It’s not often that you’ll see an indoor pedestrian bridge – especially one that’s 70 feet long and made from aluminum.
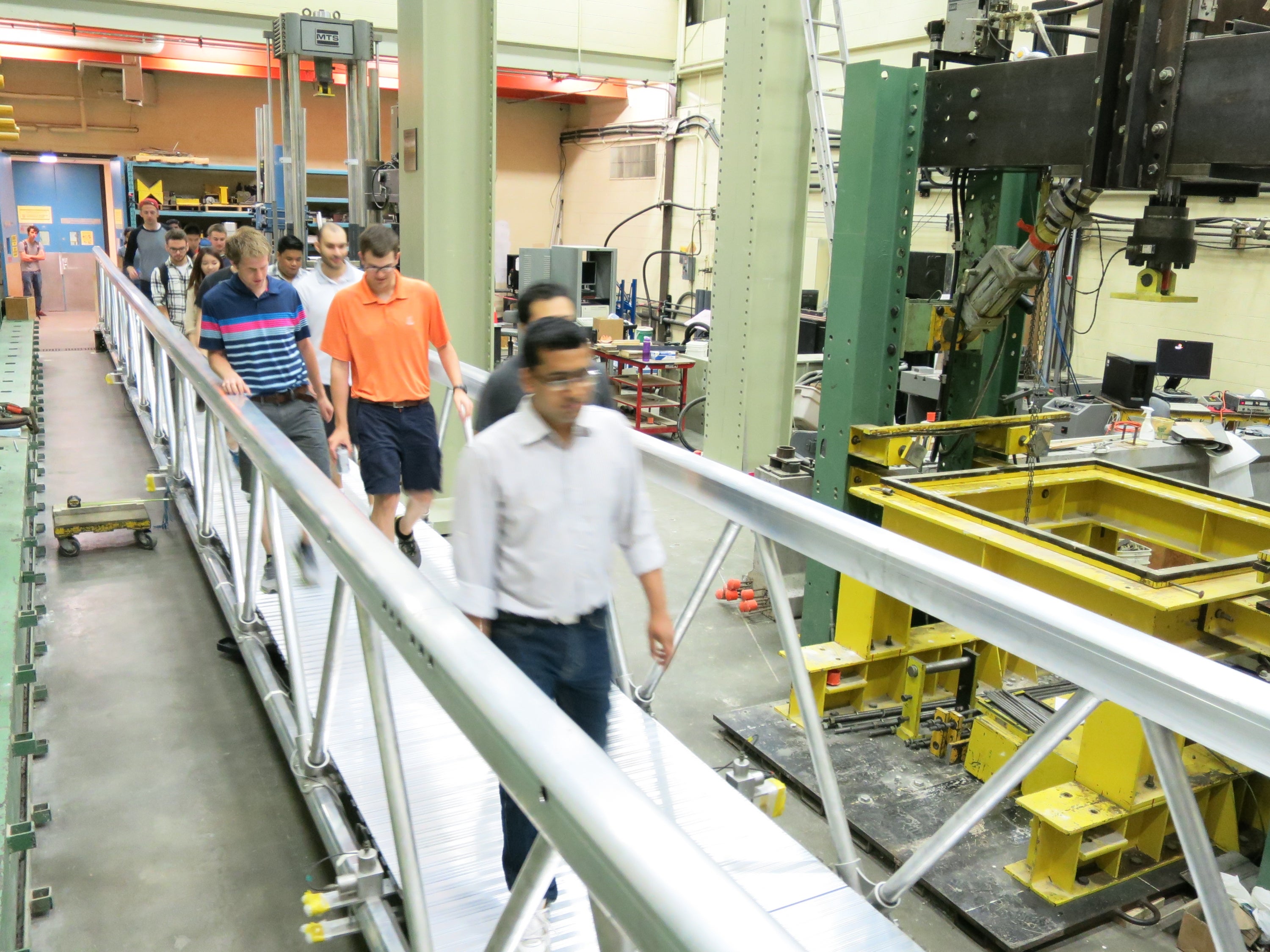
But that’s what you’ll find currently set up in Waterloo’s civil and environmental engineering’s structures lab.
There, a team led by civil and environmental engineering professors Scott Walbridge and Sriram Narasimhan is collecting vibration data to develop better models for simulating crowd loads on similar structures and discover ways to make aluminum pedestrian bridges more economical.
One of the unique things about this bridge system is that it’s modular so we can make it various lengths to see how the vibration behaviour changes according to the different lengths. — Professor Scott Walbridge
The
bridge
is
equipped
with
four
load
cells
to
accurately
record
the
load
and
12
accelerometers
to
measure
the
accelerations.
To
help
with
the
testing
various
groups,
including
a
class
of
Grade
4/5
students,
have
been
walking
and
running
along
the
bridge.
Earlier
this
month,
29
civil
engineering
students
took
their
turn
crossing
the
structure
multiple
times.
Watching them in action were industry partners Jacques Internoscia of the Aluminum Association of Canada, and Alexandre de la Chevrotière and Simon Lacasse of the Most Advanced Aluminum Design and Inspection (MAADI) Group, the company that built and donated the bridge.
Walbridge's interest in aluminum bridge research piqued when he became involved with the Canadian Bridge Design Code and was part of the committee that in 2011 released the first rules for designing aluminum bridges in Canada.
It was on that committee that he met de la Chevrotière, the president of the MAADI Group, who was so impressed with the research being done in Waterloo Engineering that he soon became an industry partner. It was de la Chevrotière who reached out to the Aluminum Association of Canada to help fund the project.
Aluminum advantages
The advantages of using aluminum rather than the concrete and steel are that it’s lightweight, more durable – it won’t corrode or degrade over time – and has the potential to last much longer. Aluminum bridges can also be prefabricated resulting in quicker installation and reduced delays for users.
But there is a downside, points out Narasimhan.
They come with a set of problems that stiffer concrete and steel bridges generally don’t have, which is they’re very sensitive to people walking on them. So we need to figure out how to better predict how they perform if they do exhibit this lively behaviour that you see right now. — Professor Sriram Narasimhan
Two
of
Narasimhan
and
Walbridge’s
civil
engineering
graduate
students
have
been
working
on
the
project
for
almost
two
years.
Ann
Sychterz,
a
master’s
student,
and
Pampa
Dey,
a
doctoral
candidate,
have
completed
preliminary
full-scale
testing
in
the
field
and
on
the
model
bridge
they
helped
set
up
in
the
lab
last
month.
“Seeing
the
lateral
movement
is
fun
and
eye-popping
at
the
same
time,”
says
Sychterz,
who
along
with
Dey,
organizes
the
students
walking
across
the
structure.
The
bridge,
which
Narasimhan
says
is
the
first
full-scale
modular
kind
in
the
world,
will
be
dismantled
before
the
end
of
July
and
moved
to
another
location
in
engineering.
Next steps include analyzing the testing data, refining predictive models based on findings, and recommending changes to the way aluminum bridges are designed.