permitted to work in an area where the sound level equals or exceeds 115 decibels (dB) unless adequate hearing protection is worn. The protective device must reduce the sound level below the number of decibels listed in Column 1 of Table 6 for the corresponding period of exposure listed in Column 2.
Table 6: Maximum Permitted Sound Level Exposure (OHSA)
Sound level (dB) |
Duration (hours per 24 h day) |
90 |
8 |
92 |
6 |
95 |
4 |
97 |
3 |
100 |
2 |
102 |
1½ |
105 |
1 |
110 |
½ |
115 |
¼ or less |
> 115 |
no exposure |
3.7 Unattended Experiments
3.7.1 Authorization
Permission to operate unattended experiments must be obtained in advance from the supervisor. Normally, authorization will be given only if the experiment does not involve the use or production of toxic or bio-hazardous substances, flammable solvents, highly explosive vapours or gases, the use of high pressures or temperatures, or the use of high levels or radioactivity which may be released if the equipment fails.
3.7.2 Precautions Required
Experiments which are to be left unattended and which involve temporary connections to building water or steam supplies are to:
(a) Use tubing in good condition, and of the proper pressure rating
(b) Have all water hoses wired or clamped at connecting points
(c) Use water lines equipped with a needle valve or other flow-restrictor located immediately next to the main supply line
If possible, all steam, water and gas lines should be equipped with automatic safety shut-offs (e.g., solenoid valves) which are activated in the event of electrical power failure or other experimental problems such as equipment failure.
Note: for high-temperature experiments or those involving exothermic reactions, safety valves on cooling water lines should be of the type which opens fully when activated in emergency situations to provide for continuous cooling of the system.
3.7.3 Identification
A conspicuous notice shall be placed on the equipment used for all unattended experiments. This notice shall provide:
(a) The name, UW extension, and home telephone number of the researcher using the equipment;
(b) The name, UW extension, and home telephone number of the researcher’s supervisor; and
(c) A listing of all potentially-hazardous chemicals (including radioactive substances) or biological agents contained in the experimental system.
3.8 First Aid
First aid facilities and training are mandated by the Workplace Safety Insurance Board (WSIB). Under Policy 34, Health, Safety and Environment, "It is the supervisor's responsibility to ensure that prompt first aid and health care treatment is obtained".
UW Departments are responsible for:
- maintaining first aid stations and reporting their locations to the Safety Office;
- Ensuring first aid stations are readily accessible for the treatment of injured/ill persons. This is normally considered to be within one building storey or two minutes away;
- designating qualified First Aiders for all their work area first aid stations;
- providing Person(s) in Charge to maintain and inspect first aid stations/kits; and
- Providing additional first aid kits in lab, shop, studio, vehicle and satellite maintenance areas.
3.8.1 Procedure for Blood and Body Fluids
- Preliminary first aid should be administered.
- Use non latex gloves from a first aid kit.
- As soon as possible thereafter, all blood and body fluids should be carefully washed off with hot soapy water.
- Call Plant Operations x33793 and inform them that a cleanup of blood and body fluids is required. Give building location and room number.
- To clean surfaces soiled by blood and body fluids, wash with a disinfecting solution, such as bleach, in a dilution of 1 part disinfecting solution to 10 parts water. Gloves should be worn and disposable materials such as paper towels used. Mops should be rinsed in the disinfecting solution.
- Blood and body fluids stained clothing, cloths and other cleaning material should be rinsed out in cold water using non latex gloves and then laundered normally.
- Blood and body fluids stained disposable articles, including gloves should be placed in a plastic bag, securely closed and placed in the regular garbage.
3.8.2 Procedure for First Aid Injury Reporting
All members of the University community must report to their supervisor any injury or illness related to their work or assignments. It is the supervisor's responsibility to ensure that prompt first aid and health care treatment is obtained, if necessary, and that University reports are completed by the end of the next University business day.
- Obtain medical aid if necessary
- Report any injury to your supervisor immediately.
- Complete the Injury/Incident Report with supervisor and forward to the Safety Office, Commissary (COM) Building.
- If you receive health care treatment or lose time from work for a workplace injury, notify the Safety Office as UW must report it to the Workplace Safety and Insurance Board.
- If you have any questions regarding the above contact the Safety Office at x33587.
3.8.3 Procedure for Transportation for a Workplace Injury
UW Departments and supervisors must provide immediate transportation to Health Services, a hospital, a doctor's office, a walk-in clinic or the worker's home, if necessary.
- A UW vehicle should be used, where possible. UW Police may assist with arranging transportation.
- When an employee is transported to a hospital by ambulance it is the University's obligation to pay for the ambulance.
- If an employee receives an ambulance invoice forward it to the Safety Office for payment.
Supplies
- First aid kits and restocking supplies are available at Chemistry Stores, ESC Room 109 ext. 33072 or through a Central Stores Requisition.
- First Aid Emergency Procedures Poster and 911 Phone Sticker are available from the Safety Office ext. 33587.
3.9 Eye/Face Washes and Safety Showers
3.9.1 Location
- Eyewash must be within 11 seconds travel distance and on the same level.
- Path of travel shall be free of obstructions that may inhibit the use of the equipment.
- Location identified by a highly visible sign.
- Location shall be easily accessible and well lit.
3.9.2 Maintenance
- Activated weekly by room occupants.
- Plant Operations to conduct annual inspections.
3.9.3 Selection
- Three versions recommended for UW Campus are shown below.
- For guidance on appropriate version contact Safety Office Ext. 33587.
3.9.4 Use
- All persons who might be exposed to hazardous materials shall be instructed in the use of emergency eye/face wash and shower equipment and procedures for medical assistance.
- Review first aid procedures on Safety Data Sheets for hazardous materials.
- Use only eye/face wash units on the eyes. Showers are for head and body and should not be used for eyes due to higher water pressure.
Table 7: Safety Showers and Eye Washes
![]() ![]() ![]() ![]() |