Researchers at the University of Waterloo are joining a major effort to help make Canadian manufacturers more competitive through the use of computer modelling.
Led by Kaan Erkorkmaz, a professor of mechanical and mechatronics engineering, the Waterloo team is in line for $1.3 million in funding over five years to tackle complex issues in advanced manufacturing.
Its work is part of an overall research project – the second phase of the Canadian Network for Research and Innovation in Machining Technology (CANRIMT) – involving 17 professors at seven universities and a total of $8.3 million in funding from all sources.
'It's the thrill of exploring'
“It’s super exciting because we’re running at the frontier of the technology,” said Erkorkmaz, the lead in digital machining, one of five themes or areas of research. “It’s the thrill of exploring, of finding out.”
Announced today, the funding is being provided by the federal government through the Natural Sciences and Engineering Research Council of Canada (NSERC), national and international industry partners, and participating universities.
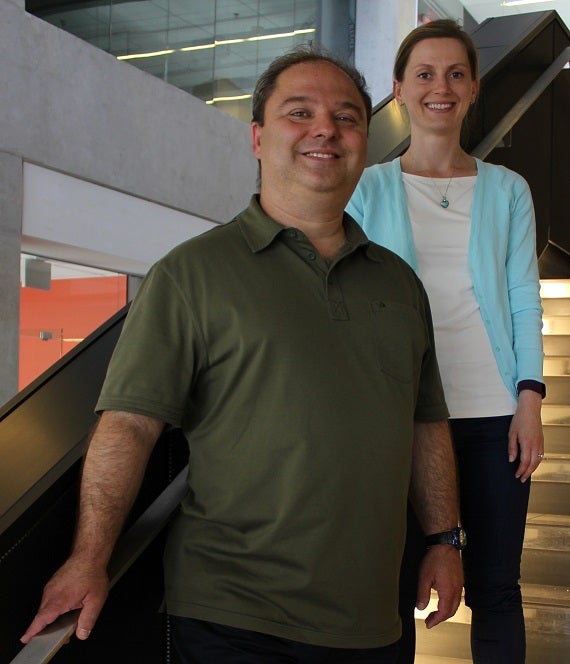
The lead investigator for a network focused on strategies for dealing with hazardous mine wastes is David Blowes, a Waterloo professor of earth and environmental sciences, and Canada Research Chair in Groundwater Remediation.
The goal of the manufacturing network, led by principal investigator Yusuf Altintas of the University of British Columbia, is utilizing virtual computer models of machines and manufacturing processes to improve quality and productivity while also reducing labour and material costs.
Although modelling for simpler, established processes such as milling, turning and boring has been in use for about 15 years, CANRIMT seeks to extend it to extremely complex machining and additive manufacturing operations, colloquially known as three-dimensional printing.
'Digital twins' save time, money
Erkorkmaz said the development of “digital twins” of manufacturing equipment enables monitoring and adjustments without costly down time or material waste. In effect, optimal settings can largely be determined on computers, minimizing disruption to the actual machines.
Models employing a sophisticated, physics-based approach can be applied in the same way to manufacturing processes, such as precisely how a cutting tool interacts with the metal it is shaping.
“Massive digitization is coming,” said Erkorkmaz, citing similar efforts in industrialized countries around the world. “You can either lead it or follow it. This will allow us to keep jobs here, basically.”
The work at Waterloo Engineering will also involve mechanical and mechatronics professor Mihaela Vlasea and at least 15 graduate and co-op students.
'We're checking off a lot of goals'
“It’s a tremendous opportunity for us to train students, develop expertise and build virtual tools that can help industry,” said Vlasea. “We’re checking off a lot of goals.”
The team’s research will focus on: computer modelling of complex machining, especially gear production; exploring how machining and additive manufacturing can best work together; and building virtual models and control techniques for machines, including laser drilling and the reduction of unwanted vibrations.
Work in the area of additive manufacturing will build on expertise developed at Waterloo over the past 15 years, including the development of a machine that uses metal powder and a powerful laser to shape it.
“You’re essentially drawing with metal,” said Vlasea, who will focus on that area of research. “You’re printing a part in layer-by-layer fashion.”