Imagine being able to clean your driveway and charge your cell phone at the same time – using the same piece of equipment.
Behrad Khamesee, a Waterloo mechanical and mechatronics
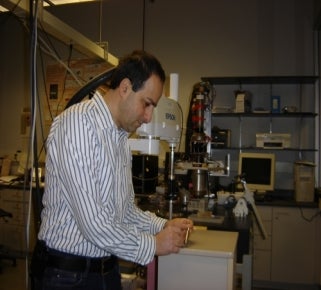
This unique form of multi-tasking is possible through a 3D multi-directional energy harvester Khamesee says is the first of its kind.
“What makes it different is that it’s a single unit unlike other multi units that have been developed,” says Khamesee. “Our patent-pending electromagnetic energy harvester system with converting multi directional motion into linear motion shows the feasibility of harvesting energy regardless of the direction of the vibration, while most existing harvesters can only harvest energy in one direction.”
Less expensive, lighter and easier to install
The technology will continuously recharge batteries through vibrations caused by motion. Because just one unit is required instead of the usual three, the developed technology is more cost efficient, much lighter, and easier to incorporate into devices or mounted directly onto machines such as a snowblower or lawnmower. It may also be strapped onto an arm or leg to produce energy while walking or biking.
It may also be used to shed light on guiding the way for snowboarders and other outdoor sport enthusiasts in areas where access to energy isn’t available.
“The technology can be used for safety and other reasons to power LED lights fastened to a snowboard, skis or other recreational equipment by capturing the energy created by the user,” explains Khamesee. “It can also light up licence plates on vehicles and eliminate the expensive wiring now used.”
Other potential uses for the harvester include health monitoring devices and wireless sensors for detecting cracks and damage to buildings and bridges.
Khamesee and Patel, who recently graduated with a master’s degree in mechanical engineering, spent about six months developing the 3D version of their research. And they didn’t need to go far for some of the parts for their prototype – many were designed and produced using the 3D- printer located in Engineering 5’s Sedra Student Design Centre.