Table of Contents
9. Safety Inspections
Laboratory safety inspections are critical for maintaining a safe and productive working environment. These inspections help identify potential hazards, ensure compliance with safety regulations, and prevent accidents or incidents that could result in injury, illness, or damage to equipment and facilities.
Regular safety inspections foster a culture of safety, promote awareness among laboratory personnel, and are essential for safeguarding the health and well-being of all individuals working in or around the laboratory. By proactively addressing risks, laboratory safety inspections play a vital role in preventing accidents and ensuring that the lab operates smoothly and efficiently.
There are many types of safety inspections in Chemical Engineering Laboratories, such as the ones conducted by the Joint Health and Safety Committee (JHSC), the Chemical Engineering Health and Safety Committee, the Supervisor, and outside authorities.
Keep in mind that as part of their daily workplace activities, all members of the campus community are responsible for reporting or correcting hazardous conditions. Hazardous conditions should be reported directly to the supervisor.
The result of a laboratory safety inspection is a report outlining the findings of the inspection. This report contains the following elements:
- Identified Hazards: A list of any safety hazards or non-compliant practices discovered during the inspection, such as improper chemical storage, lack of personal protective equipment (PPE), or faulty equipment.
- Recommendations: Specific corrective actions that need to be taken to address the identified hazards. These recommendations may include changes in procedures, additional training, or repairs and maintenance of equipment.
- Timeline for Corrections: A timeframe within which the recommended corrective actions should be completed. High-risk hazards should be addressed within 24 hours, while medium and low-risk hazards should be resolved within two weeks. This approach ensures that safety issues are promptly and effectively managed.
In the Department of Chemical Engineering, supervisors are required to conduct Laboratory Safety Inspections monthly as part of the Occupational Health and Safety Act requirements. These inspections may be delegated to a competent person; however, the Supervisor remains responsible for ensuring that the inspections are conducted, hazards are identified, and the corrective actions are implemented.
Additionally, the Chemical Engineering Safety Committee conducts laboratory safety inspections in all labs managed by the department once per term. The goal of these inspections is to assist Lab Supervisors in identifying hazards.
Both the Supervisor and the Chemical Engineering Safety Committee use a custom version of the Inspection App on Microsoft Teams to document the results of the inspections and track the completion of the corrective actions. The checklist used during the safety inspections can be found in the link below.
Chemical Engineering Lab Inspection Checklist
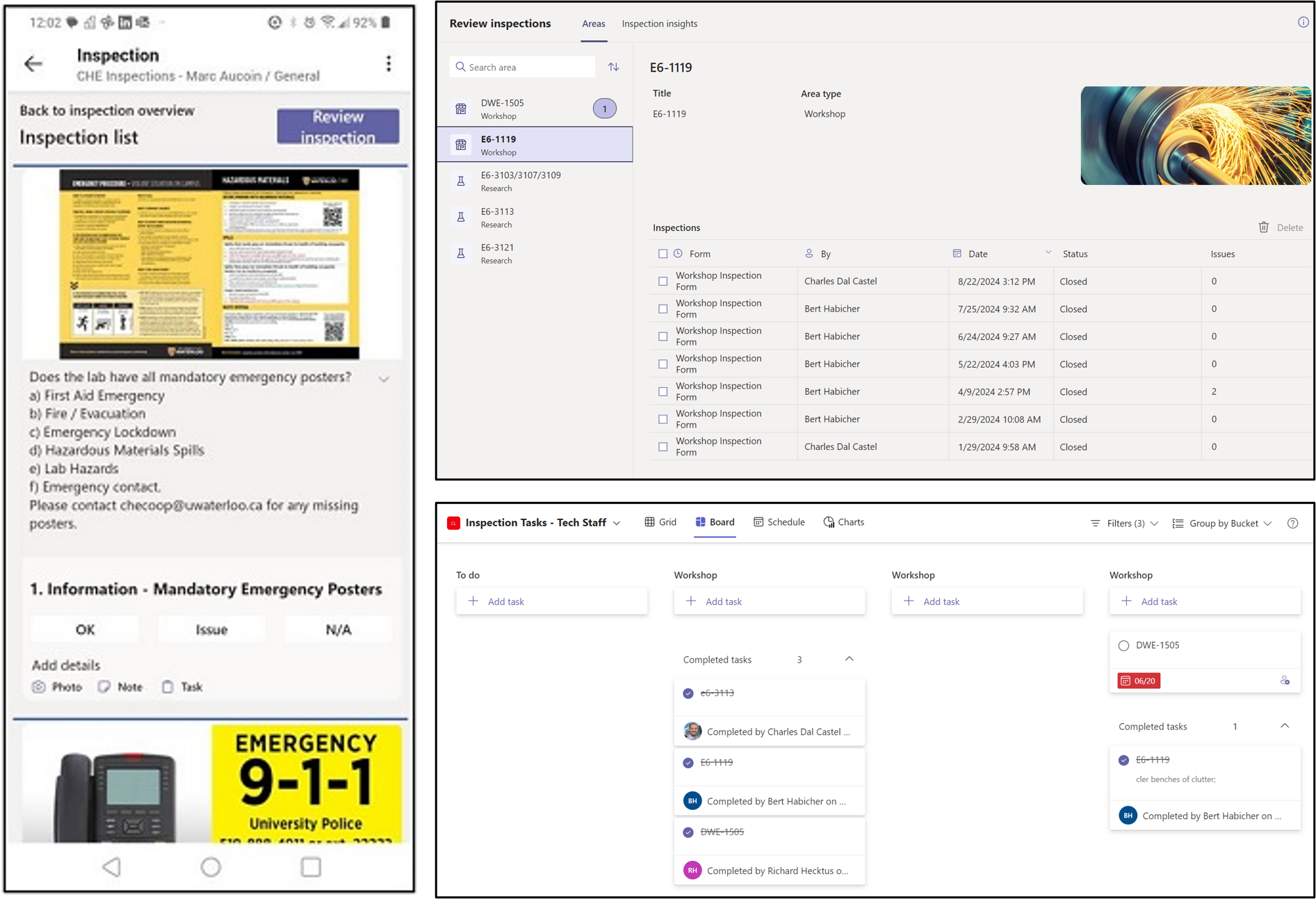