Ontario’s Regulations for Industrial Establishments defines a lifting device as “a device that is used to raise or lower any material or object and includes its rail and other supports”. This definition covers a wide range of equipment, including:
- All lifting attachments on mobile equipment
- Overhead cranes
- Rigging accessories (e.g., slings, chains, wire ropes)
- Forklifts (includes pallet trucks)
- Winches
- Scissor lifts
- Hoists
- Jacks
All lifting devices used on campus must be registered with the Safety Office and undergo an annual inspection. See below for more information.
Inspections
All lifting devices on campus must be inspected annually by a certified lifting device inspector through the Safety Office. Lifting devices that have been inspected will have a sticker similar to the image below. On devices where an inspection sticker can't be applied (e.g., slings, hooks, chains), lifting device inspectors will use a paint marker or bracelet to identify the inspection has taken place.
Please advise the Safety Office if the lifting device in your area has no sticker, paint mark or bracelet. The Safety Office will add your lifting device to the inventory and assist with scheduling an inspection.
To register your lifting device or if you are unsure if the device may be a lifting device, contact the Safety Office.
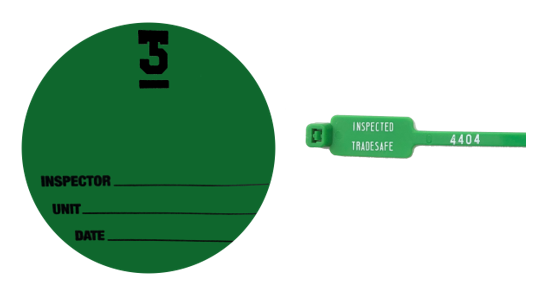
Purchasing lifting devices
- How familiar are you with the equipment supplier? Purchasing lifting equipment from reputable, certified companies helps ensure the equipment meets the Ontario laws and regulations governing overhead lifting equipment. Having references, permits, and certificates helps ensure you are working with trusted suppliers.
- Is this the right equipment for the job and facility? Work with the supplier to ensure you understand the classification and specifications of lifting and hoisting equipment. If the equipment will be attached to a building or structure, you must also ensure that structure can accommodate the installation of the lifting system and is approved for installation under Policy 22 with the rated load the application.
- Does the equipment require an Electrical Safety Authority (ESA) inspection? If the new equipment has electrical components, or requires modification to existing equipment with electrical components, an ESA certification is required to ensure it complies with requirements defined in the Ontario Electrical Safety Code.
- Always complete a pre-use inspection. Pre-use inspections are required before use of any equipment or work process that has a potential to result in a severe loss. This review identifies safety concerns and evaluates potential hazards. It also defines what measures need to be taken to bring the identified deficiencies into compliance.
- Register your lifting device with the Safety Office. Once a device is purchased, if it requires annual inspection it must be added to the University’s inventory of lifting equipment. Contact the Safety Office to register your lifting device.
Legislation - industrial regulations
Material Handling
45. Material, articles or things,
(a) required to be lifted, carried or moved, shall be lifted, carried or moved in such a way and with such precautions and safeguards, including protective clothing, guards or other precautions as will ensure that the lifting, carrying or moving of the material, articles or things does not endanger the safety of any worker;
(b) shall be transported, placed or stored so that the material, articles or things,
(i) will not tip, collapse or fall, and
(ii) can be removed or withdrawn without endangering the safety of any worker; and
(c) to be removed from a storage area, pile or rack, shall be removed in a manner that will not endanger the safety of any worker.
51. (1) A lifting device shall,
(a) be so constructed, of such strength and be equipped with suitable ropes, chains, slings and other fittings so as to adequately ensure the safety of all workers;
(b) be thoroughly examined by a competent person to determine its capability of handling the maximum load as rated,
(i) prior to being used for the first time, and
(ii) thereafter as often as necessary but not less frequently than recommended by the manufacturer and in any case, at least once a year, and a permanent record shall be kept, signed by the competent person doing the examination;
(c) be plainly marked with sufficient information so as to enable the operator of the device to determine the maximum rated load that the device is capable of lifting under any operating condition;
(d) have a cab, screen, canopy guard or other adequate protection for the operator where the operator may be exposed to the hazard of falling material;
(e) when it is a pneumatic or hydraulic hoist, have controls that automatically return to their neutral position when released.
59. Except for the purpose of a test of the material handling equipment, no material handling equipment shall be loaded in excess of its maximum rated load.
Training
Forklifts
In order to operate a powered forklift on campus, University staff must first complete Forklift Training Theory (SO1027) and then schedule and complete a practical assessment.
Crane operator
Crane Operator Training is designed for crane operators and the supervisory personnel responsible for the daily operation and safe performance of cranes. The training provides participants with the working knowledge to assist in reducing operation errors that may lead to unnecessary downtime. Crane operator training can provide additional knowledge to help avoid possible serious injury to personnel caused by improper crane operation. Participants will learn the requirements of local regulations for crane operation.
Benefits:
- Can improve operator knowledge and performance, reducing the risk of human-error downtime
- Can keep personnel updated on technology and process changes to minimize the impact of operation changes and employee turnover
Contact the Safety Office for more information on crane operator training.
Slings
Inspection of Slings and Chains (SO1035)
Resources: