The thrust which keeps a rocket aloft is generated both in the rocket engine and by accelerating the exhaust gases through a nozzle which further accelerates the flow up to supersonic speeds. What we will be modeling is the flow through the nozzle. It is easy to imagine how being able to model this in a computer can save a lot of time in building experimental models since a virtual model takes a lot less time and effort to build, and numerical experiments can be run quickly for various types of parameter values.
For those of you who are familiar with physics, the fundamental principle at work in providing thrust for a rocket is Newton's third law:
"For every action there is an equal and opposite reaction."
So when we accelerate the exhaust flow an equal amount of force is applied in the opposite direction to the rocket itself.
The idealized supersonic flow nozzle is known as the De Laval Nozzle after the Swedish inventor Gustav de Laval.
The nozzle
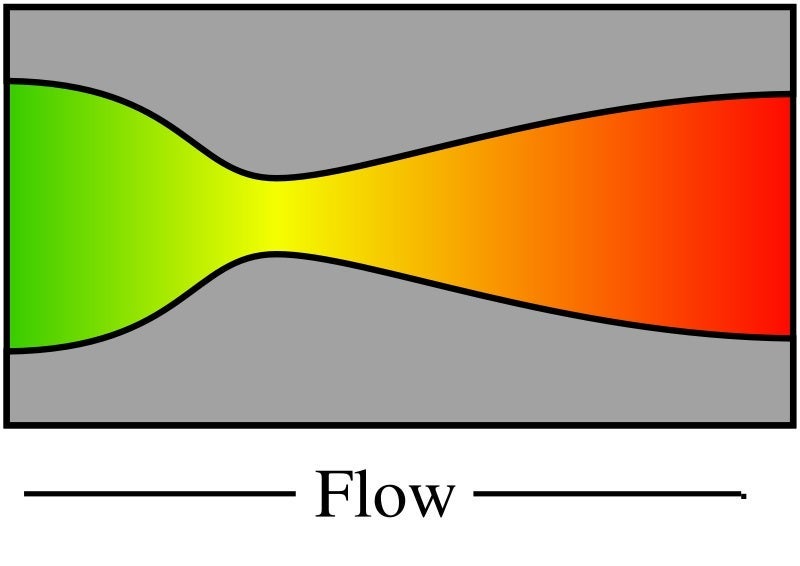
The nozzle is characterized by an area profile that converges to a minimum area and then expands outwards. What is interesting and non-intuitive about this model is that the flow accelerates everywhere in the nozzle! The minimum area point divides the flow into two fundamentally different regimes, one where the flow travels slower than the speed of sound and one where it travels faster than the speed of sound.
In order to visualize the subsonic flow first imagine pinching the nozzle of a garden hose. When you pinch it, the water shoots out faster and farther than before. Whereas the to visualize the supersonic region, however, behaves more like cars driving on a highway. If you lose a lane due to construction the traffic flow slows down but as soon as the obstruction is passed and the highway expands, the flow speeds up.
Building better rockets
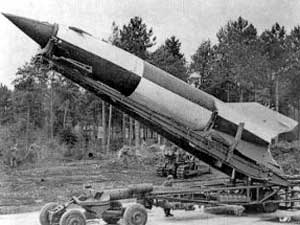
You might think that the key to building better and faster rockets is to simply build bigger and more efficient rocket motors, but as we will see it is not improving the combustion process but channeling the engine's exhaust through a properly designed nozzle that is the best way to get a higher flying rocket. The correct way to design a nozzle was first put forward theoretically in the mid 1800's but the first large scale use of these ideas occurred early out during the second world war.
Werner Von Braun and his German engineers designed and constructed the fearsome V2 rocket which could travel at speeds of up to 5500 km/hour. These same designs and principles were directly employed in building all subsequent space traveling rockets.
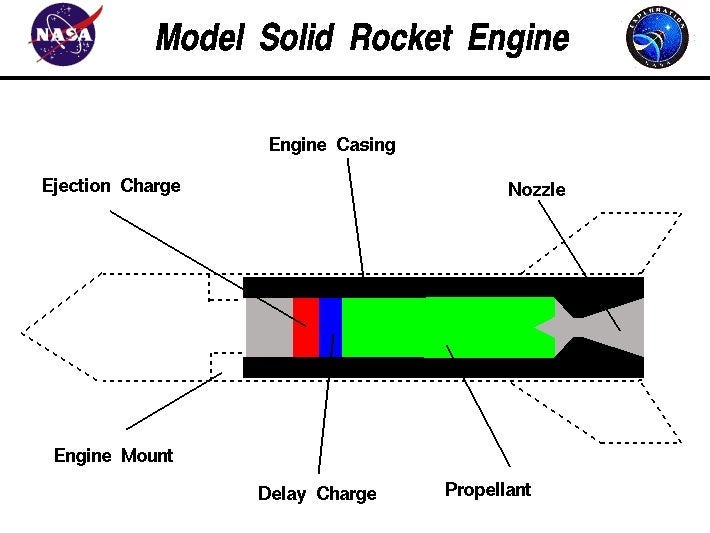
In the diagram you can see a rough sketch of a rocket design. Notice the nozzle at the bottom, which will be the focus of our numerical explorations. If you would like to learn more about rockets, NASA has some wonderful resources or ScienceBits does a very nice derivation of the equations governing water bottle rockets.
The equations describing the supersonic nozzle fall under the general category of differential equations. There exist already many numerical methods for differential equations that compute complete solutions to any desired accuracy from initial data. These algorithms form part of a base set of numerical recipes which can be adapted by Applied Mathematics students when solving specific problems. You can learn a bit more about some of these algorithms, such as the famous Runge-Kutta method for solving.
Below is a plot showing some numerical results obtained, namely the speed of the gas as it travels through the nozzle. The flow velocity is subsonic at first, but becomes supersonic later, thus providing thrust to the rocket.
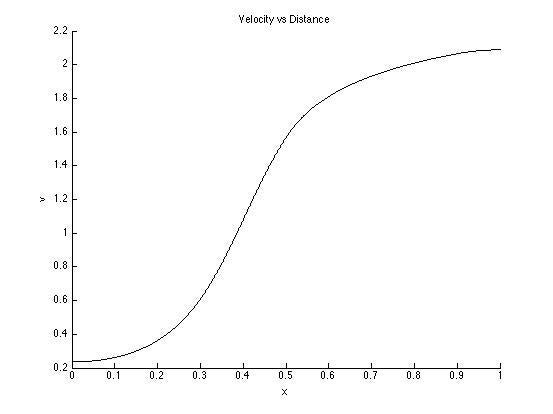