Waterloo students build unique experiences working in manufacturing industry
By: Namish Modi
University of Waterloo co-op students like working for manufacturing organizations because they work in cross-functional roles, develop dynamic skills and may secure multiple jobs at the same organization.
Students bring their dynamic skills to a variety of facets that come with working in an important industry, including in production, on the floor or in the office.
Three Waterloo co-op students; Tiana Krsmanovic, Hannah Rivers and Shawn Pang, told us about their co-op experience at ATS Automation Tooling Systems Ltd.
Hannah Rivers
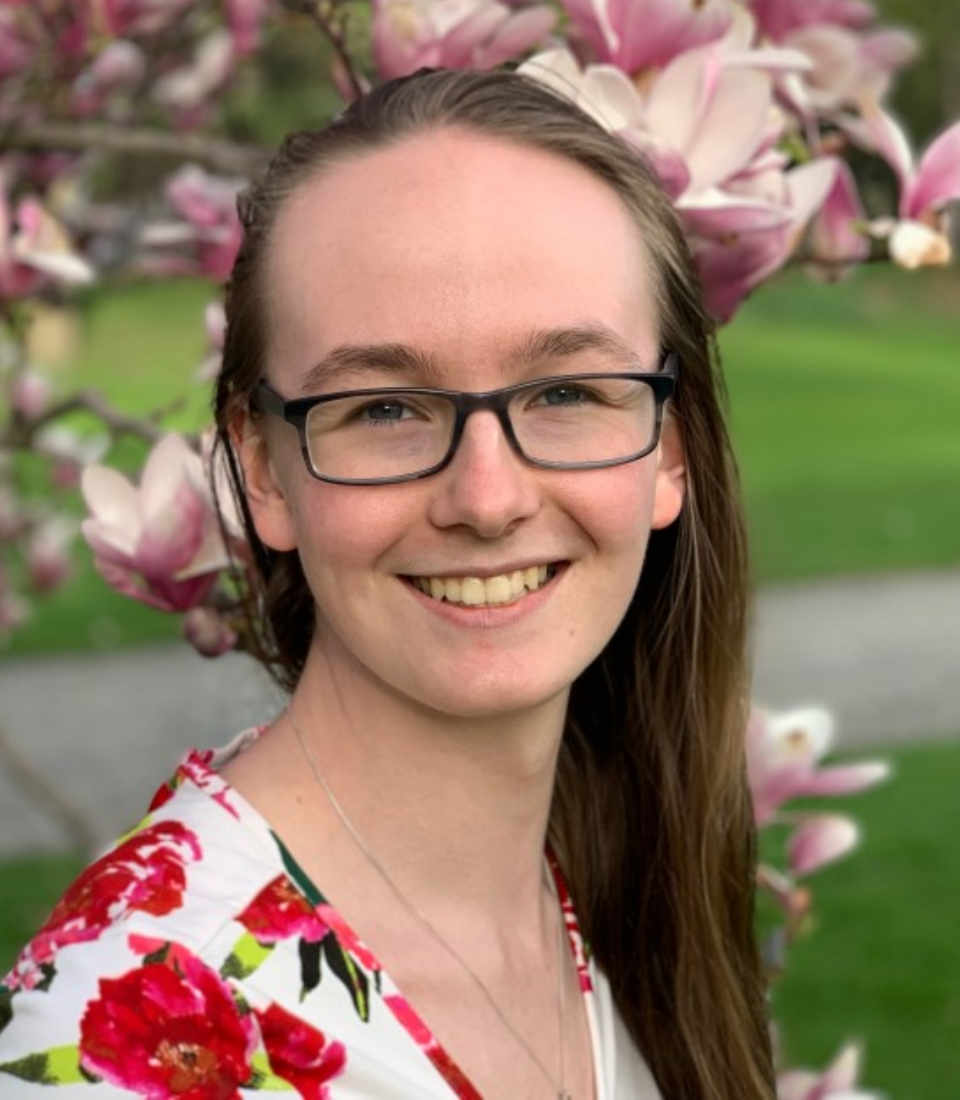
“It’s such an interesting environment to me, that I keep coming back,” says Rivers, a fourth-year Systems Designs Engineering student who worked in engineering systems support at ATS Automation this past winter.
Previously, Rivers worked for Kruger Products on a work term, and as an assembly line worker as part of a non-co-op experience. She says working for a manufacturing organization gives students an opportunity to understand how “things are kind of made in this world.”
“Each of my co-op terms or work terms in manufacturing has allowed me a little bit more insight into what the world of manufacturing is like,” Rivers said.
At ATS Automation, Rivers worked in the IT department, supporting incoming support ticket requests to help mechanical designers with any software problems. Prioritization was a key skill that Rivers developed in the role.
“I also learned a little bit about mechanical design when I was working with some of the designers there,” Rivers adds.
Rivers is a proponent of gaining a variety of experiences during co-op terms and recommends manufacturing organizations as an area with lots of opportunities for students.
My role at ATS has given me lots of insight into what I want to do in terms of my career and what I want to do when I graduate. Every co-op (term) for me is a new opportunity to learn what I like and what I don’t like. With ATS, I got a little bit of both. I learned that I really like the design aspect, in terms of manufacturing, rather than the IT aspect.
Tiana Krsmanovic
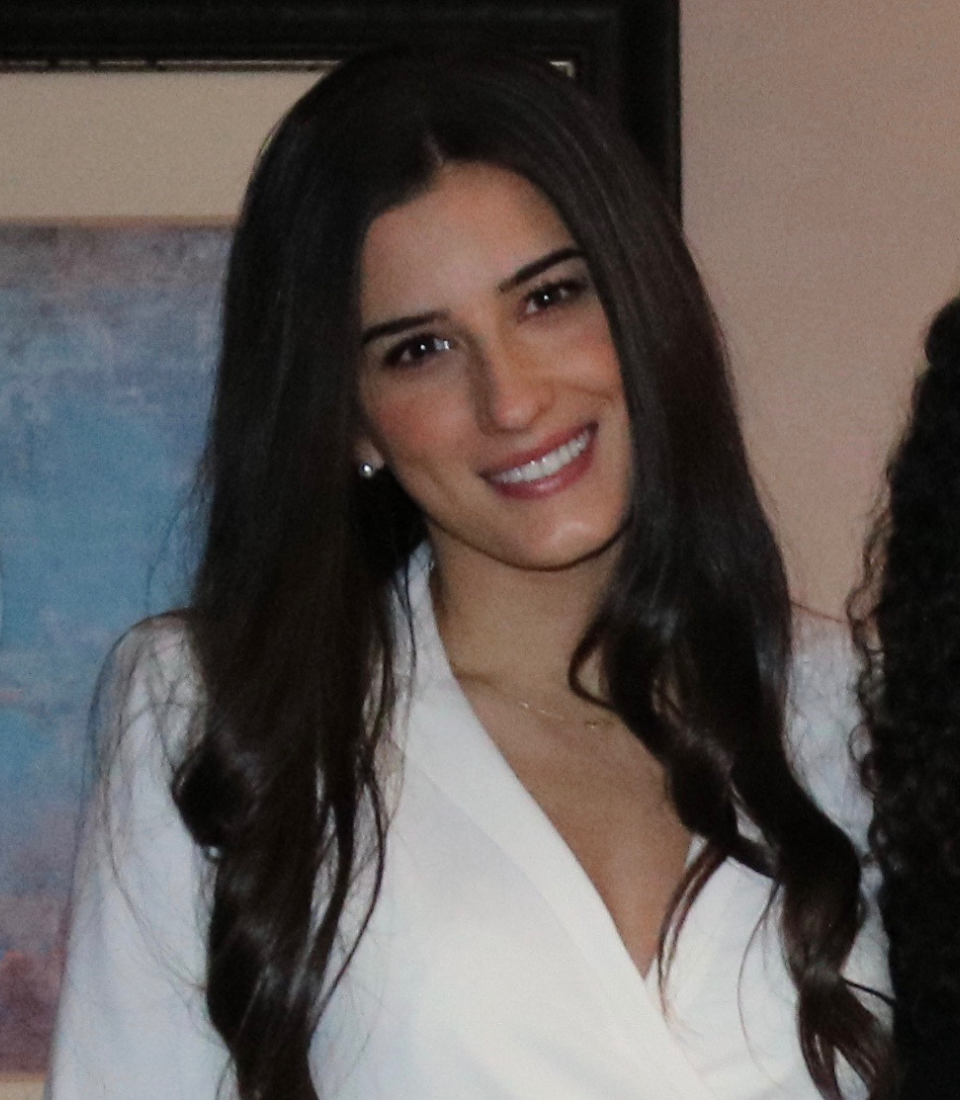
Krsmanovic, who worked at ATS Automation as a human resources coordinator during her Winter 2020 work term, says she was a bit surprised at the opportunity. Previously, she believed manufacturing roles were solely for Engineering students. Instead, during her work term at ATS Automation, she assisted with career planning modules, training, recruitment and health and safety compliance.
Being a good presenter and thinking creatively and analytically were key to her role at the organization.
Krsmanovic, whose work term transitioned to remote in March 2020, says she was happy to have some unique experiences when the position was in-person, like seeing the shop floor.
I picked up so much on this co-op, and I worked with so many different people. That was huge, because at that point, you only have about four months of co-op experience. But even in that shorter timeframe, where it got cut shorter because of COVID, every day was so productive.
Krsmanovic isn’t overlooking working in a manufacturing company in the future. She is currently working in project management at Gore Mutual Insurance for her fourth co-op term.
Shawn Pang
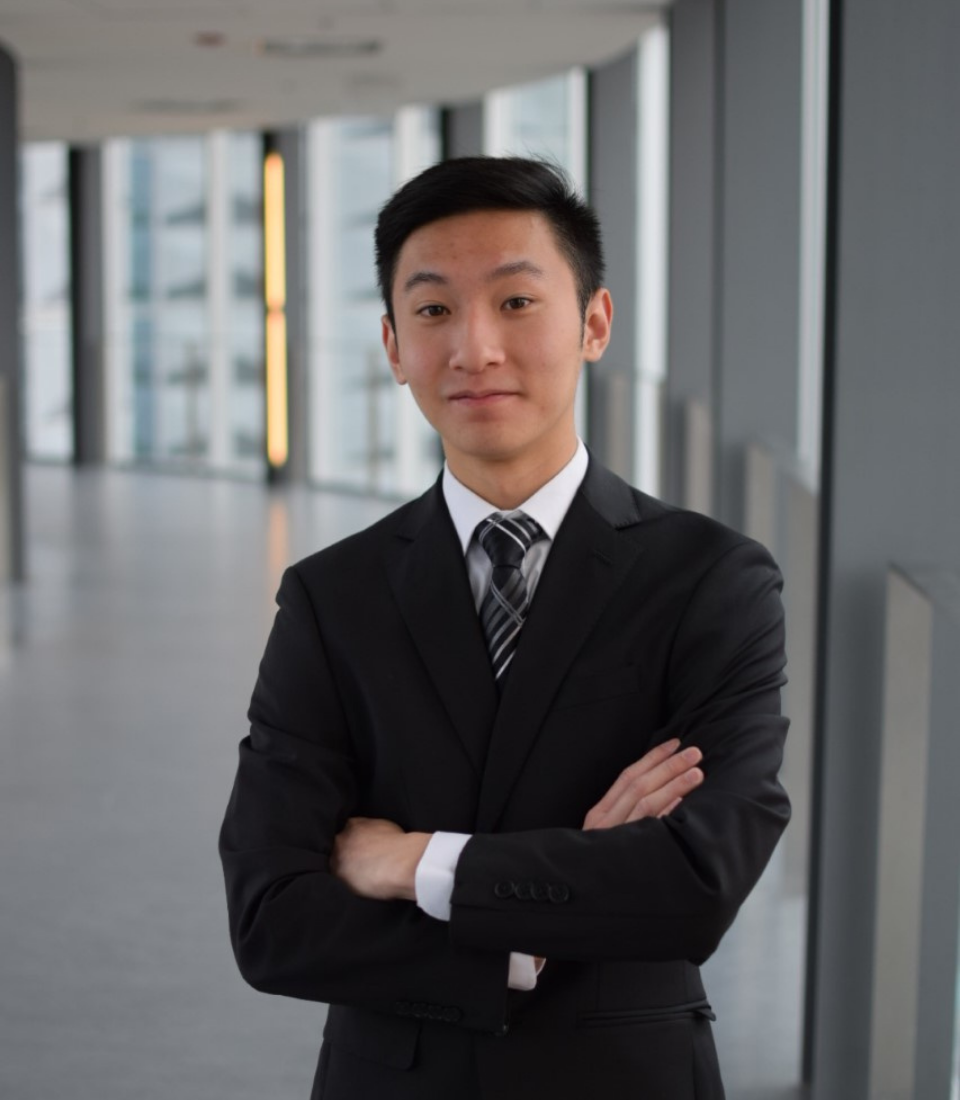
His preceding three co-op terms were in supply chain at Pepsi. Before that, Pang worked as a line worker in food manufacturing in his first work term.
All five of Pang’s work terms were in manufacturing but were vastly different.
“I think because of the hybrid crossover knowledge I have; it makes me kind of flexible in such roles,” Pang adds.
He finds that the manufacturing environment is more likely to retain co-op students for multiple co-op terms, due to stringent training processes.
He says working in a front-line role helped teach him good manufacturing practices and about the industry in general. It helped prepare him progress into different types of roles.
At Pepsi, it was more of business and front-line leadership role. He enjoyed multiple work terms at the organization, and it prompted him to stay in the supply chain field, for his next co-op work term. At ATS, he works in data analysis where he has gained a stronger ability to understand process improvements in the workplace. Pang says the different roles require different skills, including leadership.
I think [leadership] is a trait that employers look at, to see whether you’re able to lead a team of people and achieve results. I think willingness to learn is very important, so don’t limit yourself to your area.
Like Rivers, Pang believes co-op is the perfect opportunity for students to test out their preferences and form long-term goals.
“I would like to encourage everyone to not be afraid of trying something that’s out of your comfort zone, because co-op is the only time pretty much in your life where you can try whatever you would like to, but you’re not sure about.”
Waterloo students with different levels of experience bring their skills to various levels of a manufacturing organization, including at the front line.