Engineers from the University of Waterloo applied neutron beams in the developing a promising new magnesium alloy. In addition to being cost-effective, the material’s alloying elements ensure increased ductility and strength—paving the way for lighter, more energy-efficient vehicles.
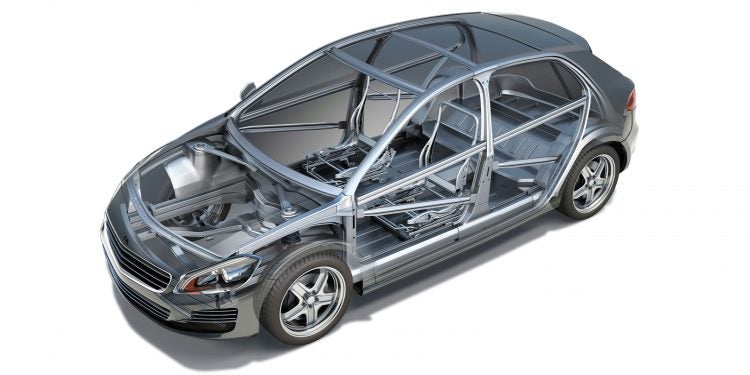
Source: Canadian Neutron Beam Centre (CNBC)
Contact: cnbc@cnl.ca
Image: Cars made with lightweight metals, such as magnesium, help to reduce the environmental impacts of driving. (SSAB)
When compared to their heavier counterparts, lighter cars require less energy to travel the same distance, regardless of whether that energy comes from batteries, hydrogen, or fossil fuels. As a result, lighter cars are also cleaner cars because this energy savings translates into reductions in greenhouse gases and other pollutants. And because they require less energy, lighter cars can be converted more easily to use energy sources other than gasoline.
The prospect of making cars lighter and using alternative fuels are among the motivations for Ford’s recent $1.2B investment in its Canadian research and manufacturing facilities. In fact, all major car makers in North America and Europe are pursuing these objectives to help meet their environmental targets.
Today, the average car needs about 7.4 litres of fuel to travel 100 kilometres. However, that amount could easily be reduced to less than 6 litres just by replacing the car’s steel components with magnesium ones, because magnesium is 80% lighter than steel. In fact, magnesium is the lightest of all engineering metals, and therefore it would present the greatest potential for weight savings if a magnesium alloy with comparable performance were developed.
“Magnesium alloys haven’t been widely adopted by car makers for reasons such as cost, manufacturing limitations, and performance,” says Professor Shahrzad Esmaeili of the University of Waterloo. While all these factors must be considered in the development of new magnesium alloys for the auto industry, overcoming limitations in manufacturing represents the first hurdle.
One of the key characteristics that determines how easy it is for manufacturers to work with an alloy is ductility, which refers to how much it can be stretched without breaking. “The available magnesium alloys are less ductile, and their strength is typically lower than those of steel or aluminum alloys,” explains Esmaeili. “But we have made progress by creating magnesium alloys that alleviate these problems.”
Esmaeili was one of the researchers sponsored by the NSERC Magnesium Network (MagNET), a five-year program launched in 2008 that brought together university, government, and industry expertise to develop magnesium materials for car parts.
Specifically, the team focused on improving the ductility and strength of one particular magnesium alloy (i.e., magnesium alloyed with 4% zinc). Earlier studies had shown that adding cerium to such a magnesium–zinc alloy could improve its ductility, while other findings suggested that incorporating calcium could increase its strength. Thus, Esmaeili’s team added small amounts (i.e., less than 1%) of both cerium and calcium to their alloy to improve its properties—all without significantly increasing the cost of materials, as cerium and calcium are relatively inexpensive.
“We tested the hypothesis that adding both cerium and calcium to the magnesium–zinc alloy would combine their positive effects,” says Brian Langelier, who started working with Esmaeili’s research team in 2008 as a graduate student. “Our initial study showed promising results, but we needed to understand in more detail how cerium and calcium were affecting the alloy’s texture. That’s when we used neutrons.”
Texture, which can have major impacts on an alloy’s ductility, refers to the orientation of the micron-sized crystal grains that make up every alloy. Specifically, an alloy’s ductility tends to be greater when its grains are randomly oriented as compared to when they are lined up in the same direction. To characterize their new alloy’s texture, the researchers relied on neutron beams at the Canadian Neutron Beam Centre (CNBC), as neutrons are uniquely capable of penetrating deep inside an alloy to determine the orientation of its grains.
Combining the results from the neutron beam analysis with those gained from electron microscopy, Esmaeili’s team published a paper in 2015 which demonstrated that cerium and calcium were randomizing the texture and modifying the grain size of their new alloy. In addition to providing explanations for the observed improvements in the alloy’s ductility, the data also offered insights into how the alloy might be optimized.

Pole figures, determined by neutron beam analysis, indicate a more ‘randomized’ texture for the alloy with cerium and calcium (Mg-Zn-Ce-Ca, left) as compared to without cerium and calcium (Mg-Zn, right). When many grains are oriented in the same direction (indicated by red or orange spots), ductility is reduced.
With many questions about the alloy’s ductility now answered, Esmaeili’s team began to address the issue of strength. To do so, they adopted an ‘age hardening’ approach, which is commonly used to increase the strength of some aluminum alloys. Age hardening involves heating the material to cause the formation of nanometre-sized ‘hardening particles.’ These particles help to increase a material’s strength by inhibiting the movements of certain structural defects within the grains when the material is exposed to a substantial force. However, age hardening can also increase the potential for fracturing if the hardening particles are not distributed uniformly.
Esmaeili’s team applied age hardening to an array of magnesium–zinc alloy samples, including some with both cerium and calcium, some with only cerium or calcium, and some with neither. The researchers conducted systematic comparisons to understand the resulting changes to the samples’ strength using a number of experimental techniques. They shared their three main findings in a series of papers published in 2015, 2016, and 2017.
First, the researchers found that the effectiveness of age hardening was actually reduced in samples where only cerium was added as compared to the original magnesium–zinc alloy. However, they overcame this limitation by designing a preparation step that successfully eliminated this unwanted effect. Second, they found that the presence of both cerium and calcium significantly improved the effectiveness of age hardening by increasing the capacity of the magnesium–zinc alloy to form hardening particles. Finally, after examining the alloy’s microscopic structure, they concluded that adding calcium improves the uniform distribution of these particles, thereby helping it to resist fracturing.
Taken together, the insights provided by the four studies demonstrate a scientific foundation for better understanding such magnesium–zinc alloys and their potential applications. Esmaeili and her fellow researchers are currently examining additional processing methods that could further improve their alloy’s performance for use in cars in the future.